Based near Enniskillen, Co Fermanagh, R&W Contractors is a family-run business specialising in wood-chipping, timber harvesting, brash recovery and site clearance operations.
During the summer months, the services offering expanded to include a small amount of pit silage.
The family business was first established by Rodney Noble, who started out mainly as an agricultural contractor, before gradually going down the route of digger hire and site-clearance work. In 2013, Rodney found himself in a job clearing a willow plantation, which had gone beyond the stage of harvesting with a self-propelled harvester. Once the site had been felled with the digger and saw, the customer needed the willow to be chipped. Having spotted an opening for a high-capacity PTO wood chipper, Rodney looked into the idea. After some research, a deal was done for a new Mus-Max WT 8 machine, which he operated with a Case IH Puma 165.
Since then, the business has grown considerably and is driven forward with the help of sons, William and Thomas, who are now heavily involved in its day-to-day running.
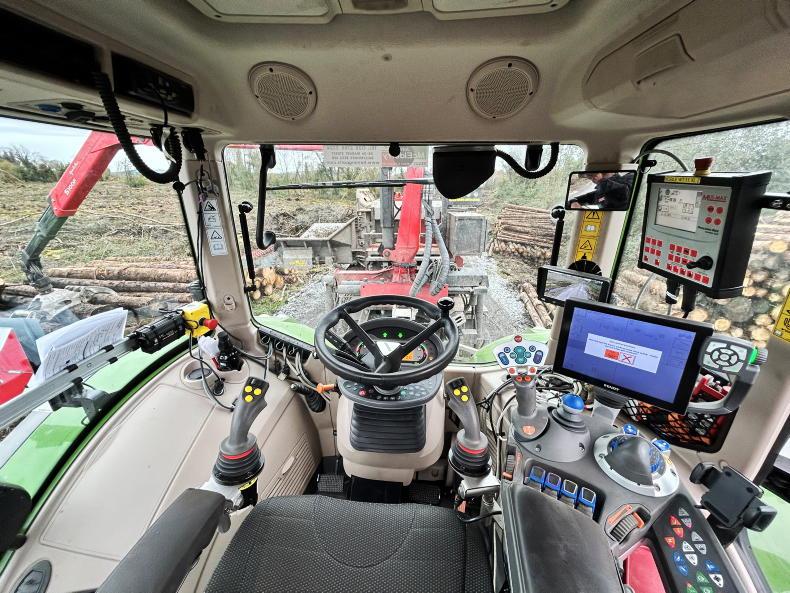
The reverse drive feature and the large cab leaves for a comfortable work station.
Along with the three Nobles, a further seven staff are employed full-time. Alongside running two Mus-Max trailed chippers, machinery includes one timber harvester, three timber forwarders and five diggers, which spend the majority of time at site-clearance work.
Wood chipping
Over the years, the business has grown steadily, mainly as result of the niche services it provides and helped by the work generated on the back of Northern Ireland’s Renewable Heat Incentive (RHI) scheme, which has seen a considerable increase in the number of biomass burners requiring chipped timber for fuel. Since the closure of the scheme, the business has continued to grow, with the Nobles now chipping all across the island of Ireland. Two years ago, a second chipper was purchased in order to keep up with workload. Now, in excess of 80,000t of timber and brash are chipped annually.
In 2018, Rodney’s original Mus-Max WT 8 was upgraded to a WT 9 model. Having a power requirement in the region 300hp, he bought a Case IH Magnum 340, which was later replaced by a Fendt 936 Vario. For 2022, the decision was made to purchase another chipper to keep up with the growing workload.
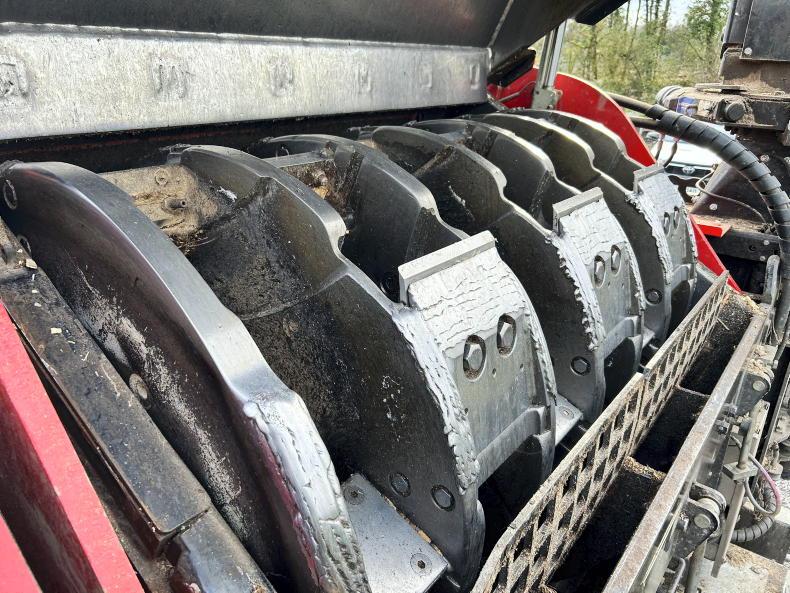
Although the drum can accomodate up 14 knives, the Nobles opt to run 12.
A deal was done for Mus-Max’s largest machine at the time, a WT 11XL Z. However, Covid-19, delayed its delivery time by over nine months. In the meantime, a Jenz 583 machine was bought to keep on top of the workload until the WT 11XL Z arrived into the country.
“The Mus-Max machines had worked well up until this and we knew their workings and maintenance inside out. The Jenz was a grand machine too. We worked it for the year until the WT 11 XL Z arrived last December. It now runs alongside a WT 11 Z, which replaced the older WT 9 earlier this summer,” William explained.
Both are among the highest-output trailed machines currently available on the market. The WT 11XL Z now sits as the second-largest model offered by the Austrian manufacturer and is capable of chipping in the region of 75t/hr, while the slightly smaller WT 11 Z is capable of 50t/hr, William said, based on his experience.
As you’d expect, it takes a considerable amount of engineering to turn 75t of trees into 75t of wood chip in one hour, almost 22t of steel to be exact. This is the total combined weight of the WT 11XL Z. The unit can be broken down into three components, the chassis, the chipper and the crane. We caught up with William to see the WT 11XL Z in action.
Crane and intake
The WT 11XL Z chassis is equipped with a 10m Palfinger Epsilon S100F crane, which weighs 3t alone. This two-stage crane and its jacks are run off the tractor’s load sensing hydraulics and is controlled from the tractor cab via two joysticks.

The spout has a 1m telescopic extension.
It has a 135cm x 80cm feed opening, which is fed via a 3m infeed conveyor. This translates to a maximum possible tree diameter of 80cm (softwood). From here, the top and bottom rollers control the infeed of timber into the chopping drum. The chopping unit follows a similar operating principle to a forage harvester in that it features a perfectly balanced drum and shearbar. The heavy-duty drum can be equipped with six, 12 or 14 blades, each achieving one cut per revolution. However, the Nobles run 12 blades, with 40mm, 50mm and 60mm screens generally, depending on the particular job. These screens are what determine the chip sizes. William explained that larger industrial size biomass boilers can accommodate chips up to 60mm in size, whereas smaller domestic boilers tend to take 30mm chips.
Blower and features
Underneath the screens, hydraulic augers transport the chips towards the hydraulic blower drum, which can be set anywhere between 500rpm and 1,100rpm, depending on operator preference.
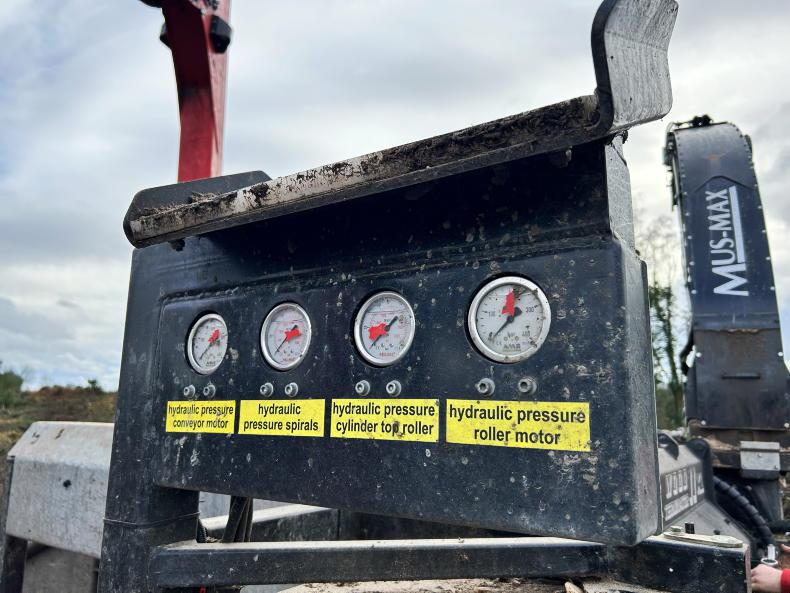
All gauges are easily viewed from the tractor cab.
William explained that the hydraulically adjustable drum speed was an optional extra they went for in order to increase speed to blow brash, which can often be wet. Other features include an auto greaser.
From the control terminal in the cab, the operator can control the speed of the drum and infeed conveyor. Drum speed is controlled by adjusting the tractor’s PTO speed. The chipper has an automatic feed control feature whereby the infeed is adjusted in accordance with the tractor’s engine load, the greater the load on the engine the slower the infeed and vice versa.
William explained that the system works very well, which he feels is partly down to the impressive low-down torque of the Fendt 1050’s MAN 12.4l engine. According to Fendt, the 1050 achieves its maximum torque of 2,400Nm at just 1,100rpm.
Wear and tear
Given the nature of the job, there is naturally a considerable amount of wear and tear on the chippers. In total, William said that they have over 20 sets of blades, including spares. Blades tend to be swapped out for a freshly sharpened set every evening. Other maintenance includes the replacement of blower wear plates and spout liners every 300 hours and hard-facing in areas around the drum to prolong working life.
Fendt tractors
In 2020, the Nobles decided it was time to upgrade the Magnum 340. Given the nature of the work in that the operator ideally needs to be facing the chipper, a reverse drive tractor was the obvious shout. This straight away limited the options, as Fendt and Valtra were the only two brands offering reverse drive from factory.

Speed of the hydraulically driven blower can be set anywhere between 500rpm and 1,100rpm depending on the material being chipped.
“Fendt was really the only option as it offered both the power we required and the reverse drive package. Our first Fendt was a 936 Vario. It worked away on the WT 9 until this year, clocking up over 6,000 hours with little to no issues,” William said.
Today, the fleet comprises five Fendt Vario tractors; a 1050, 942, 724 and two 718s. In January 2022, the Nobles bought the first 1050 Vario tractor to be sold in Ireland, Fendt’s flagship tractor model. Churning out a maximum 517hp, the 1050 Vario was bought to run the Mus-Max WT 11XL Z chipper, which didn’t arrive until December 2022.
“Since delivery, I don’t think the chipper has been taken off the 1050. It has in the region of 2,500 hours clocked up now. It’s well matched to the big chipper, but at the same time we wouldn’t like to run it with any less power, and the chipper can test it at times. In good timber, it can chip 75t/hr or fill an artic trailer in around 20 minutes. At this sort of work it will have no problem burning 70l/hr.”
To put this into context, the 740l tank would last just under 10.5 hours of continuous chipping. The 942 Vario, on the other hand, burns marginally less at 65l/hr working the WT 11 Z, which can chip in the region of 50t/hr, according to William.
Given the radius of the Noble’s cover, one might think a self-propelled chipper or a chipper built onto a truck body might be a better option, but William believes that the tractor and trailed chipper suits their business for a number of reasons.
“If we ever find ourselves at a job where ground conditions are poor, well then we have the traction benefits of a tractor. Or for some reason there was an issue with a tractor, then we can just hook the chipper onto another tractor. On top of that, trailed machines seem less complicated and the option is always there to upgrade it separately to the tractor. So, it really boils down to the versatility of a trailed chipper,” William pointed out.
Based near Enniskillen, Co Fermanagh, R&W Contractors is a family-run business specialising in wood-chipping, timber harvesting, brash recovery and site clearance operations.
During the summer months, the services offering expanded to include a small amount of pit silage.
The family business was first established by Rodney Noble, who started out mainly as an agricultural contractor, before gradually going down the route of digger hire and site-clearance work. In 2013, Rodney found himself in a job clearing a willow plantation, which had gone beyond the stage of harvesting with a self-propelled harvester. Once the site had been felled with the digger and saw, the customer needed the willow to be chipped. Having spotted an opening for a high-capacity PTO wood chipper, Rodney looked into the idea. After some research, a deal was done for a new Mus-Max WT 8 machine, which he operated with a Case IH Puma 165.
Since then, the business has grown considerably and is driven forward with the help of sons, William and Thomas, who are now heavily involved in its day-to-day running.
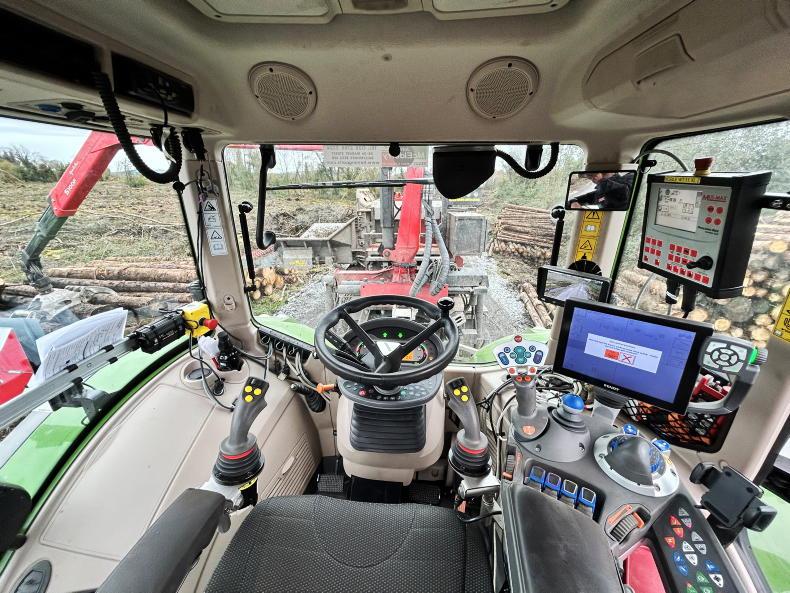
The reverse drive feature and the large cab leaves for a comfortable work station.
Along with the three Nobles, a further seven staff are employed full-time. Alongside running two Mus-Max trailed chippers, machinery includes one timber harvester, three timber forwarders and five diggers, which spend the majority of time at site-clearance work.
Wood chipping
Over the years, the business has grown steadily, mainly as result of the niche services it provides and helped by the work generated on the back of Northern Ireland’s Renewable Heat Incentive (RHI) scheme, which has seen a considerable increase in the number of biomass burners requiring chipped timber for fuel. Since the closure of the scheme, the business has continued to grow, with the Nobles now chipping all across the island of Ireland. Two years ago, a second chipper was purchased in order to keep up with workload. Now, in excess of 80,000t of timber and brash are chipped annually.
In 2018, Rodney’s original Mus-Max WT 8 was upgraded to a WT 9 model. Having a power requirement in the region 300hp, he bought a Case IH Magnum 340, which was later replaced by a Fendt 936 Vario. For 2022, the decision was made to purchase another chipper to keep up with the growing workload.
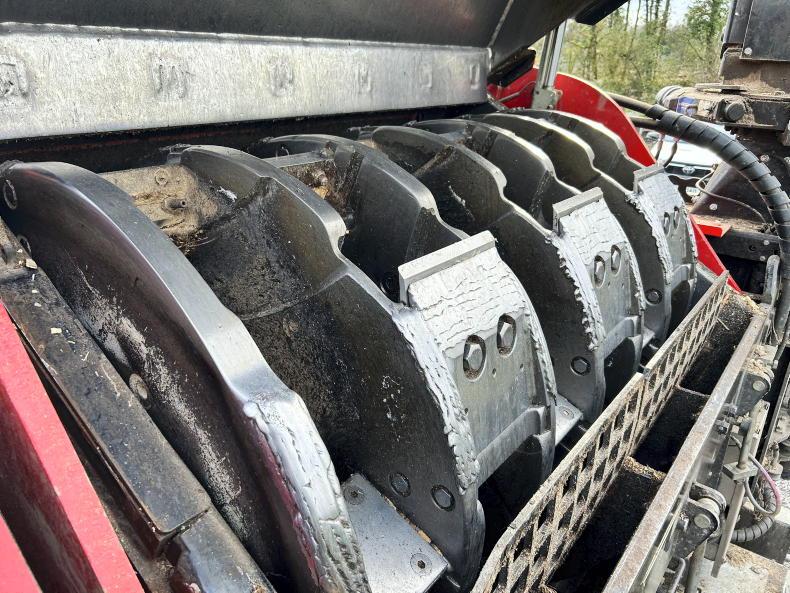
Although the drum can accomodate up 14 knives, the Nobles opt to run 12.
A deal was done for Mus-Max’s largest machine at the time, a WT 11XL Z. However, Covid-19, delayed its delivery time by over nine months. In the meantime, a Jenz 583 machine was bought to keep on top of the workload until the WT 11XL Z arrived into the country.
“The Mus-Max machines had worked well up until this and we knew their workings and maintenance inside out. The Jenz was a grand machine too. We worked it for the year until the WT 11 XL Z arrived last December. It now runs alongside a WT 11 Z, which replaced the older WT 9 earlier this summer,” William explained.
Both are among the highest-output trailed machines currently available on the market. The WT 11XL Z now sits as the second-largest model offered by the Austrian manufacturer and is capable of chipping in the region of 75t/hr, while the slightly smaller WT 11 Z is capable of 50t/hr, William said, based on his experience.
As you’d expect, it takes a considerable amount of engineering to turn 75t of trees into 75t of wood chip in one hour, almost 22t of steel to be exact. This is the total combined weight of the WT 11XL Z. The unit can be broken down into three components, the chassis, the chipper and the crane. We caught up with William to see the WT 11XL Z in action.
Crane and intake
The WT 11XL Z chassis is equipped with a 10m Palfinger Epsilon S100F crane, which weighs 3t alone. This two-stage crane and its jacks are run off the tractor’s load sensing hydraulics and is controlled from the tractor cab via two joysticks.

The spout has a 1m telescopic extension.
It has a 135cm x 80cm feed opening, which is fed via a 3m infeed conveyor. This translates to a maximum possible tree diameter of 80cm (softwood). From here, the top and bottom rollers control the infeed of timber into the chopping drum. The chopping unit follows a similar operating principle to a forage harvester in that it features a perfectly balanced drum and shearbar. The heavy-duty drum can be equipped with six, 12 or 14 blades, each achieving one cut per revolution. However, the Nobles run 12 blades, with 40mm, 50mm and 60mm screens generally, depending on the particular job. These screens are what determine the chip sizes. William explained that larger industrial size biomass boilers can accommodate chips up to 60mm in size, whereas smaller domestic boilers tend to take 30mm chips.
Blower and features
Underneath the screens, hydraulic augers transport the chips towards the hydraulic blower drum, which can be set anywhere between 500rpm and 1,100rpm, depending on operator preference.
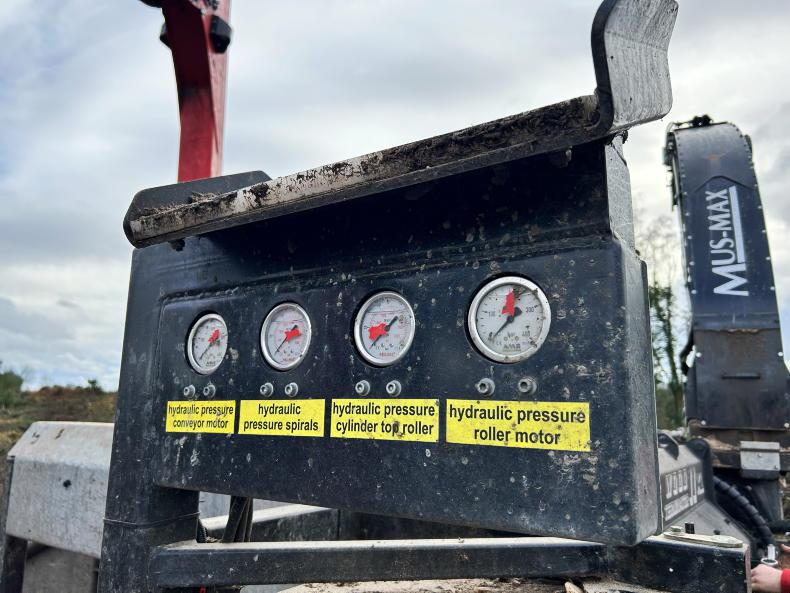
All gauges are easily viewed from the tractor cab.
William explained that the hydraulically adjustable drum speed was an optional extra they went for in order to increase speed to blow brash, which can often be wet. Other features include an auto greaser.
From the control terminal in the cab, the operator can control the speed of the drum and infeed conveyor. Drum speed is controlled by adjusting the tractor’s PTO speed. The chipper has an automatic feed control feature whereby the infeed is adjusted in accordance with the tractor’s engine load, the greater the load on the engine the slower the infeed and vice versa.
William explained that the system works very well, which he feels is partly down to the impressive low-down torque of the Fendt 1050’s MAN 12.4l engine. According to Fendt, the 1050 achieves its maximum torque of 2,400Nm at just 1,100rpm.
Wear and tear
Given the nature of the job, there is naturally a considerable amount of wear and tear on the chippers. In total, William said that they have over 20 sets of blades, including spares. Blades tend to be swapped out for a freshly sharpened set every evening. Other maintenance includes the replacement of blower wear plates and spout liners every 300 hours and hard-facing in areas around the drum to prolong working life.
Fendt tractors
In 2020, the Nobles decided it was time to upgrade the Magnum 340. Given the nature of the work in that the operator ideally needs to be facing the chipper, a reverse drive tractor was the obvious shout. This straight away limited the options, as Fendt and Valtra were the only two brands offering reverse drive from factory.

Speed of the hydraulically driven blower can be set anywhere between 500rpm and 1,100rpm depending on the material being chipped.
“Fendt was really the only option as it offered both the power we required and the reverse drive package. Our first Fendt was a 936 Vario. It worked away on the WT 9 until this year, clocking up over 6,000 hours with little to no issues,” William said.
Today, the fleet comprises five Fendt Vario tractors; a 1050, 942, 724 and two 718s. In January 2022, the Nobles bought the first 1050 Vario tractor to be sold in Ireland, Fendt’s flagship tractor model. Churning out a maximum 517hp, the 1050 Vario was bought to run the Mus-Max WT 11XL Z chipper, which didn’t arrive until December 2022.
“Since delivery, I don’t think the chipper has been taken off the 1050. It has in the region of 2,500 hours clocked up now. It’s well matched to the big chipper, but at the same time we wouldn’t like to run it with any less power, and the chipper can test it at times. In good timber, it can chip 75t/hr or fill an artic trailer in around 20 minutes. At this sort of work it will have no problem burning 70l/hr.”
To put this into context, the 740l tank would last just under 10.5 hours of continuous chipping. The 942 Vario, on the other hand, burns marginally less at 65l/hr working the WT 11 Z, which can chip in the region of 50t/hr, according to William.
Given the radius of the Noble’s cover, one might think a self-propelled chipper or a chipper built onto a truck body might be a better option, but William believes that the tractor and trailed chipper suits their business for a number of reasons.
“If we ever find ourselves at a job where ground conditions are poor, well then we have the traction benefits of a tractor. Or for some reason there was an issue with a tractor, then we can just hook the chipper onto another tractor. On top of that, trailed machines seem less complicated and the option is always there to upgrade it separately to the tractor. So, it really boils down to the versatility of a trailed chipper,” William pointed out.
SHARING OPTIONS: