The Irish Farmers Journal recently visited a new robotic set-up on the farm of Francis and Eimear Nally and their young family Aaron and Killian, from outside Athlone, Co Westmeath. One robot has been installed on the farm but scope has been left to install another in the future if desired.
While Francis’ parents Fintan and Bridie Nally had been milking up until 1999, the decision was taken to move away from dairy. However, in 2011 Francis and Eimear re-established the dairy enterprise on the home block. Sixty cows were milked in the first year through a standard parlour and that has steadily increased in the intervening period, with 145 cows now being milked between the two blocks on the farm.
“It wouldn’t have been possible to manage two different parlours so the decision was made to go for the robot. From a lifestyle point of view, there are a lot of benefits too,” according to Francis. “There are a lot of people that don’t understand what goes into a weekend milking and the time it can take."
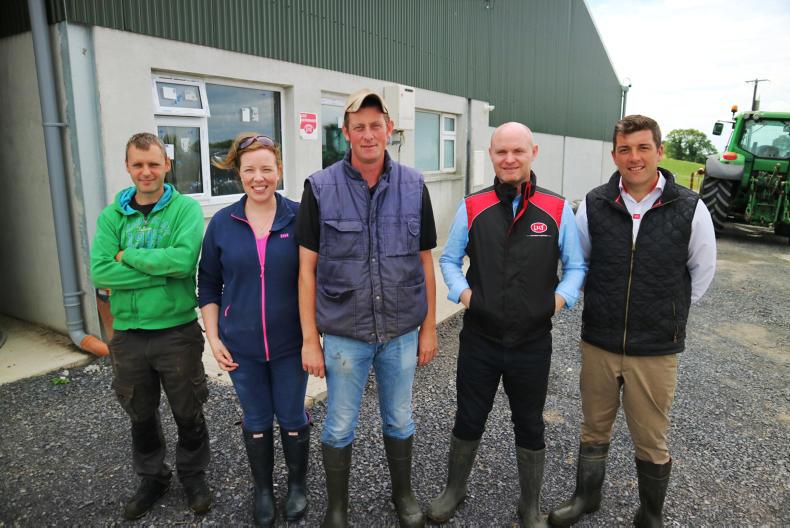
From left to right - Keith Nally, Eimear Nally, Francis Nally, SEamus McDonagh and Niall McGauran.

The shed
The Lely Astronaut was installed on a 57ac out-block which was used for carrying drystock and making silage up to this year.
Moving to an outside block with no buildings or farm infrastructure gave Francis and the team at Lely Mullingar the opportunity of locating the new shed at the centre of the farm, which is not always an option for farmers. However, it is possible to have cows walking up to 2km to the robot.
There are also options for the actual layout of the building, with the bulk tank located anywhere within 100m of the robot.
Site
The site was chosen to allow for an A-B-C grazing system to be installed. “We designed the roadways so that cows would not be meeting each other coming back from one block as this could have an effect on cow flow in and out of the shed,” according to Niall McGauran of Lely Mullingar.
The grazeway stretches out a further 10.5m from the shed as it was decided to allow plenty of room to prevent any sharp turns for cows.
“Roadways generally do not need to be too wide as it is mainly low levels of cow traffic that will be moving on them. Two-metre-wide pathways would be sufficient,” said Niall.
The gates to the A block will be open between 2am and 1pm, B block between 1pm and 7pm and C block between 7pm and 2am. In a year like this when grass is tight and any rotational grazing system is seriously challenged, the question often posed is how a robotic system can cope with these conditions, especially with grass used as a tool to encourage cows to move through the different blocks.
For Francis, feeding silage started four weeks ago with 70 bales fed to date. He made the decision to feed silage outside in fields to help keep cows moving through the robot.
“Another option for farmers is to continue letting cows out to paddocks in the A and B blocks but keep cows inside for the C block and allow them access to silage, for example,” Niall said.

Cubicles
The shed has a total of 124 cubicles and has been designed to allow for the addition of a second robotic unit in the future if required, although the land block surrounding the shed is the current limiting factor. Cows are fed on either side of the shed.
The shed itself is 36.6m long and 27.3m wide. Slatted tanks are laid out in a T shape, ensuring that when not allowed access to the cubicles, cows will be over slats for the majority, if not all, of the time that they are in the shed for milking. Tanks are 9ft deep with a total slurry storage capacity of 150,000 gallons.
Over the past winter the shed was used to hold three different groups of stock with dividers used between cubicles. Crossover points at either end of the shed mean that there is easy access to the feed barriers.
“It is a versatile shed,” according to Seamus McDonagh, project co-ordinator with Lely Mullingar. “It can be used for the 70 cows that are being milked off the robot but it can also be set up to hold other groups too.”
The main area of the shed is made up of three rows of 20 cubicles running head to head, while a further four cubicles are located in an isolation area where cows can be automatically drafted to. Cubicles measure 1.1m (43in) centre to centre with double cubicle beds measuring 4.5m from heel to heel. The feeding area for cows is 4.2m wide from the heel of the cubicle bed to the feed barrier.
“Anything less than this would be too tight and would impact on cow flow around the shed. It is often these areas that would be compromised in existing sheds but space within a shed is even more important when it comes to robotic milking,” according to Seamus.
“Cow flow is very important throughout the shed and we made sure that there were no bottlenecks or dead ends.”

Movemen
The two passageways that run down the centre of the shed are 2.9m wide. The minimum requirement is 1.8m but this could negatively impact cow flow.
Crossover points are 2.3m wide. Francis made the decision to install drinkers on the doors at the end of the passageway as opposed to at the crossover point. If they were located at the crossover point, passageways would have to be 3.5m wide. In this way, he could fit an extra six cubicles in the shed. Scrapers in the shed also go out under the door.
Drafting
Having a good drafting system was pointed out as one of the key considerations when it comes to robotic milking with this system allowing cows to be drafted to either cubicles or a large straw pen that has not yet been fitted with barriers. It is recommended that passageways that lead to the isolation area or the handling area are 950mm to 1m wide to ensure cows cannot turn back.
Ample space needs to be left in front of the robot to allow cows to easily move in and out of the system. Ideally 5m to 6m should be left and here is it 5.5m.
Outside block
Francis has installed a camera system focusing on the grazeway gates and the robot itself to identify any issues, and also for security.
“We were nervous of the system at the start,” Francis admitted. “There is a good bit of labour required to get going and that is made even more difficult when it is an outside block and you are not there as much. Things have settled down now but that only happened in the last five or six weeks.
“At the start you could be getting alerts from the robot the whole time but that can be changed so you will only get alerts for critical issues. The shed is designed to be easily kept,” he said.
“You do get more information on cows with the robot and that does filter through to deciding what to cull, for example. Every milking you can get information on yield, butterfat, protein, lactose and somatic cell count (SCC). The heat detection with the robot is also working well, we would generally AI for four to five weeks and then let bulls out.”
Cost
The cost of the first Lely Astronaut is €125,000 to €150,000, depending on the specifications of the robot. This includes other aspects including the grazeway and compressor. It also includes yard design, project management and mapping of the farm to plan grazing infrastructure.
The costs for installing a second robot start from €80,000.
A TAMS grant was used to part-fund the robot, with Francis availing of a 40% grant on the first €80,000 invested.
Eugene Costello did all the concrete work for the project, while Coyle Agri supplied the barriers. Oliver Nally plumbed the shed. The meal bin was supplied by McAree Engineering and Brendan Donnelly supplied and fitted the auger system. The mattresses were supplied by Teemore Engineering. Fencing was completed by Frank Byrne. Alan Dooley Satellite Systems installed the camera system.
The Irish Farmers Journal recently visited a new robotic set-up on the farm of Francis and Eimear Nally and their young family Aaron and Killian, from outside Athlone, Co Westmeath. One robot has been installed on the farm but scope has been left to install another in the future if desired.
While Francis’ parents Fintan and Bridie Nally had been milking up until 1999, the decision was taken to move away from dairy. However, in 2011 Francis and Eimear re-established the dairy enterprise on the home block. Sixty cows were milked in the first year through a standard parlour and that has steadily increased in the intervening period, with 145 cows now being milked between the two blocks on the farm.
“It wouldn’t have been possible to manage two different parlours so the decision was made to go for the robot. From a lifestyle point of view, there are a lot of benefits too,” according to Francis. “There are a lot of people that don’t understand what goes into a weekend milking and the time it can take."
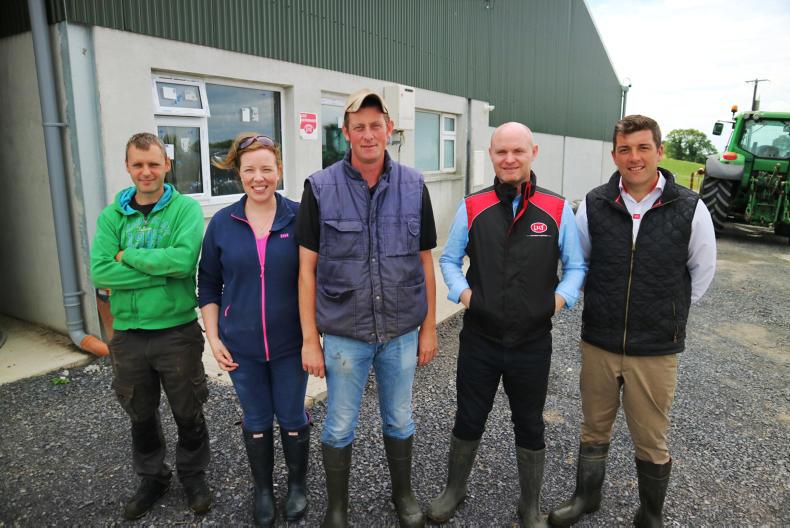
From left to right - Keith Nally, Eimear Nally, Francis Nally, SEamus McDonagh and Niall McGauran.

The shed
The Lely Astronaut was installed on a 57ac out-block which was used for carrying drystock and making silage up to this year.
Moving to an outside block with no buildings or farm infrastructure gave Francis and the team at Lely Mullingar the opportunity of locating the new shed at the centre of the farm, which is not always an option for farmers. However, it is possible to have cows walking up to 2km to the robot.
There are also options for the actual layout of the building, with the bulk tank located anywhere within 100m of the robot.
Site
The site was chosen to allow for an A-B-C grazing system to be installed. “We designed the roadways so that cows would not be meeting each other coming back from one block as this could have an effect on cow flow in and out of the shed,” according to Niall McGauran of Lely Mullingar.
The grazeway stretches out a further 10.5m from the shed as it was decided to allow plenty of room to prevent any sharp turns for cows.
“Roadways generally do not need to be too wide as it is mainly low levels of cow traffic that will be moving on them. Two-metre-wide pathways would be sufficient,” said Niall.
The gates to the A block will be open between 2am and 1pm, B block between 1pm and 7pm and C block between 7pm and 2am. In a year like this when grass is tight and any rotational grazing system is seriously challenged, the question often posed is how a robotic system can cope with these conditions, especially with grass used as a tool to encourage cows to move through the different blocks.
For Francis, feeding silage started four weeks ago with 70 bales fed to date. He made the decision to feed silage outside in fields to help keep cows moving through the robot.
“Another option for farmers is to continue letting cows out to paddocks in the A and B blocks but keep cows inside for the C block and allow them access to silage, for example,” Niall said.

Cubicles
The shed has a total of 124 cubicles and has been designed to allow for the addition of a second robotic unit in the future if required, although the land block surrounding the shed is the current limiting factor. Cows are fed on either side of the shed.
The shed itself is 36.6m long and 27.3m wide. Slatted tanks are laid out in a T shape, ensuring that when not allowed access to the cubicles, cows will be over slats for the majority, if not all, of the time that they are in the shed for milking. Tanks are 9ft deep with a total slurry storage capacity of 150,000 gallons.
Over the past winter the shed was used to hold three different groups of stock with dividers used between cubicles. Crossover points at either end of the shed mean that there is easy access to the feed barriers.
“It is a versatile shed,” according to Seamus McDonagh, project co-ordinator with Lely Mullingar. “It can be used for the 70 cows that are being milked off the robot but it can also be set up to hold other groups too.”
The main area of the shed is made up of three rows of 20 cubicles running head to head, while a further four cubicles are located in an isolation area where cows can be automatically drafted to. Cubicles measure 1.1m (43in) centre to centre with double cubicle beds measuring 4.5m from heel to heel. The feeding area for cows is 4.2m wide from the heel of the cubicle bed to the feed barrier.
“Anything less than this would be too tight and would impact on cow flow around the shed. It is often these areas that would be compromised in existing sheds but space within a shed is even more important when it comes to robotic milking,” according to Seamus.
“Cow flow is very important throughout the shed and we made sure that there were no bottlenecks or dead ends.”

Movemen
The two passageways that run down the centre of the shed are 2.9m wide. The minimum requirement is 1.8m but this could negatively impact cow flow.
Crossover points are 2.3m wide. Francis made the decision to install drinkers on the doors at the end of the passageway as opposed to at the crossover point. If they were located at the crossover point, passageways would have to be 3.5m wide. In this way, he could fit an extra six cubicles in the shed. Scrapers in the shed also go out under the door.
Drafting
Having a good drafting system was pointed out as one of the key considerations when it comes to robotic milking with this system allowing cows to be drafted to either cubicles or a large straw pen that has not yet been fitted with barriers. It is recommended that passageways that lead to the isolation area or the handling area are 950mm to 1m wide to ensure cows cannot turn back.
Ample space needs to be left in front of the robot to allow cows to easily move in and out of the system. Ideally 5m to 6m should be left and here is it 5.5m.
Outside block
Francis has installed a camera system focusing on the grazeway gates and the robot itself to identify any issues, and also for security.
“We were nervous of the system at the start,” Francis admitted. “There is a good bit of labour required to get going and that is made even more difficult when it is an outside block and you are not there as much. Things have settled down now but that only happened in the last five or six weeks.
“At the start you could be getting alerts from the robot the whole time but that can be changed so you will only get alerts for critical issues. The shed is designed to be easily kept,” he said.
“You do get more information on cows with the robot and that does filter through to deciding what to cull, for example. Every milking you can get information on yield, butterfat, protein, lactose and somatic cell count (SCC). The heat detection with the robot is also working well, we would generally AI for four to five weeks and then let bulls out.”
Cost
The cost of the first Lely Astronaut is €125,000 to €150,000, depending on the specifications of the robot. This includes other aspects including the grazeway and compressor. It also includes yard design, project management and mapping of the farm to plan grazing infrastructure.
The costs for installing a second robot start from €80,000.
A TAMS grant was used to part-fund the robot, with Francis availing of a 40% grant on the first €80,000 invested.
Eugene Costello did all the concrete work for the project, while Coyle Agri supplied the barriers. Oliver Nally plumbed the shed. The meal bin was supplied by McAree Engineering and Brendan Donnelly supplied and fitted the auger system. The mattresses were supplied by Teemore Engineering. Fencing was completed by Frank Byrne. Alan Dooley Satellite Systems installed the camera system.
SHARING OPTIONS: