There are many systems to help set the rate of fertiliser spreading correctly. The removal of a disc and the weighing of the fertiliser that falls into a bucket in 30 seconds and some simple calculations can give large improvements in rate control for a small investment of time.
This is often more difficult as the spreader ages due to corrosion of the disc removal mechanism. And more harm may be done to the pattern and rate during the removal of the disc than would be gained by doing the test.
Bogballe has the S-indicator, which enables the flow rate of the fertiliser to be assessed using a hanging funnel separate from the machine. Vicon has an app where you input the density of the fertiliser and it calculates the setting required.
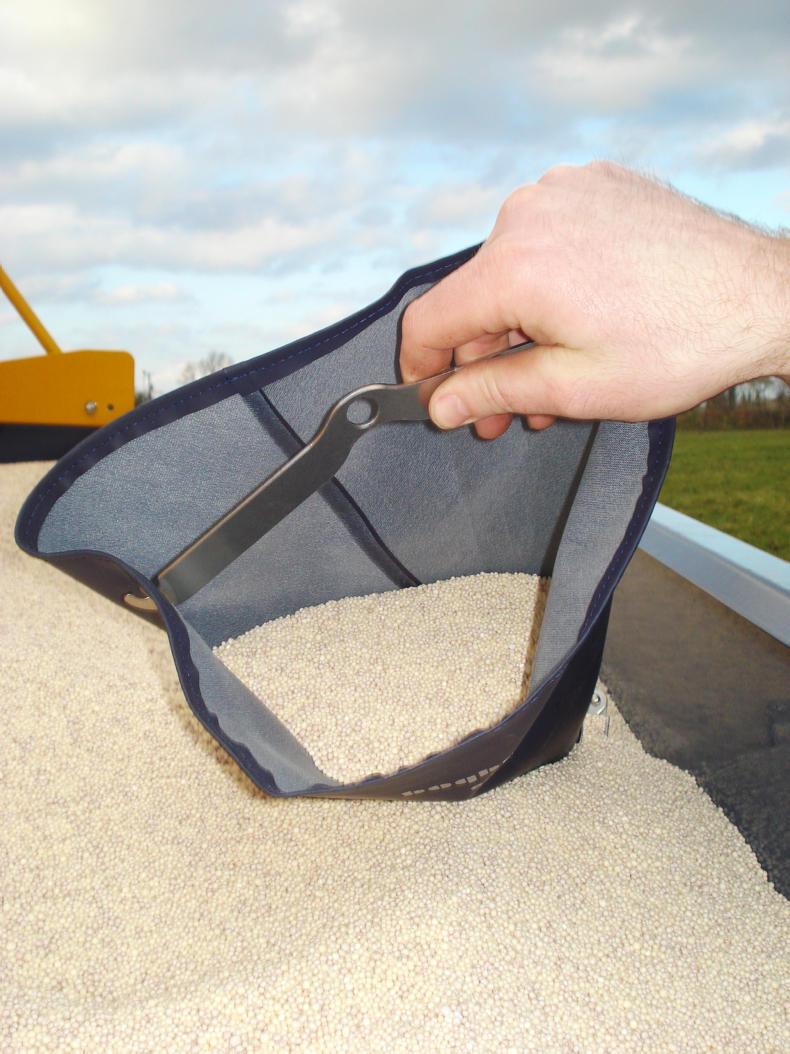
The S-indicator from Bogballe is a simple rate setting tool. The S-indicator from Bogballe is a simple rate setting tool.
Amazone recently brought out a new app for checking the spread pattern of your spreader. Instead of using the standard collection trays to catch the fertiliser, mats are placed on the ground. When the fertiliser has been spread over the area, a photo of each mat is taken and the app calculates the spread pattern of the spreader. The app is called EasyCheck and will be available shortly.
Forward speed
The next step in technology is weight cells on your machine. These, which are linked to radar speed detection, mean that the rate adjusts depending on your forward speed.
The rate can be set on an in-cab control unit. These systems are available on all the main manufacturers’ mid- to high-end machines.
Headland spreading technology is an area where the manufacturers differ in the approach they take, ranging from drop-down deflector vanes to deflect the fertiliser away from the headland or reversing the disc rotation to narrow the spread pattern. These reduce the amount of fertiliser thrown into the hedge.
Precise headland spreading is essential in areas where watercourses border your field.
All of the manufacturers’ systems have to meet European standards for this reason.
Simple GPS systems can also bring improvements in driving accuracy. Entry-level systems can be bought for €1,200 to €1,500.
One of these guidance systems with a competent operator and a modern twin-disc spreader can bring measurable savings in comparison to stepping out bout widths on grassland or ploughed ground pre-sowing.
The next step in technology is linking the GPS system to the spreader. This allows the spreader to determine its actual working position in the field. GPS systems can provide the fertiliser spreader with the information required to operate full sectional control in short ground, as well as automatically opening and closing the shutters for headland turning.
Most of these systems can be linked using an Isobus connection. Isobus is a generic connection system used by implement manufacturers and tractor manufacturers to link their machines.
It removes the requirement for a separate control box for the spreader, giving spreader control from the tractor’s own screen. It is only in the most recent update that it has become fully and consistently functional across most machines.
More control
Spreaders are now starting to move away from the mechanical-drive systems we are used to, where the pto shaft turns a gear assembly and the discs turn at a constant and equal speed. This will allow not only for much greater control of disc speed, but also the ability to run each disc at a different speed to modify the spread pattern, similar to section control on a sprayer.
The spread pattern can also be modified by differing the drop point of the fertiliser on to the disc. If the fertiliser is dropped closer to the centre of the disc, it will leave at a greater speed, giving you a wider spread width.
High accuracy
Both the variable speed disc drives and the differing drop area combined can give the very high accuracy required to match up to the data that can be gained these days. Yield mapping from combines, sensor data and drone sensor data can be overlaid on to field maps and then, with a combination of the latest technology available on spreaders, the fertiliser can be targeted where it is thought to be needed.
The main manufacturers have different ideas on how to achieve this accuracy but all are based on the same principle that the more information you have about the material being spread and the area being spread, the better and more accurate job that can be done.
There are many systems to help set the rate of fertiliser spreading correctly. The removal of a disc and the weighing of the fertiliser that falls into a bucket in 30 seconds and some simple calculations can give large improvements in rate control for a small investment of time.
This is often more difficult as the spreader ages due to corrosion of the disc removal mechanism. And more harm may be done to the pattern and rate during the removal of the disc than would be gained by doing the test.
Bogballe has the S-indicator, which enables the flow rate of the fertiliser to be assessed using a hanging funnel separate from the machine. Vicon has an app where you input the density of the fertiliser and it calculates the setting required.
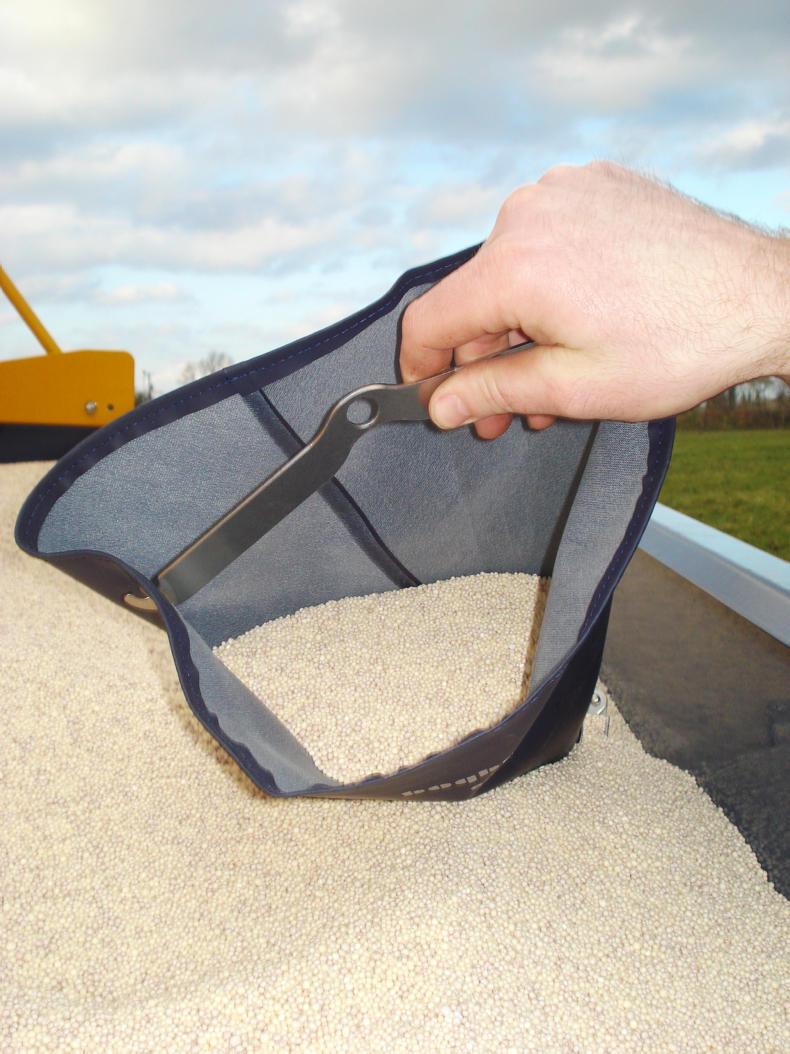
The S-indicator from Bogballe is a simple rate setting tool. The S-indicator from Bogballe is a simple rate setting tool.
Amazone recently brought out a new app for checking the spread pattern of your spreader. Instead of using the standard collection trays to catch the fertiliser, mats are placed on the ground. When the fertiliser has been spread over the area, a photo of each mat is taken and the app calculates the spread pattern of the spreader. The app is called EasyCheck and will be available shortly.
Forward speed
The next step in technology is weight cells on your machine. These, which are linked to radar speed detection, mean that the rate adjusts depending on your forward speed.
The rate can be set on an in-cab control unit. These systems are available on all the main manufacturers’ mid- to high-end machines.
Headland spreading technology is an area where the manufacturers differ in the approach they take, ranging from drop-down deflector vanes to deflect the fertiliser away from the headland or reversing the disc rotation to narrow the spread pattern. These reduce the amount of fertiliser thrown into the hedge.
Precise headland spreading is essential in areas where watercourses border your field.
All of the manufacturers’ systems have to meet European standards for this reason.
Simple GPS systems can also bring improvements in driving accuracy. Entry-level systems can be bought for €1,200 to €1,500.
One of these guidance systems with a competent operator and a modern twin-disc spreader can bring measurable savings in comparison to stepping out bout widths on grassland or ploughed ground pre-sowing.
The next step in technology is linking the GPS system to the spreader. This allows the spreader to determine its actual working position in the field. GPS systems can provide the fertiliser spreader with the information required to operate full sectional control in short ground, as well as automatically opening and closing the shutters for headland turning.
Most of these systems can be linked using an Isobus connection. Isobus is a generic connection system used by implement manufacturers and tractor manufacturers to link their machines.
It removes the requirement for a separate control box for the spreader, giving spreader control from the tractor’s own screen. It is only in the most recent update that it has become fully and consistently functional across most machines.
More control
Spreaders are now starting to move away from the mechanical-drive systems we are used to, where the pto shaft turns a gear assembly and the discs turn at a constant and equal speed. This will allow not only for much greater control of disc speed, but also the ability to run each disc at a different speed to modify the spread pattern, similar to section control on a sprayer.
The spread pattern can also be modified by differing the drop point of the fertiliser on to the disc. If the fertiliser is dropped closer to the centre of the disc, it will leave at a greater speed, giving you a wider spread width.
High accuracy
Both the variable speed disc drives and the differing drop area combined can give the very high accuracy required to match up to the data that can be gained these days. Yield mapping from combines, sensor data and drone sensor data can be overlaid on to field maps and then, with a combination of the latest technology available on spreaders, the fertiliser can be targeted where it is thought to be needed.
The main manufacturers have different ideas on how to achieve this accuracy but all are based on the same principle that the more information you have about the material being spread and the area being spread, the better and more accurate job that can be done.
SHARING OPTIONS: