Renewable energy incentives are brought in by governments to encourage people to invest in technologies to hit EU targets. What they really do is encourage people to invest to get a return on their investment.
In the UK, many incentives initially set out to give investors a return of 8% to 10% over time to make it worthwhile. In many cases, farmers are ideally positioned to increase the returns, as they have large needs when it comes to heat and electricity requirements.
However, it is clear in many countries that incentives have the additional benefit of directly supporting farmers’ income. I first saw it in Germany, where AD plants using slurry got a higher incentive, making it very attractive.
The UK initially went down the same way, although over time the level of incentives have been reduced.
The introduction of renewable heat incentives (RHI) in Northern Ireland set out to meet the government’s target of 10% of heat produced from renewables by 2020. It is available for biomethane, biomass boilers, solar thermal and ground-source heat pumps.
RHI has certainly helped the pig and poultry sector in Northern Ireland. Big heat users, many have moved to quickly install biomass boilers to cut expensive heating bills. In some cases, they can get a payment for heating houses.
In a business that has been plagued by volatility and tight margins, the ability to turn what was a significant cost into a positive has doubled profitability, but also given them a considerable competitive advantage.
How it is paid
Heat meters are installed for each boiler and payments are determined by the actual heat output made quarterly. RHI is set at a fixed rate that only changes in line with inflation.
The payment for biomass boilers depends on the size, with a big drop in payment when boiler size goes above 100kW. This has seen many farmers put in a number of small boilers to maximise RHI payments, rather than a single, larger unit.
The RHI is currently under review for new entrants to the scheme, with several changes likely.
One change proposed is to reduce the payment for controlled heat and power technologies by 0.5 ROCs (2c/kWh) and give an additional payment for the heat energy produced. Another proposed change is to have the same payment for all sizes of biomass boilers at 3.5 pence per kWh for new systems.
Domestic heat use
There is a separate heat generation scheme operating in Northern Ireland, for domestic heat use. It provides an upfront payment to assist with the capital cost and a tariff payment for a period of seven years. They are for:
Solar thermal – £320 and 13.7p/kWh.Air source heat pumps – £1,700 and 3.6p/kWh.Biomass boilers – £2,500 and 5.7p/kWh.Ground source heat pump – £3,500 and 8.3p/kWh.Biomass boilers, fuelled usually by logs or pellets, are by far the most popular, accounting for almost half of total installations.
On the domestic scheme, the amount of heat used is calculated based on an energy performance certificate for the building, unless a dual system has been retained, in which case they would need a meter to measure the amount produced by biomass.
State-of-the-art R&D lab opening at CREST
The focus on renewable energy in Northern Ireland has also brought construction jobs and back-up services.
A new state-of-the-art bioenergy research and development testing facility is opening at the Centre for Renewable Energy and Sustainable Technologies (CREST) in Enniskillen on Wednesday 9 September.
The advanced R&D facility, which is part-financed through the Interreg IVa programme, with support from the Special EU Programmes Body, is thought to be the most extensive research facility of its kind in Northern Ireland.
It comprises of a testing laboratory and a biomass processing area, including a briquette press, pellet mill and oilseed press, along with a range of testing equipment.
“The new laboratory will enable us to undertake a range of practical industry research projects relating to bioenergy on behalf of businesses and farmers in the region,” CREST centre manager Tim Stokes said.
The equipment can be used to process and analyse various biomass residues to assess their suitability for producing biomass fuel.
It can also be used to support local anaerobic digestion plants through testing the stability of biological processes that are producing the biogas – thereby facilitating efficient plant operation and energy production.
A three-day series of events has been organised by CREST at South West College and the Agri-Food and Biosciences Institute (AFBI) will run as follows:
8 September – Biomass Fuel Quality Workshop at AFBI, Hillsborough.9 September – CREST R&D lab opening and biomass processing and testing workshop.10 September – Anaerobic digestion and biogas optimisation seminar at CREST.For further information, contact Shane McBrien on 028-6634 2301 or email: shane.mcbrien@swc.ac.uk
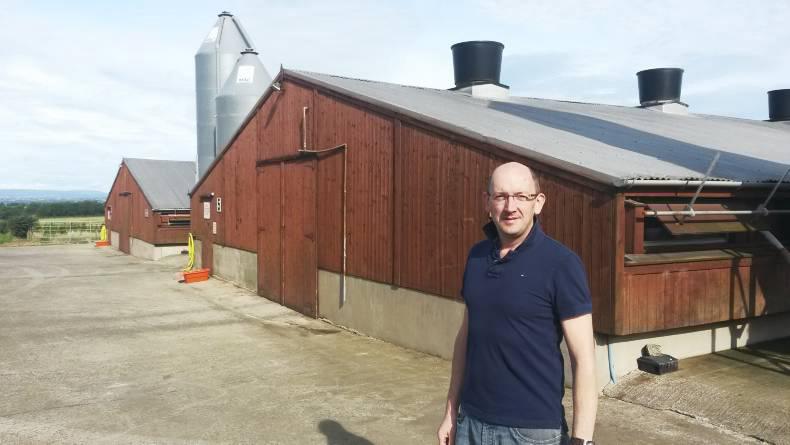
Farmer getting the heat benefits
Thomas Forgrave rears broiler chickens for Moy Park up to 42 days old in six poultry houses on his farm near Ballymoney, Co Antrim. He installed six biomass boilers 18 months ago to heat each of his sheds using fan heaters.
Thomas decided to install six individual heaters, as the tariff paid for biomass boilers from 20 to 99kW is 6.4 pence per kWh, whereas the next bracket from 100 to 999kW boilers is only 1.5p/kWh. This made it much more economical to have a boiler for each shed, as opposed to one large boiler for the whole farm.
Three 20t meal bins store wood pellets that are fed in automatically to a burning chamber which produces heat to maintain water in a 3,000-litre buffer tank at 80°C. This water is then pumped to the shed where a radiator in the fan heaters heat the house.
Each house cost around £50,000 to £60,000 to convert and the coniferous timber wood pellets cost from £165 to £185/t. The amount used differs greatly depending on the time of year and the weather.
Servicing and electricity costs on the farm have increased since the new system was installed.
“The electricity bill is easily up by 50% from before, but this is understandable with the power needed for the boiler, water pumps, computer system and fan heaters,” Thomas said.
Houses are maintained at 32 to 34°C at day one and then gradually brought down to 22 to 24°C. The boilers are switched on a few days before the birds arrive and are switched off for the last 10 days as the birds are eventually capable of making their own heat.
The houses on the farm were originally heated with gas heaters. Thomas has observed improvements to the litter quality and less hock burn and lameness in the broilers since converting to biomass. This is due to no water vapour being produced from the heaters.
“The biggest benefit is bird welfare because of this. It is also more pleasant for the farmer, with no smell from ammonia. Feed conversion ratio has improved since I changed the heaters,” Thomas said.
There is no cap on RHI for the amount of entrants and the energy paid for, so there has been wide uptake of the scheme with anyone with a high-heat requirement. RHI is paid for 20 years for each technology.
The RHI is currently under review for new entrants to the scheme. Changes such as increasing the upper limit for the size of boiler for higher payments and possibly imposing a cap on the amount paid for a technology per time period have been rumoured.
Changes are planned to come into force from around October and are likely to be announced in the coming weeks.
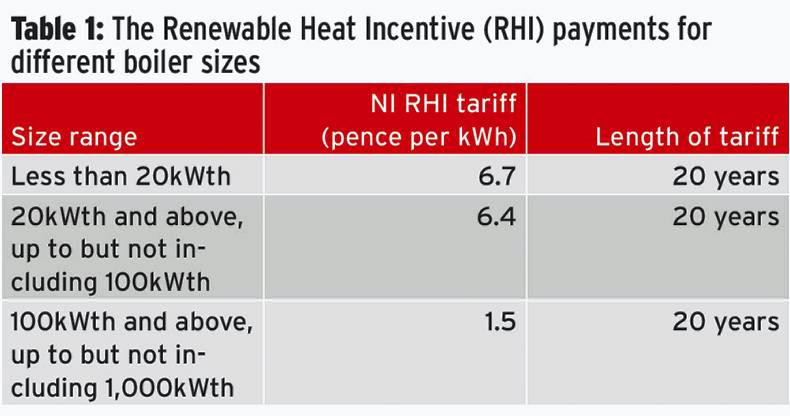
Renewable energy incentives are brought in by governments to encourage people to invest in technologies to hit EU targets. What they really do is encourage people to invest to get a return on their investment.
In the UK, many incentives initially set out to give investors a return of 8% to 10% over time to make it worthwhile. In many cases, farmers are ideally positioned to increase the returns, as they have large needs when it comes to heat and electricity requirements.
However, it is clear in many countries that incentives have the additional benefit of directly supporting farmers’ income. I first saw it in Germany, where AD plants using slurry got a higher incentive, making it very attractive.
The UK initially went down the same way, although over time the level of incentives have been reduced.
The introduction of renewable heat incentives (RHI) in Northern Ireland set out to meet the government’s target of 10% of heat produced from renewables by 2020. It is available for biomethane, biomass boilers, solar thermal and ground-source heat pumps.
RHI has certainly helped the pig and poultry sector in Northern Ireland. Big heat users, many have moved to quickly install biomass boilers to cut expensive heating bills. In some cases, they can get a payment for heating houses.
In a business that has been plagued by volatility and tight margins, the ability to turn what was a significant cost into a positive has doubled profitability, but also given them a considerable competitive advantage.
How it is paid
Heat meters are installed for each boiler and payments are determined by the actual heat output made quarterly. RHI is set at a fixed rate that only changes in line with inflation.
The payment for biomass boilers depends on the size, with a big drop in payment when boiler size goes above 100kW. This has seen many farmers put in a number of small boilers to maximise RHI payments, rather than a single, larger unit.
The RHI is currently under review for new entrants to the scheme, with several changes likely.
One change proposed is to reduce the payment for controlled heat and power technologies by 0.5 ROCs (2c/kWh) and give an additional payment for the heat energy produced. Another proposed change is to have the same payment for all sizes of biomass boilers at 3.5 pence per kWh for new systems.
Domestic heat use
There is a separate heat generation scheme operating in Northern Ireland, for domestic heat use. It provides an upfront payment to assist with the capital cost and a tariff payment for a period of seven years. They are for:
Solar thermal – £320 and 13.7p/kWh.Air source heat pumps – £1,700 and 3.6p/kWh.Biomass boilers – £2,500 and 5.7p/kWh.Ground source heat pump – £3,500 and 8.3p/kWh.Biomass boilers, fuelled usually by logs or pellets, are by far the most popular, accounting for almost half of total installations.
On the domestic scheme, the amount of heat used is calculated based on an energy performance certificate for the building, unless a dual system has been retained, in which case they would need a meter to measure the amount produced by biomass.
State-of-the-art R&D lab opening at CREST
The focus on renewable energy in Northern Ireland has also brought construction jobs and back-up services.
A new state-of-the-art bioenergy research and development testing facility is opening at the Centre for Renewable Energy and Sustainable Technologies (CREST) in Enniskillen on Wednesday 9 September.
The advanced R&D facility, which is part-financed through the Interreg IVa programme, with support from the Special EU Programmes Body, is thought to be the most extensive research facility of its kind in Northern Ireland.
It comprises of a testing laboratory and a biomass processing area, including a briquette press, pellet mill and oilseed press, along with a range of testing equipment.
“The new laboratory will enable us to undertake a range of practical industry research projects relating to bioenergy on behalf of businesses and farmers in the region,” CREST centre manager Tim Stokes said.
The equipment can be used to process and analyse various biomass residues to assess their suitability for producing biomass fuel.
It can also be used to support local anaerobic digestion plants through testing the stability of biological processes that are producing the biogas – thereby facilitating efficient plant operation and energy production.
A three-day series of events has been organised by CREST at South West College and the Agri-Food and Biosciences Institute (AFBI) will run as follows:
8 September – Biomass Fuel Quality Workshop at AFBI, Hillsborough.9 September – CREST R&D lab opening and biomass processing and testing workshop.10 September – Anaerobic digestion and biogas optimisation seminar at CREST.For further information, contact Shane McBrien on 028-6634 2301 or email: shane.mcbrien@swc.ac.uk
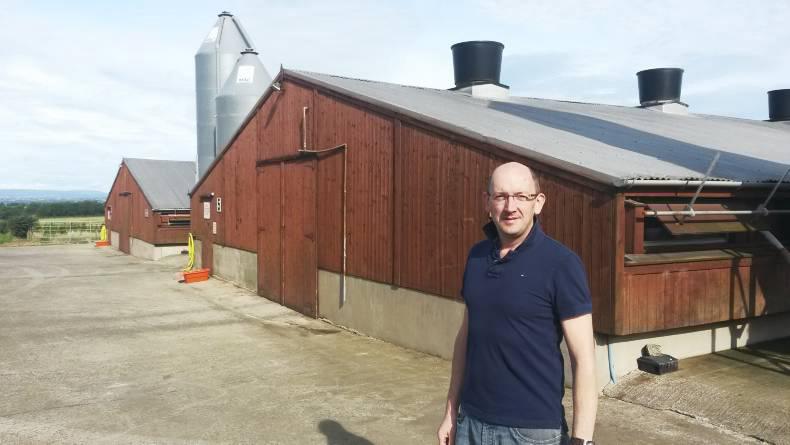
Farmer getting the heat benefits
Thomas Forgrave rears broiler chickens for Moy Park up to 42 days old in six poultry houses on his farm near Ballymoney, Co Antrim. He installed six biomass boilers 18 months ago to heat each of his sheds using fan heaters.
Thomas decided to install six individual heaters, as the tariff paid for biomass boilers from 20 to 99kW is 6.4 pence per kWh, whereas the next bracket from 100 to 999kW boilers is only 1.5p/kWh. This made it much more economical to have a boiler for each shed, as opposed to one large boiler for the whole farm.
Three 20t meal bins store wood pellets that are fed in automatically to a burning chamber which produces heat to maintain water in a 3,000-litre buffer tank at 80°C. This water is then pumped to the shed where a radiator in the fan heaters heat the house.
Each house cost around £50,000 to £60,000 to convert and the coniferous timber wood pellets cost from £165 to £185/t. The amount used differs greatly depending on the time of year and the weather.
Servicing and electricity costs on the farm have increased since the new system was installed.
“The electricity bill is easily up by 50% from before, but this is understandable with the power needed for the boiler, water pumps, computer system and fan heaters,” Thomas said.
Houses are maintained at 32 to 34°C at day one and then gradually brought down to 22 to 24°C. The boilers are switched on a few days before the birds arrive and are switched off for the last 10 days as the birds are eventually capable of making their own heat.
The houses on the farm were originally heated with gas heaters. Thomas has observed improvements to the litter quality and less hock burn and lameness in the broilers since converting to biomass. This is due to no water vapour being produced from the heaters.
“The biggest benefit is bird welfare because of this. It is also more pleasant for the farmer, with no smell from ammonia. Feed conversion ratio has improved since I changed the heaters,” Thomas said.
There is no cap on RHI for the amount of entrants and the energy paid for, so there has been wide uptake of the scheme with anyone with a high-heat requirement. RHI is paid for 20 years for each technology.
The RHI is currently under review for new entrants to the scheme. Changes such as increasing the upper limit for the size of boiler for higher payments and possibly imposing a cap on the amount paid for a technology per time period have been rumoured.
Changes are planned to come into force from around October and are likely to be announced in the coming weeks.
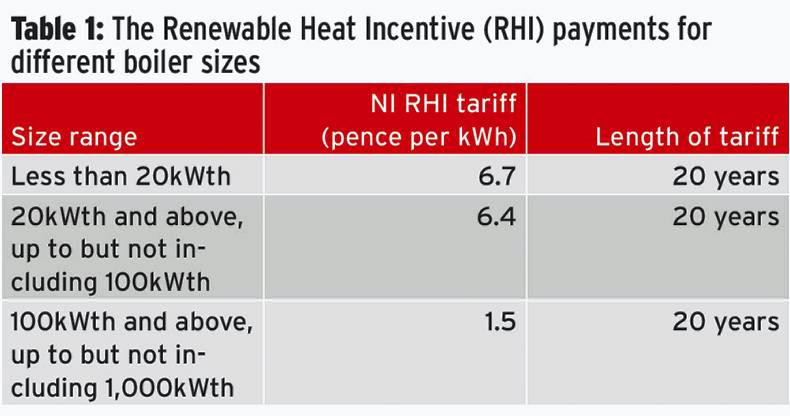
SHARING OPTIONS: