As Ireland has so few operational
anaerobic digestion (AD) plants,
developing our 2030 biomethane targets will essentially mean starting a new industry nearly from scratch.
As such, there’s a need for training in this area. Recently, Cré, the Composting and Anaerobic Digestion Association of Ireland, hosted a training course on planning for an AD facility.
Given that most AD projects are currently in various planning stages, whether in their initial concept phase, undergoing economic assessments, or navigating the planning process, this training course proved timely.
The course was designed for all stakeholders involved in AD and it attracted a diverse range of interest from the entire industry. Attendees included representatives from Gas Networks Ireland, the EPA, local authorities, the Department of Agriculture and Environment, and waste management companies.
The two-day programme included presentations, practical exercises and a site visit to an operational AD plant that generates electricity. The Irish Farmers Journal had the opportunity to participate in the course, and in this article, we’ll highlight some of the key topics covered during the training.
AD biology
AD occurs in four stages: hydrolysis, acidogenesis, acetogenesis, and methanogenesis, all of which take place within tanks.
Understanding each of these stages and the specific environmental conditions required, such as pH, temperature, and retention time, provides insights into the design, construction, and operation of your plant.
Similarly, understanding how the process works is essential for ongoing monitoring of the plant and for quickly resolving any issues that may arise. The microorganisms in an AD tank are alive, and if not managed correctly, they can become unhealthy or die, all of which can have significant implications for gas production. Inhibitors such as heavy metals, excessive salts and minerals, surfactants and antibiotics can damage the microorganisms, so regularly testing feedstock and sampling the tank is vital.
Feedstock types
An AD plant’s design and capacity should be based on the available feedstock rather than designing the plant first and then searching for feedstock. The type of material you supply to the digester has significant implications for the plant’s design, planning and licensing requirements and operational parameters.
Therefore, having a clear understanding of the feedstock you intend to use from the early stages is crucial.
Various feedstocks are used in AD, including food waste, commercial waste, municipal waste, sludges, agricultural slurries, manure, straw, and biomass sources like grass silage, maize, beet, and whole crops.
During the course, participants engaged in an exercise to determine the potential biomethane yield from each feedstock. For instance, one tonne of grass silage with a dry matter content of 35% could generate approximately 95m3 of biomethane, whereas one tonne of pig slurry with a dry matter content of 6% would produce just 12m3.
Site visit
Day one concluded with a site visit to Gilfresh AD (pictured right) in Loughgall, Co Armagh. This plant has been in operation since 2016 and is located on the premises of vegetable growers and packers Gilfresh Produce.

Attendees collect their certificates after the course.
The plant is supplied with various inputs, including vegetable waste, chicken litter, cattle slurry, grass silage, fodder beet, hybrid rye, and maize.
Originally, it had a generating capacity of 500 kW, but in 2017, a second 500 kW CHP unit was installed, which not only generates electricity but also provides heat and electricity for a nearby greenhouse.
Technology and plant layout
The type of plant you wish to build and the volume of feedstock, as well as the regulations you must adhere to, will shape the plant’s design and layout. Wet digestion systems, using insulated, heated concrete tanks, is the most common design, but dry digestion systems also have their place.
Gas cleaning and upgrading systems also vary depending on the supplier.
To upgrade biogas to biomethane, you can employ various technologies such as scrubbing systems, membrane systems, pressure swing adsorption, cryogenic distillation, or a novel system that uses metal-organic frameworks (MOF). Each of these options has its own set of advantages and disadvantages.
Waste licence or no waste licence
Another topic covered was licencing requirements. Generally, AD plants which process waste must apply for an EPA waste licence when total tonnage is over 10,000t. This includes food waste, cooking oil, brown bin waste, meat products etc. Facilities below this tonnage can
apply for a waste license permit through their local authority.
However, there is significant lack of clarity within the industry regarding the classification of slurry as either waste or not. Sites licensed by the EPA for waste management are associated with high costs and stringent ongoing monitoring.
If slurry were to be classified as waste, it would fundamentally alter the character of an agricultural AD project, leading to a substantial rise in costs and posing challenges in obtaining planning permission and acceptance from local communities.
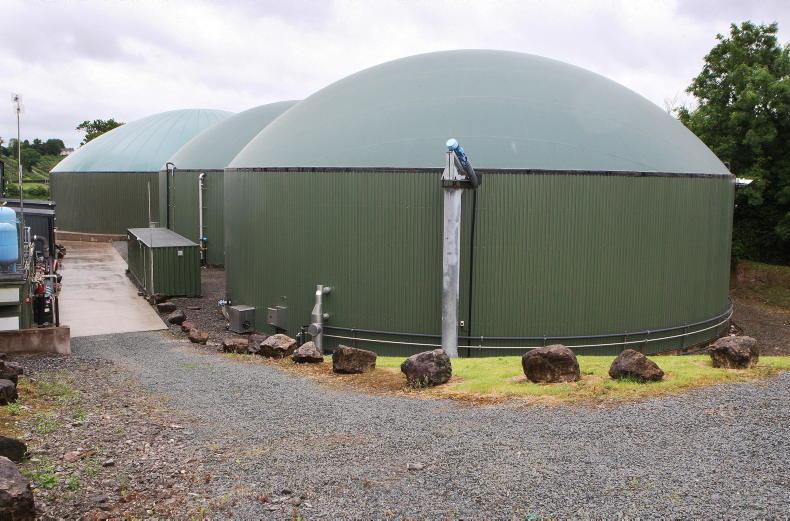
The three digesters on Gilfresh Produce.
The process of ensuring compliance with regulations related to Animal By-Products and other licensing requirements, such as Industrial Emission Licences, were also covered in the course.
Health and safety
Arguably, the most crucial module in the course focuses on health and safety, delivered by Dr Les Gornall. While AD is not a new concept, with thousands of plants operating in Europe, it is not without its dangers and risks, akin to any development. This module covers the primary hazards associated with AD projects, notably hydrogen sulphide (H2S) poisoning, gas asphyxiation, explosions, and incidents like slips, trips, and falls.
More importantly, the course provides
guidance on accident prevention and the implementation of best-practice safety standards and the use of safety equipment, including gas meters.
As Ireland has so few operational
anaerobic digestion (AD) plants,
developing our 2030 biomethane targets will essentially mean starting a new industry nearly from scratch.
As such, there’s a need for training in this area. Recently, Cré, the Composting and Anaerobic Digestion Association of Ireland, hosted a training course on planning for an AD facility.
Given that most AD projects are currently in various planning stages, whether in their initial concept phase, undergoing economic assessments, or navigating the planning process, this training course proved timely.
The course was designed for all stakeholders involved in AD and it attracted a diverse range of interest from the entire industry. Attendees included representatives from Gas Networks Ireland, the EPA, local authorities, the Department of Agriculture and Environment, and waste management companies.
The two-day programme included presentations, practical exercises and a site visit to an operational AD plant that generates electricity. The Irish Farmers Journal had the opportunity to participate in the course, and in this article, we’ll highlight some of the key topics covered during the training.
AD biology
AD occurs in four stages: hydrolysis, acidogenesis, acetogenesis, and methanogenesis, all of which take place within tanks.
Understanding each of these stages and the specific environmental conditions required, such as pH, temperature, and retention time, provides insights into the design, construction, and operation of your plant.
Similarly, understanding how the process works is essential for ongoing monitoring of the plant and for quickly resolving any issues that may arise. The microorganisms in an AD tank are alive, and if not managed correctly, they can become unhealthy or die, all of which can have significant implications for gas production. Inhibitors such as heavy metals, excessive salts and minerals, surfactants and antibiotics can damage the microorganisms, so regularly testing feedstock and sampling the tank is vital.
Feedstock types
An AD plant’s design and capacity should be based on the available feedstock rather than designing the plant first and then searching for feedstock. The type of material you supply to the digester has significant implications for the plant’s design, planning and licensing requirements and operational parameters.
Therefore, having a clear understanding of the feedstock you intend to use from the early stages is crucial.
Various feedstocks are used in AD, including food waste, commercial waste, municipal waste, sludges, agricultural slurries, manure, straw, and biomass sources like grass silage, maize, beet, and whole crops.
During the course, participants engaged in an exercise to determine the potential biomethane yield from each feedstock. For instance, one tonne of grass silage with a dry matter content of 35% could generate approximately 95m3 of biomethane, whereas one tonne of pig slurry with a dry matter content of 6% would produce just 12m3.
Site visit
Day one concluded with a site visit to Gilfresh AD (pictured right) in Loughgall, Co Armagh. This plant has been in operation since 2016 and is located on the premises of vegetable growers and packers Gilfresh Produce.

Attendees collect their certificates after the course.
The plant is supplied with various inputs, including vegetable waste, chicken litter, cattle slurry, grass silage, fodder beet, hybrid rye, and maize.
Originally, it had a generating capacity of 500 kW, but in 2017, a second 500 kW CHP unit was installed, which not only generates electricity but also provides heat and electricity for a nearby greenhouse.
Technology and plant layout
The type of plant you wish to build and the volume of feedstock, as well as the regulations you must adhere to, will shape the plant’s design and layout. Wet digestion systems, using insulated, heated concrete tanks, is the most common design, but dry digestion systems also have their place.
Gas cleaning and upgrading systems also vary depending on the supplier.
To upgrade biogas to biomethane, you can employ various technologies such as scrubbing systems, membrane systems, pressure swing adsorption, cryogenic distillation, or a novel system that uses metal-organic frameworks (MOF). Each of these options has its own set of advantages and disadvantages.
Waste licence or no waste licence
Another topic covered was licencing requirements. Generally, AD plants which process waste must apply for an EPA waste licence when total tonnage is over 10,000t. This includes food waste, cooking oil, brown bin waste, meat products etc. Facilities below this tonnage can
apply for a waste license permit through their local authority.
However, there is significant lack of clarity within the industry regarding the classification of slurry as either waste or not. Sites licensed by the EPA for waste management are associated with high costs and stringent ongoing monitoring.
If slurry were to be classified as waste, it would fundamentally alter the character of an agricultural AD project, leading to a substantial rise in costs and posing challenges in obtaining planning permission and acceptance from local communities.
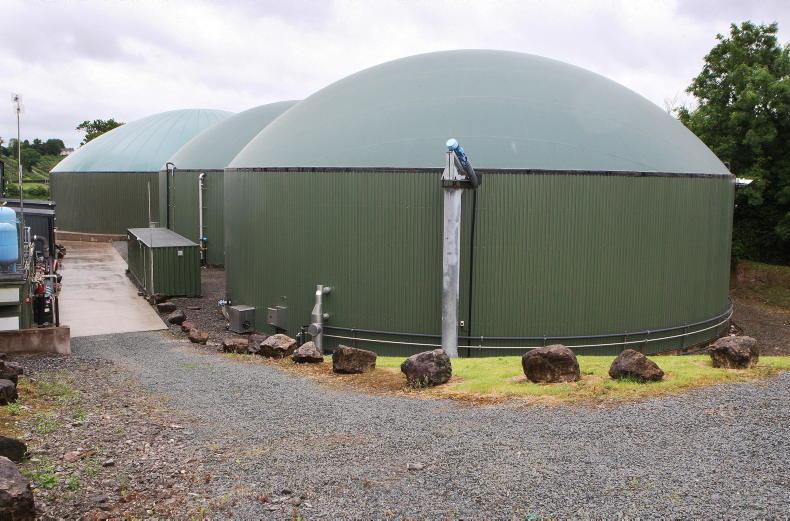
The three digesters on Gilfresh Produce.
The process of ensuring compliance with regulations related to Animal By-Products and other licensing requirements, such as Industrial Emission Licences, were also covered in the course.
Health and safety
Arguably, the most crucial module in the course focuses on health and safety, delivered by Dr Les Gornall. While AD is not a new concept, with thousands of plants operating in Europe, it is not without its dangers and risks, akin to any development. This module covers the primary hazards associated with AD projects, notably hydrogen sulphide (H2S) poisoning, gas asphyxiation, explosions, and incidents like slips, trips, and falls.
More importantly, the course provides
guidance on accident prevention and the implementation of best-practice safety standards and the use of safety equipment, including gas meters.
SHARING OPTIONS: