While dedicated handlers have gained in popularity, tractor front loader use is still the dominant materials handler system on farms today.
Loader capacities and features have generally evolved in line with tractor development. By and large, the principles of tractor front-loader design remain the same today as they did a handful of decades ago –ultimately, converting a conventional tractor into something akin to a self-propelled Swiss-army knife.
There are a huge number of old tractor-mounted front loaders still working effectively on farms around the country. There are even many trip loaders that would have been given a new lease of life, having been converted to hydraulic implement operation.
A number of firms even offer a quick-attach, euro-hitch implement frame conversion to bring older loaders with pin-mounted implements further up to spec.
One feature often overlooked is the addition of a little comfort. All manufacturers of tractor-mounted front loader on the market today offer some form of loader suspension. While this is generally an option, it is one almost everyone specified when buying a new loader.
While called different names by various manufacturers, all tractor-loader suspension systems are based on the same principle and act on the loader’s hydraulic system. Plumbed into the loader’s hydraulic lift rams is a gas-filled accumulator.
There are two main designs of accumulator. Both use gas, which unlike a liquid can be compressed as a method of providing a suspension system.
The gas used is generally nitrogen which is almost inert so will not react with the oil in the system if there is a leak between the gas and oil side of an accumulator. Oxygen on the other hand, when combined with oil under high pressure, can form an explosive mixture. That’s the reason why oxygen in gas cylinders used for heating and cutting should never be used to charge or test an accumulator in a hydraulic system.
By far the most common accumulator design is almost round or slightly cylindrical. This uses an elastic diaphragm to keep the oil separate from the gas.
The second design resembles a hydraulic cylinder or ram. The gas is in one end separated from the oil by a floating piston in the cylinder. This design has a higher oil capacity, but is more expensive. It is generally used on larger equipment, such as dedicated materials handlers. Its use has crept in on some tractor loaders too.
Mentioned earlier, it is likely that most new tractor front loaders will be fitted with an accumulator-based suspension system. Older loaders without suspension can benefit greatly by fitting some form of suspension or soft-drive system.
McHugh Components in Dublin is one company to offer the makings of a soft-drive system. There are many others as well that could offer such as system but, for this exercise, the Irish Farmers Journal teamed up with McHughs to fit a system to a 1995 Tanco T100 loader.
We have to mention that while McHugh components is a major parts supplier to the agricultural machinery and manufacturing industry, it does not supply directly to the consumer. Its network of dealers throughout the country is extensive, so there should be no problem sourcing part or all of a soft-drive system. Again, there are many other firms that could potentially supply a soft-drive system as well.
Fitting
We all know what it is like to travel over rough terrain or road with a tractor loader. When the tractor hits and rises over a bump in the road or yard, the loader – if fixed solidly – will rise with it and no doubt return with a bang. With an accumulator plumbed into the hydraulic circuit, the tractor rises but the weight of the loader compresses the gas within the accumulator, vastly reducing the effect of the loader returning to earth.
Fitting a soft-drive system will vary from loader to loader. This exercise with the Tanco T100 is to show that it can be done and is well worth doing.
As with all practical exercises, if in doubt don’t do it. Hydraulic oil under pressure can penetrate the skin and cause blood poisoning. Releasing a hydraulic pipe under pressure can also cause a loader or implement to drop with potentially lethal consequences.
Oil itself is an irritant, so wear suitable gloves and eye protection.
If you feel that the job is outside of your comfort zone of capabilities, your local mechanic or garage will only be too happy to fit a system for you. They should be able to provide you with a guide price to allow you to be able to budget for the job.
Tractors with high capacity hydraulics systems may require an accumulator on both side of the lift ram or leak back valve in the loader control valve block. Older tractors or tractors delivering 30 to 40 litres/min for loader operation will not require such systems.
They will rarely be able to fill the down side of the main lift/lower rams with oil in regular use. This leaves some empty space for the ram to move upwards when the suspension system is switched on and the loader is ‘‘bouncing’’.
Picture one

There are different size and capacity accumulators but pictured here is typical of what you could use on a tractor front loader. The unit on the left has an oil capacity of approximately half a litre and the unit on the right approximately three-quarters of a litre. McHugh Components offers two systems, one with a manual shut-off lever and the other with an electrically operated solenoid cut-off valve.
Picture two
Charge pressures vary and will have an effect on loader suspension performance. This unit is charged to 30-bar and is typical of what works. Some manufacturers plumb two accumulators into the circuit, charged at different pressures to offer a broader range of loader suspension.
Picture three

This is the kit we will fit to the Tanco T100, which has double-acting lift cylinders. All that is required in addition to the soft-drive kit is a length of hydraulic pipe, plus a tee to plumb into the main lift cylinder circuit.
Picture four
We fitted the accumulator on the left side of the T100 loader because there is room to bolt the accumulator to the loader saddle on this side. It is also relatively close to where we tap into the lift cylinder hydraulic circuit.
Picture five

We marked out, drilled and tapped holes to bolt the accumulator bracket directly on to the lefthand saddle. Pictured are the M8x20 bolts used, M8x1.25 (pitch) and stage one and stage two taps. The drill bit required for the hole is 6.5mm.
We drilled and tapped holes because it was the tidiest option (you can buy drill bits and taps individually at most engineering outlets). Alternatively, you could make and weld a simple bracket on to the loader.
Picture six
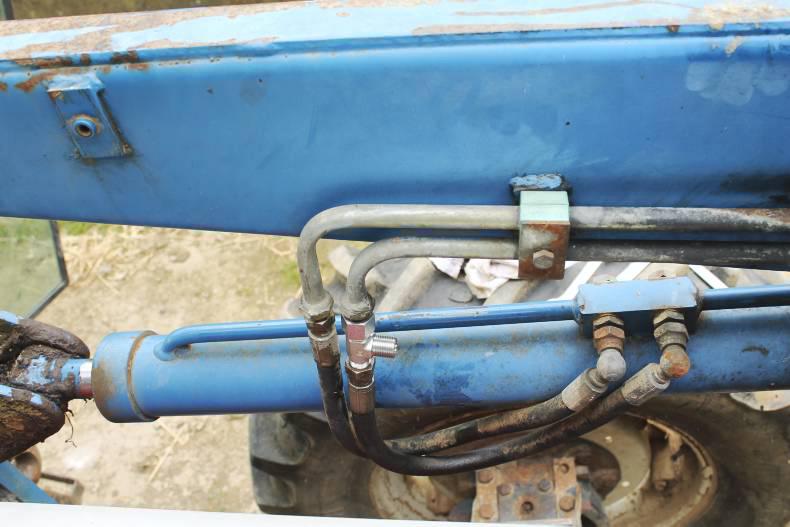
Once the loader-raise hydraulic pipe was identified, we fitted a 3/8” British standard pipe (BSP), female/male/male (F/M/M) tee.
Metric or BSP fittings are used throughout most loader makes and are easy to source.
Be very careful disconnecting hydraulic pipes. Make sure that the loader is supported and there is no pressure in the hydraulic system. Again, oil is hazardous to man and environment so use proper PPE. If in any doubt, then don’t touch the hydraulic system.
Picture seven

Mount accumulator. Insert 1/2” x 3/8” bps m/m adapter and lever action tap, plus 3/8” x 3/8” m/m bsp adapter. With the tee in place and the accumulator bolted to the saddle, measure for the hydraulic hose. In this case, the plan was to loop it up over the arm and into the accumulator tap.
Picture eight
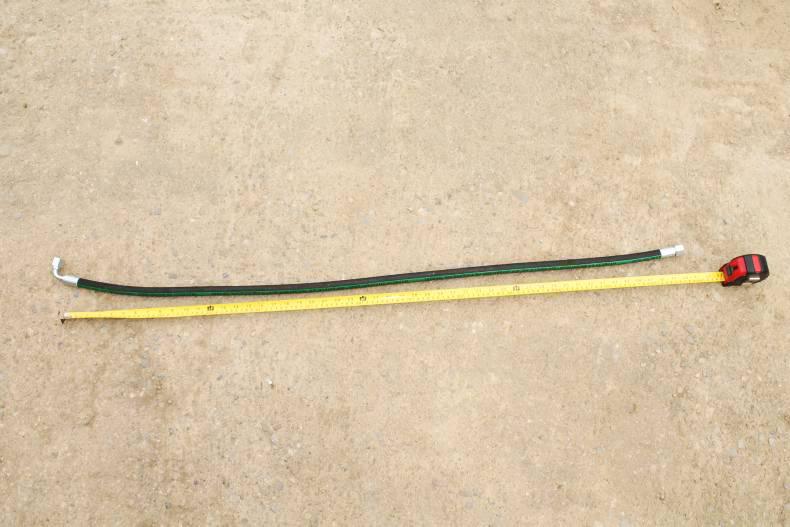
We calculated that we would need in the region of 1.2m (approximately 4ft) of hydraulic pipe. At one end, we would require a straight 3/8” female bsp end to connect to the accumulator. On the other end, a 90-degree bend would connect nicely to the tee we fitted into the loader system.
Picture nine

With the pipe connected, it looked like this. It is not complete yet as the flexible rubber pipe could easily get snagged and cause serious damage or failure of the loaders’ raising hydraulic circuit.
Picture 10
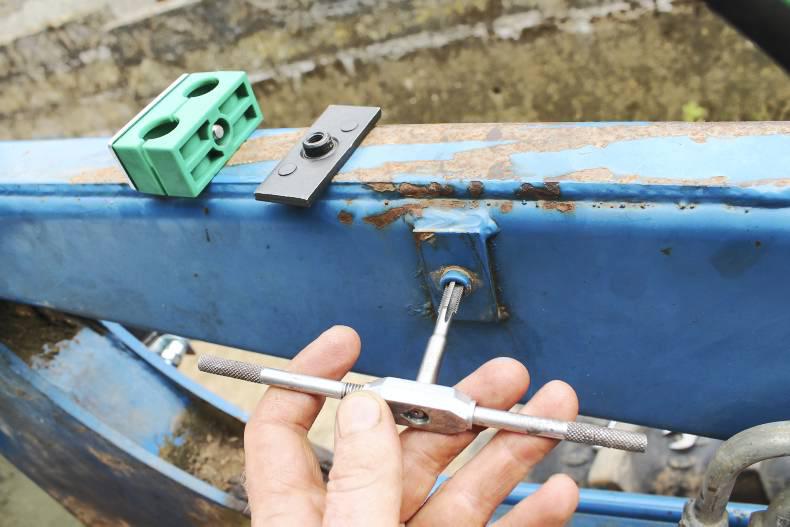
On the inside of the loader arm, there is an original Tanco clamp base plate. We used one of our 6mm taps to clean the paint and rust out.
Picture 11
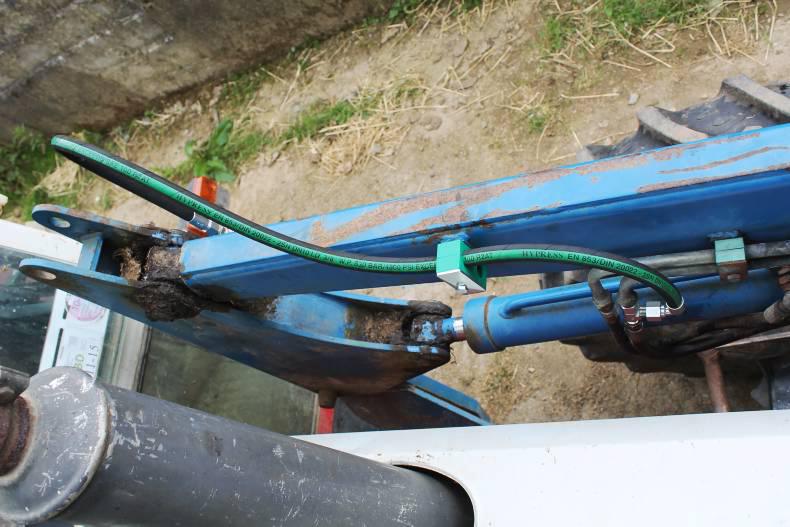
Clamping the flexible pipe in place made a much tidier job and it reduces the risk of the flexible pipe getting caught on anything.
The finished job with access to the accumulator tap is on the busy side of the tractor, where it can be switched on or off, as required.
The tap can also be seen from the tractor seat but a quick journey anywhere tells you if it is on or
not.
Kit components will differ from loader to loader, but this exercise demonstrates that a soft-drive suspension system can be fitted without costing a fortune.
The difference the soft-drive kit made was phenomenal, especially where the surface on local roads can be pretty poor. It is well worth the effort and spend to preserve the structure of both the tractor and driver. It is not quite front suspension but the soft-drive kit makes a huge difference, even at lower speeds around the yard.
The guide price of the kit we created for our Tanco T100 loader from McHugh Components (may vary from supplier to supplier):
Soft-drive kit with lever action valve €180 + vat.Soft-drive kit with electric valve: €250, plus vat.3/8”x 1/2” m/m adapter: €1.40, plus vat.Pipe clamp complete: €4.50, plus vat.1.2m of 3/8” hydraulic pipe with f-ends: €22 , plus vat.3/8” f/m/m tee: €9, plus vat.Total price of mechanical soft-drive kit €216.90, plus vat @ 13.5% = €246.18; VAT @ 23% = €266.79.Total price of electric soft-drive kit €286.90, plus vat @13.5% = €325.63; VAT @ 23% = €352.89.It is worth noting that the vat rate is 13.5% if supplied and fitted by a garage/local mechanic (who is registered for vat).
While dedicated handlers have gained in popularity, tractor front loader use is still the dominant materials handler system on farms today.
Loader capacities and features have generally evolved in line with tractor development. By and large, the principles of tractor front-loader design remain the same today as they did a handful of decades ago –ultimately, converting a conventional tractor into something akin to a self-propelled Swiss-army knife.
There are a huge number of old tractor-mounted front loaders still working effectively on farms around the country. There are even many trip loaders that would have been given a new lease of life, having been converted to hydraulic implement operation.
A number of firms even offer a quick-attach, euro-hitch implement frame conversion to bring older loaders with pin-mounted implements further up to spec.
One feature often overlooked is the addition of a little comfort. All manufacturers of tractor-mounted front loader on the market today offer some form of loader suspension. While this is generally an option, it is one almost everyone specified when buying a new loader.
While called different names by various manufacturers, all tractor-loader suspension systems are based on the same principle and act on the loader’s hydraulic system. Plumbed into the loader’s hydraulic lift rams is a gas-filled accumulator.
There are two main designs of accumulator. Both use gas, which unlike a liquid can be compressed as a method of providing a suspension system.
The gas used is generally nitrogen which is almost inert so will not react with the oil in the system if there is a leak between the gas and oil side of an accumulator. Oxygen on the other hand, when combined with oil under high pressure, can form an explosive mixture. That’s the reason why oxygen in gas cylinders used for heating and cutting should never be used to charge or test an accumulator in a hydraulic system.
By far the most common accumulator design is almost round or slightly cylindrical. This uses an elastic diaphragm to keep the oil separate from the gas.
The second design resembles a hydraulic cylinder or ram. The gas is in one end separated from the oil by a floating piston in the cylinder. This design has a higher oil capacity, but is more expensive. It is generally used on larger equipment, such as dedicated materials handlers. Its use has crept in on some tractor loaders too.
Mentioned earlier, it is likely that most new tractor front loaders will be fitted with an accumulator-based suspension system. Older loaders without suspension can benefit greatly by fitting some form of suspension or soft-drive system.
McHugh Components in Dublin is one company to offer the makings of a soft-drive system. There are many others as well that could offer such as system but, for this exercise, the Irish Farmers Journal teamed up with McHughs to fit a system to a 1995 Tanco T100 loader.
We have to mention that while McHugh components is a major parts supplier to the agricultural machinery and manufacturing industry, it does not supply directly to the consumer. Its network of dealers throughout the country is extensive, so there should be no problem sourcing part or all of a soft-drive system. Again, there are many other firms that could potentially supply a soft-drive system as well.
Fitting
We all know what it is like to travel over rough terrain or road with a tractor loader. When the tractor hits and rises over a bump in the road or yard, the loader – if fixed solidly – will rise with it and no doubt return with a bang. With an accumulator plumbed into the hydraulic circuit, the tractor rises but the weight of the loader compresses the gas within the accumulator, vastly reducing the effect of the loader returning to earth.
Fitting a soft-drive system will vary from loader to loader. This exercise with the Tanco T100 is to show that it can be done and is well worth doing.
As with all practical exercises, if in doubt don’t do it. Hydraulic oil under pressure can penetrate the skin and cause blood poisoning. Releasing a hydraulic pipe under pressure can also cause a loader or implement to drop with potentially lethal consequences.
Oil itself is an irritant, so wear suitable gloves and eye protection.
If you feel that the job is outside of your comfort zone of capabilities, your local mechanic or garage will only be too happy to fit a system for you. They should be able to provide you with a guide price to allow you to be able to budget for the job.
Tractors with high capacity hydraulics systems may require an accumulator on both side of the lift ram or leak back valve in the loader control valve block. Older tractors or tractors delivering 30 to 40 litres/min for loader operation will not require such systems.
They will rarely be able to fill the down side of the main lift/lower rams with oil in regular use. This leaves some empty space for the ram to move upwards when the suspension system is switched on and the loader is ‘‘bouncing’’.
Picture one

There are different size and capacity accumulators but pictured here is typical of what you could use on a tractor front loader. The unit on the left has an oil capacity of approximately half a litre and the unit on the right approximately three-quarters of a litre. McHugh Components offers two systems, one with a manual shut-off lever and the other with an electrically operated solenoid cut-off valve.
Picture two
Charge pressures vary and will have an effect on loader suspension performance. This unit is charged to 30-bar and is typical of what works. Some manufacturers plumb two accumulators into the circuit, charged at different pressures to offer a broader range of loader suspension.
Picture three

This is the kit we will fit to the Tanco T100, which has double-acting lift cylinders. All that is required in addition to the soft-drive kit is a length of hydraulic pipe, plus a tee to plumb into the main lift cylinder circuit.
Picture four
We fitted the accumulator on the left side of the T100 loader because there is room to bolt the accumulator to the loader saddle on this side. It is also relatively close to where we tap into the lift cylinder hydraulic circuit.
Picture five

We marked out, drilled and tapped holes to bolt the accumulator bracket directly on to the lefthand saddle. Pictured are the M8x20 bolts used, M8x1.25 (pitch) and stage one and stage two taps. The drill bit required for the hole is 6.5mm.
We drilled and tapped holes because it was the tidiest option (you can buy drill bits and taps individually at most engineering outlets). Alternatively, you could make and weld a simple bracket on to the loader.
Picture six
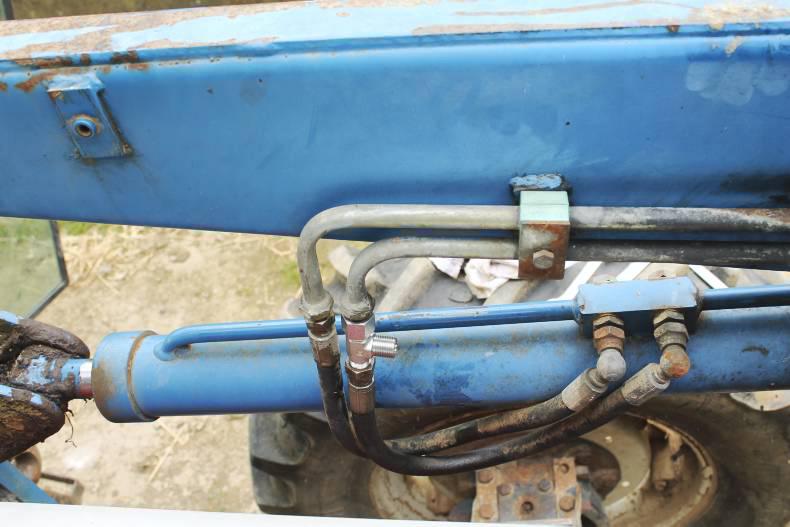
Once the loader-raise hydraulic pipe was identified, we fitted a 3/8” British standard pipe (BSP), female/male/male (F/M/M) tee.
Metric or BSP fittings are used throughout most loader makes and are easy to source.
Be very careful disconnecting hydraulic pipes. Make sure that the loader is supported and there is no pressure in the hydraulic system. Again, oil is hazardous to man and environment so use proper PPE. If in any doubt, then don’t touch the hydraulic system.
Picture seven

Mount accumulator. Insert 1/2” x 3/8” bps m/m adapter and lever action tap, plus 3/8” x 3/8” m/m bsp adapter. With the tee in place and the accumulator bolted to the saddle, measure for the hydraulic hose. In this case, the plan was to loop it up over the arm and into the accumulator tap.
Picture eight
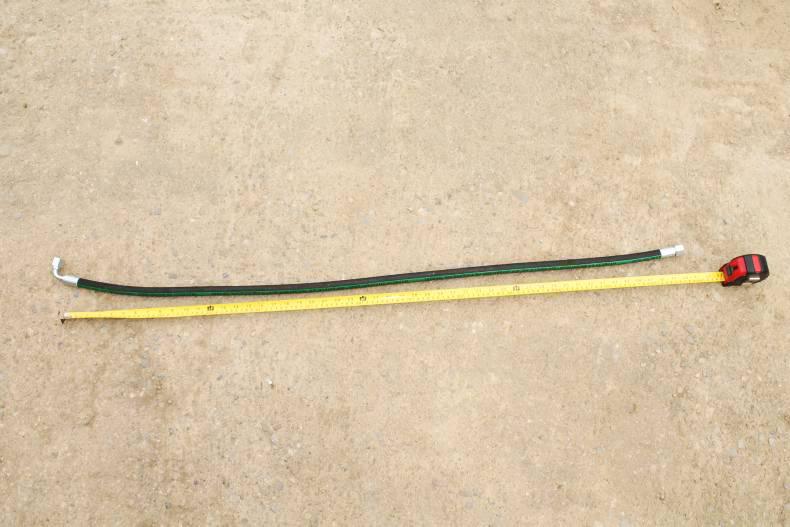
We calculated that we would need in the region of 1.2m (approximately 4ft) of hydraulic pipe. At one end, we would require a straight 3/8” female bsp end to connect to the accumulator. On the other end, a 90-degree bend would connect nicely to the tee we fitted into the loader system.
Picture nine

With the pipe connected, it looked like this. It is not complete yet as the flexible rubber pipe could easily get snagged and cause serious damage or failure of the loaders’ raising hydraulic circuit.
Picture 10
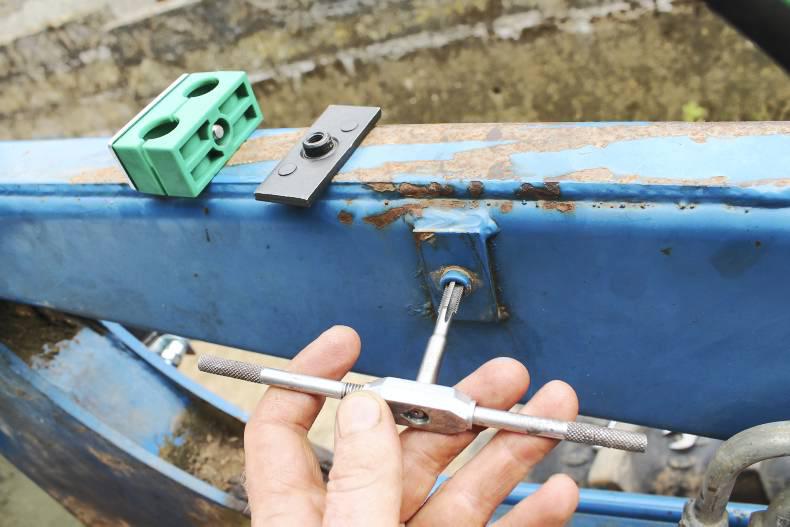
On the inside of the loader arm, there is an original Tanco clamp base plate. We used one of our 6mm taps to clean the paint and rust out.
Picture 11
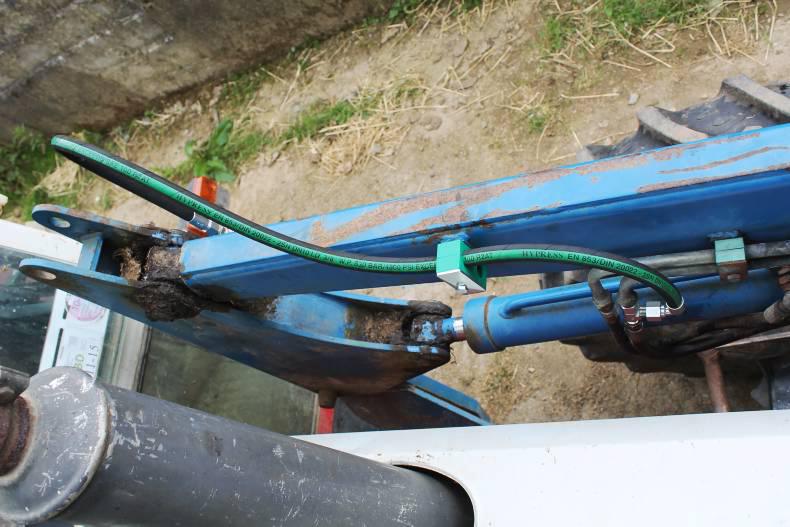
Clamping the flexible pipe in place made a much tidier job and it reduces the risk of the flexible pipe getting caught on anything.
The finished job with access to the accumulator tap is on the busy side of the tractor, where it can be switched on or off, as required.
The tap can also be seen from the tractor seat but a quick journey anywhere tells you if it is on or
not.
Kit components will differ from loader to loader, but this exercise demonstrates that a soft-drive suspension system can be fitted without costing a fortune.
The difference the soft-drive kit made was phenomenal, especially where the surface on local roads can be pretty poor. It is well worth the effort and spend to preserve the structure of both the tractor and driver. It is not quite front suspension but the soft-drive kit makes a huge difference, even at lower speeds around the yard.
The guide price of the kit we created for our Tanco T100 loader from McHugh Components (may vary from supplier to supplier):
Soft-drive kit with lever action valve €180 + vat.Soft-drive kit with electric valve: €250, plus vat.3/8”x 1/2” m/m adapter: €1.40, plus vat.Pipe clamp complete: €4.50, plus vat.1.2m of 3/8” hydraulic pipe with f-ends: €22 , plus vat.3/8” f/m/m tee: €9, plus vat.Total price of mechanical soft-drive kit €216.90, plus vat @ 13.5% = €246.18; VAT @ 23% = €266.79.Total price of electric soft-drive kit €286.90, plus vat @13.5% = €325.63; VAT @ 23% = €352.89.It is worth noting that the vat rate is 13.5% if supplied and fitted by a garage/local mechanic (who is registered for vat).
SHARING OPTIONS: