Based in Clerihan, Co Tipperary, Jim Ryan Contracting Services Ltd is a large agricultural contracting business. With 12 full-time employees, the team is kept busy during the summer months with their John Deere self-propelled silage harvester, two PÖttinger forage wagons and four balers.
Previously running two Lely Tornado combination baler-wrappers for baling silage for eight seasons, Ryans upgraded to a new McHale Fusion 3+ in 2017 and a new Kuhn FBP 3135 in 2018. They also runs two Lely Welger balers for hay and straw.
Pickup reel
The FBP 3135 is fitted with a 2.3m pickup reel with five rows of tine bars. The tines have a spacing of 61mm. Owner Kieran Ryan explained that after checking through the pickup reel, it’s good to go for the season ahead, with no maintenance needed. The baler also came as standard with a crop roller.
Kieran outlined that the short distance between the pickup tines and the rotor means there’s no dead spot for grass to sit in-between, allowing for a consistent crop flow. The FBP 3135 comes with a beefy rotor, spanning the entire width of the feed-in area. The rotor is manufactured from hardox steel.
Knives
Just behind the rotor sits a 23-knife selectable floor. From new, the combination unit comes with the option of either a 14- or 23-knife bank, providing a theoretical chop length of 70mm and 45mm respectively. Many Irish contractors would opt for the 23-knife selectable floor, meaning they can run 11 knives one day and 12 knives the next day.
Each knife is spring-protected and Kuhn also has a feature that keeps the knives clean, to help chop the grass. The cleaning interval can be adjusted via the control terminal. Kieran said he has been really impressed with the throughput capacity of the pickup reel and feed roller. He typically sharpens the knives after every 500 bales.
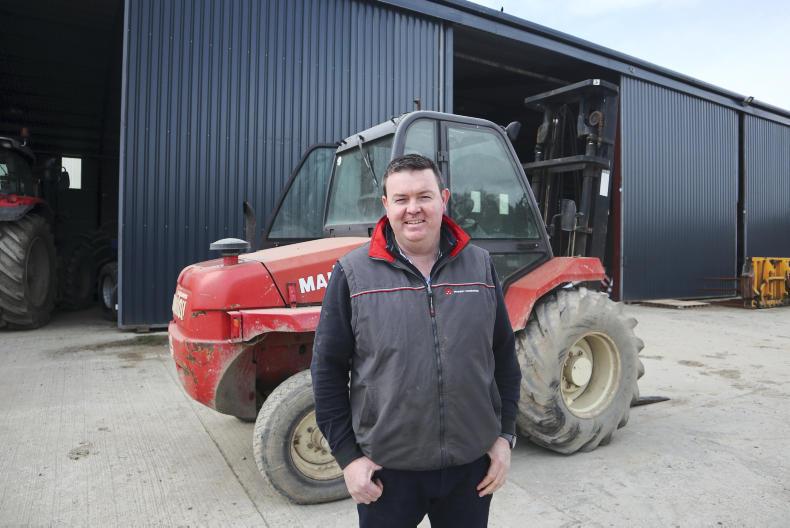
Kieran Ryan.
Drop-floor
The floor and knives can be hydraulically lowered from the cab in the case of a rotor blockage. After the blockage is cleared, they are brought back into the work position.
When baling a raked or large swath of grass with any baler, occasionally the baler may swallow a lump of grass at the last second just before the net or film is about to be engaged, causing the slip clutch to go off. One feature that differentiates Kuhn is that the rotor drive can be disengaged from the bale chamber drive, enabling the binding and discharge of the bale from the chamber.
The rotor disengagement and drop-floor technology allow the operator to get the machine going again quickly. Kieran said this was one feature that really stood out for him.
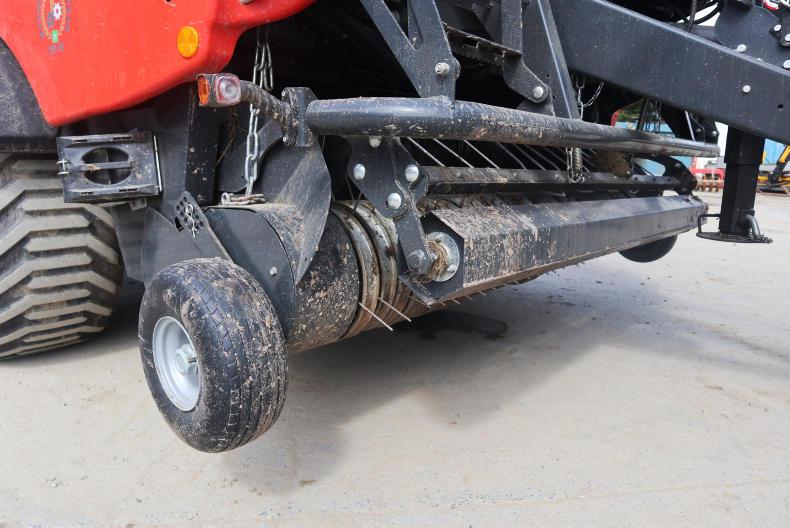
The FBP 3135 is fitted with a 2.3m pickup reel with five rows of tine bars.
Net/film binding
Changing from net to film binding can be done without changing the film or net roll’s position. The operator has to just change the feed-in of the desired application material, the settings on the control terminal and the pulley settings at the side of the intake roller. Kieran said the pulley needed a lot of lubrication or it could easily seize, especially if working in warm dusty weather.
When using conventional film, two rolls need to be inserted on to the reels to bind the entire width of the bale. During bale ejection, the last roller on the back door is automatically disengaged to prevent film damage. Despite people saying two rolls of conventional film work out cheaper than using the wider mantle-type film, Kieran said that based on his 2018 costings this is not true and both systems work out the same pricewise.
Bale chamber
The FBP 3135 has a redesigned bale chamber, consisting of 18 rollers. The rollers are made from 3.2mm thick steel and have 50mm double-raced bearings on the drive side.
All bearings are centrally greased using a Beka Max automatic bearing greasing system. The rollers have built-in scrapers to push the material out and away from the bearings.
Sensors on the back door monitor bale growth from 80%, notifying the operator about the baling process through the bale growth indicator and allowing them to guide the baler according to the left-right bale chamber filling indication displayed on the terminal.
One attribute that Kieran said impressed him over 2018 season was the consistently perfect bale shape and density.
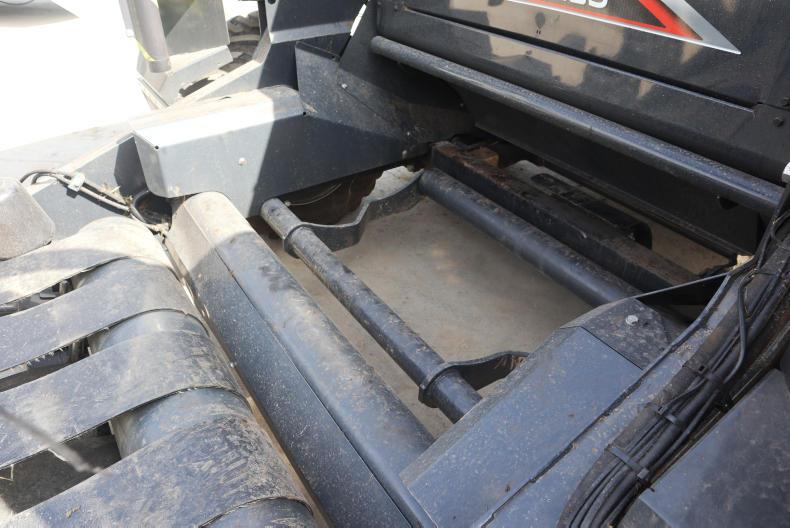
The wrapping table is tilted forward and the transfer arm loads the bale on to the table.
Wrapping system
The transfer arm collects the bale as it leaves the chamber. The wrapping table is tilted forward and the arm loads the bale onto the table before the tailgate shuts automatically and the wrapping process begins. Kieran said the transfer arm on the Kuhn can be a little slower than other balers on the market but that it makes up for it with other attributes.
The side guide protection plates allow for a secure bale transfer. The wrapping system uses a four-belt wrapping table with two large rollers and four side cones.
When the bale is ejected from the chamber, 60% of the bale is covered with stretch film. The 3D wrapping system applies film to the edges of the bale that have not already being covered by either film or net. Kuhn claims this is to increase the form stability compared to a conventional (2D) system. After completing the 3D wrapping cycle, 80% of the bale is covered in film and the remainder is wrapped conventionally.

The FBP 3135 sits on a tandem axle on four 500/45-22.5 flotation tyres.
Tandem axle
The FBP 3135 sits on a tandem axle on four 500/45-22.5 flotation tyres. Kieran said the tandem axle means the machine is very smooth on the road. He maintains it is very balanced and quite low, meaning it doesn’t get into any fits of bouncing while in transport. He said the fact that the machine is low means he can see the bale being wrapped from the cab of the tractor rather than watching it on the camera in the cab.
Kieran said that because of the extra axle, the machine is a little long, but that it hasn’t failed to get in any gap and it has minimal tail swing.
After putting 14,000 bales of a mixture of silage and haylage through the FBP 3135, Kieran said overall he has been very impressed with how the baler has performed throughout the 2018 season. He noted that 90% of his customers have gone down the route of using film on film. He added: “I like the film dispenser on the FBP 3135 and furthermore the fact that I can use conventional wrap in this system”.
Specs
Weight: 5,600kg
Width: 2.97m (9.41ft)
Length: 6.4m (21.19ft)
Knives: 23 knife selectable floor (combinations; 0-7-11-12-23)
Bale chamber: 18 rollers
Terminal: Isobus compatible
Pickup: 2.3m five tine bar camless
List price: €106,000 plus VAT
Based in Clerihan, Co Tipperary, Jim Ryan Contracting Services Ltd is a large agricultural contracting business. With 12 full-time employees, the team is kept busy during the summer months with their John Deere self-propelled silage harvester, two PÖttinger forage wagons and four balers.
Previously running two Lely Tornado combination baler-wrappers for baling silage for eight seasons, Ryans upgraded to a new McHale Fusion 3+ in 2017 and a new Kuhn FBP 3135 in 2018. They also runs two Lely Welger balers for hay and straw.
Pickup reel
The FBP 3135 is fitted with a 2.3m pickup reel with five rows of tine bars. The tines have a spacing of 61mm. Owner Kieran Ryan explained that after checking through the pickup reel, it’s good to go for the season ahead, with no maintenance needed. The baler also came as standard with a crop roller.
Kieran outlined that the short distance between the pickup tines and the rotor means there’s no dead spot for grass to sit in-between, allowing for a consistent crop flow. The FBP 3135 comes with a beefy rotor, spanning the entire width of the feed-in area. The rotor is manufactured from hardox steel.
Knives
Just behind the rotor sits a 23-knife selectable floor. From new, the combination unit comes with the option of either a 14- or 23-knife bank, providing a theoretical chop length of 70mm and 45mm respectively. Many Irish contractors would opt for the 23-knife selectable floor, meaning they can run 11 knives one day and 12 knives the next day.
Each knife is spring-protected and Kuhn also has a feature that keeps the knives clean, to help chop the grass. The cleaning interval can be adjusted via the control terminal. Kieran said he has been really impressed with the throughput capacity of the pickup reel and feed roller. He typically sharpens the knives after every 500 bales.
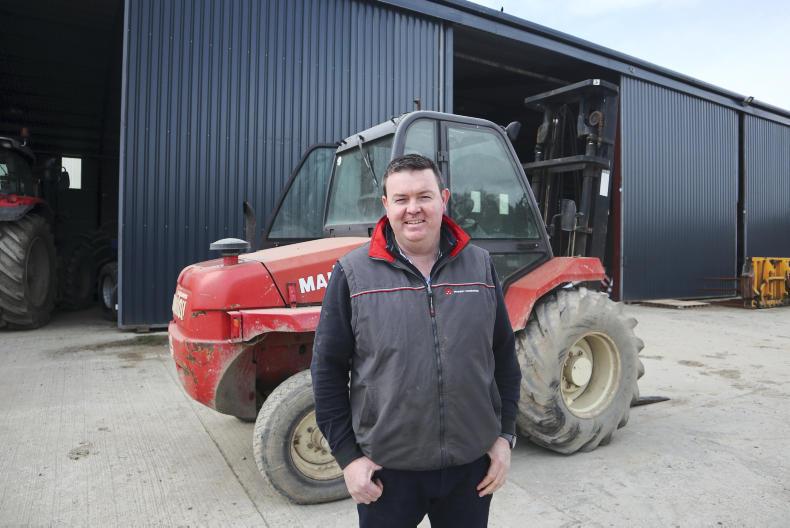
Kieran Ryan.
Drop-floor
The floor and knives can be hydraulically lowered from the cab in the case of a rotor blockage. After the blockage is cleared, they are brought back into the work position.
When baling a raked or large swath of grass with any baler, occasionally the baler may swallow a lump of grass at the last second just before the net or film is about to be engaged, causing the slip clutch to go off. One feature that differentiates Kuhn is that the rotor drive can be disengaged from the bale chamber drive, enabling the binding and discharge of the bale from the chamber.
The rotor disengagement and drop-floor technology allow the operator to get the machine going again quickly. Kieran said this was one feature that really stood out for him.
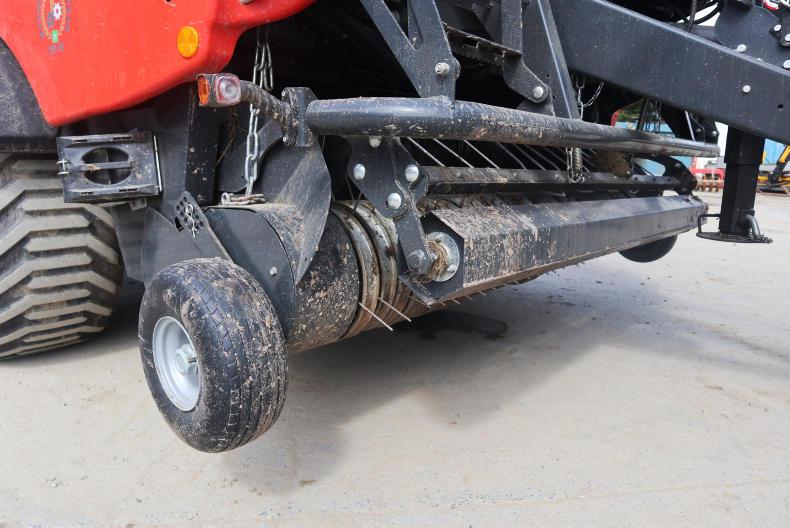
The FBP 3135 is fitted with a 2.3m pickup reel with five rows of tine bars.
Net/film binding
Changing from net to film binding can be done without changing the film or net roll’s position. The operator has to just change the feed-in of the desired application material, the settings on the control terminal and the pulley settings at the side of the intake roller. Kieran said the pulley needed a lot of lubrication or it could easily seize, especially if working in warm dusty weather.
When using conventional film, two rolls need to be inserted on to the reels to bind the entire width of the bale. During bale ejection, the last roller on the back door is automatically disengaged to prevent film damage. Despite people saying two rolls of conventional film work out cheaper than using the wider mantle-type film, Kieran said that based on his 2018 costings this is not true and both systems work out the same pricewise.
Bale chamber
The FBP 3135 has a redesigned bale chamber, consisting of 18 rollers. The rollers are made from 3.2mm thick steel and have 50mm double-raced bearings on the drive side.
All bearings are centrally greased using a Beka Max automatic bearing greasing system. The rollers have built-in scrapers to push the material out and away from the bearings.
Sensors on the back door monitor bale growth from 80%, notifying the operator about the baling process through the bale growth indicator and allowing them to guide the baler according to the left-right bale chamber filling indication displayed on the terminal.
One attribute that Kieran said impressed him over 2018 season was the consistently perfect bale shape and density.
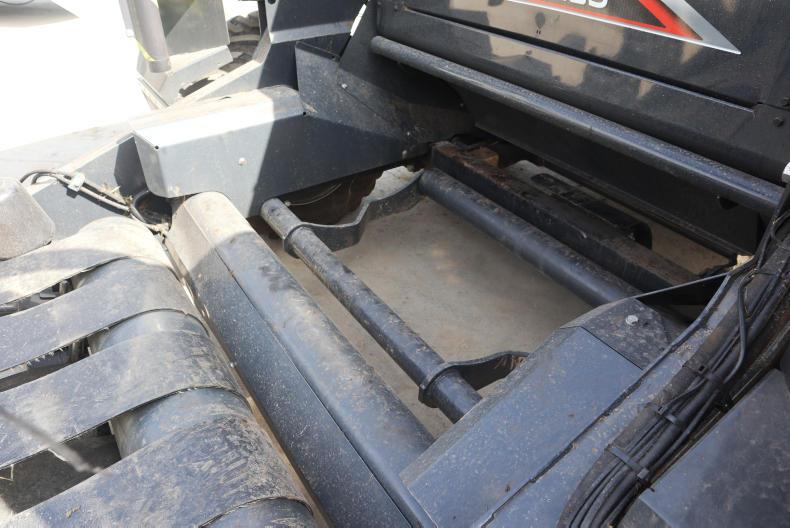
The wrapping table is tilted forward and the transfer arm loads the bale on to the table.
Wrapping system
The transfer arm collects the bale as it leaves the chamber. The wrapping table is tilted forward and the arm loads the bale onto the table before the tailgate shuts automatically and the wrapping process begins. Kieran said the transfer arm on the Kuhn can be a little slower than other balers on the market but that it makes up for it with other attributes.
The side guide protection plates allow for a secure bale transfer. The wrapping system uses a four-belt wrapping table with two large rollers and four side cones.
When the bale is ejected from the chamber, 60% of the bale is covered with stretch film. The 3D wrapping system applies film to the edges of the bale that have not already being covered by either film or net. Kuhn claims this is to increase the form stability compared to a conventional (2D) system. After completing the 3D wrapping cycle, 80% of the bale is covered in film and the remainder is wrapped conventionally.

The FBP 3135 sits on a tandem axle on four 500/45-22.5 flotation tyres.
Tandem axle
The FBP 3135 sits on a tandem axle on four 500/45-22.5 flotation tyres. Kieran said the tandem axle means the machine is very smooth on the road. He maintains it is very balanced and quite low, meaning it doesn’t get into any fits of bouncing while in transport. He said the fact that the machine is low means he can see the bale being wrapped from the cab of the tractor rather than watching it on the camera in the cab.
Kieran said that because of the extra axle, the machine is a little long, but that it hasn’t failed to get in any gap and it has minimal tail swing.
After putting 14,000 bales of a mixture of silage and haylage through the FBP 3135, Kieran said overall he has been very impressed with how the baler has performed throughout the 2018 season. He noted that 90% of his customers have gone down the route of using film on film. He added: “I like the film dispenser on the FBP 3135 and furthermore the fact that I can use conventional wrap in this system”.
Specs
Weight: 5,600kg
Width: 2.97m (9.41ft)
Length: 6.4m (21.19ft)
Knives: 23 knife selectable floor (combinations; 0-7-11-12-23)
Bale chamber: 18 rollers
Terminal: Isobus compatible
Pickup: 2.3m five tine bar camless
List price: €106,000 plus VAT
SHARING OPTIONS: