Farming a total of 52ha outside Foxford in Co Mayo, Shane and Brenda Hughes are readjusting to life as dairy farmers.
The Hughes family got out of dairy farming in 2003. At the time, they were milking a small number of cows in very old facilities and the investments required, in the midst of the quota era, just didn’t stack up.
In the meantime, Shane worked off-farm in construction, built up a herd of 65 suckler cows and a sheep flock and set up a farm machinery contracting business also.
The lure of dairy returned and, in 2020, Shane and Brenda made the decision to get back into milking cows.
The long-term plan is to milk between 80 and 100 cows which they hope will be sufficient to provide a good family farm income for their three children – Charlie, Ciara and Conor.
The farm is in two splits, with 25ha in the milking block supporting a herd of 69 cows presently.
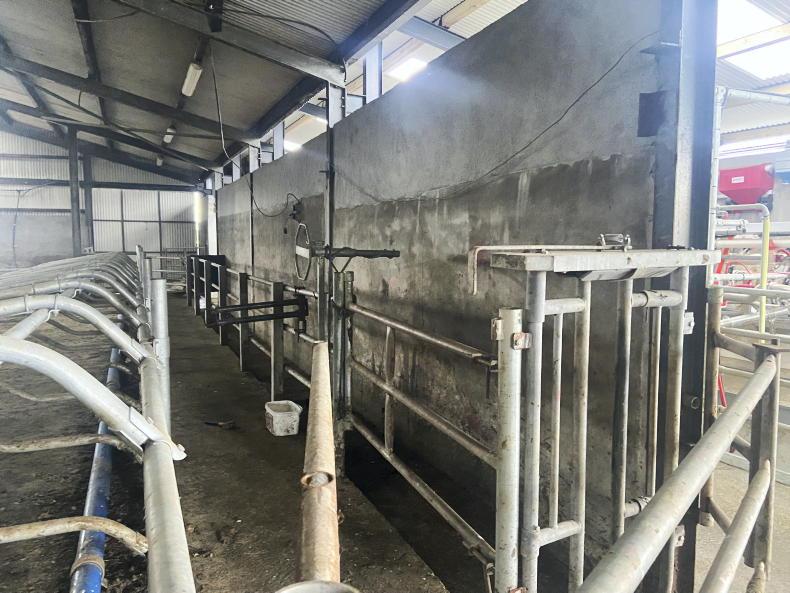
The crush is built on to the side of the parlour.
Calves, heifers and most of the silage are all on the out-farm located about two miles away.
The first task was to work on roadways, water and fencing, with all of this work starting in March 2020. Building work began in August 2020.
Existing cattle and sheep sheds on the farm were converted to cow cubicles. A new slatted tank was constructed to double as extra slurry storage and as a collecting yard. A new silage slab was also constructed.
The 14-unit Pearson milking parlour was built in an existing lean-to on to the now cubicle shed. The cows enter the slatted and roofed collecting yard and exit the parlour by turning left and back into the shed where they have the option of going through a new crush or down the feed passage and out to the fields.

The new 14-unit Pearson on Shane Hughes's farm.
“I had originally planned to put the parlour at the other side of the shed, closer to the house but there is more space and cow flow is better where it went.
“The other side of the shed is a straw-bedded area for calving cows and rearing calves. We use the old sheep hurdles as calf pens and they work great,” Shane says.
There are now 82 cubicles in the yard on the home farm, with 50 cubicles in a shed on the out-farm, where the heifers stay for the winter. Shane used to make all round-bale silage in the past but a new silage slab means he is making pit silage and drawing it back from the out-farm.
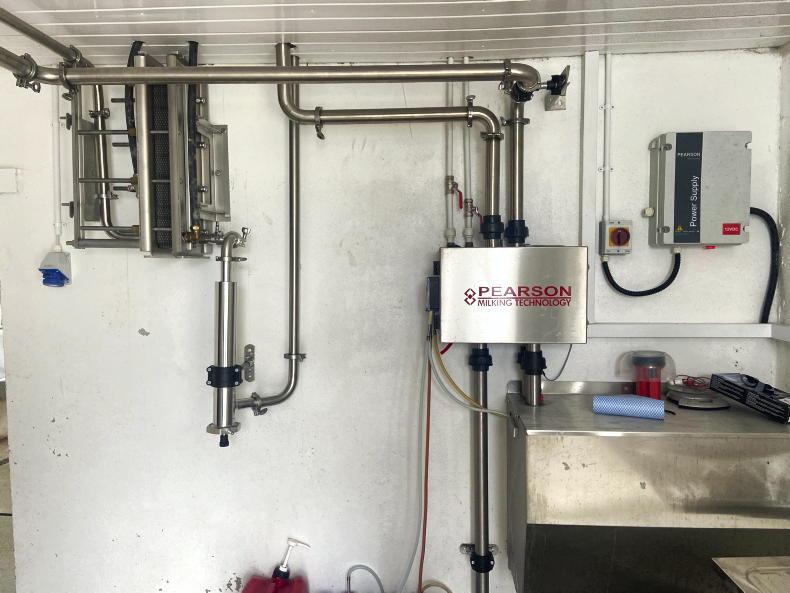
The dairy is finished to a high level.
The integration of the cubicles into the existing shed on the home farm has been excellent.
A small flow channel links up the new tank with the existing tank. The building work was completed by Ray Kelly, whom Shane and Brenda have nothing but good things to say about. Shane helped him throughout with the concrete and steel work. Four new automatic scrapers were installed to keep passageways clean.
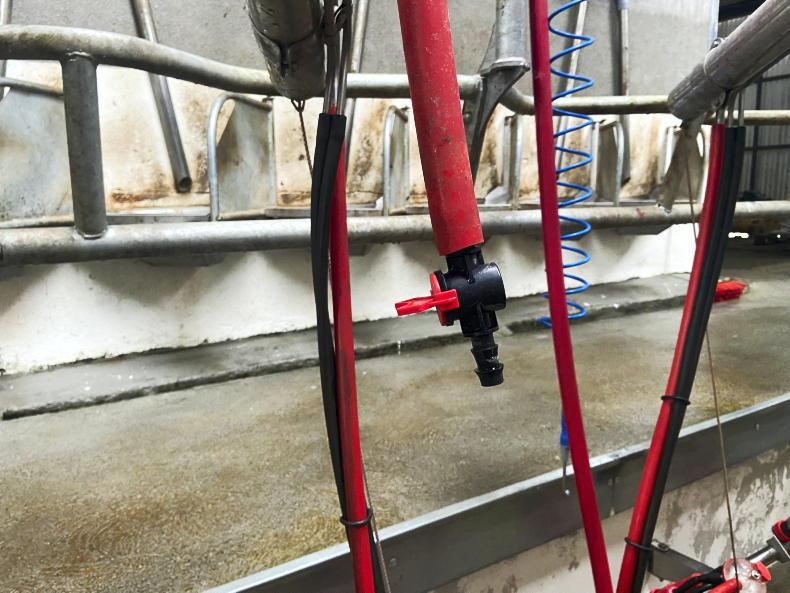
Vacuum line to plug in dump bucket.
A new 14-unit Pearson parlour was installed by local dealer Jarlath Colleran. Shane was humming and hawing about how many units to install but, in the end, he settled for 14.
A high level of technology is employed, with automatic cluster removers, variable speed vacuum pump, milk meters, automatic meal feeders and an automatic wash system.
A zig-zag rump rail and angled meal trough means that the cows line up well, even with nearly all heifers in the herd this year. The plant is at two foot six inch centres, with cow stands and pit 6ft wide. As is the norm with Pearson parlours, the parlour came factory-assembled so all that needed to be done was to fix the four stanchions in concrete and bolt the horizontal supports on to the walls.
Even the washdown hoses were installed on the plant at the factory.
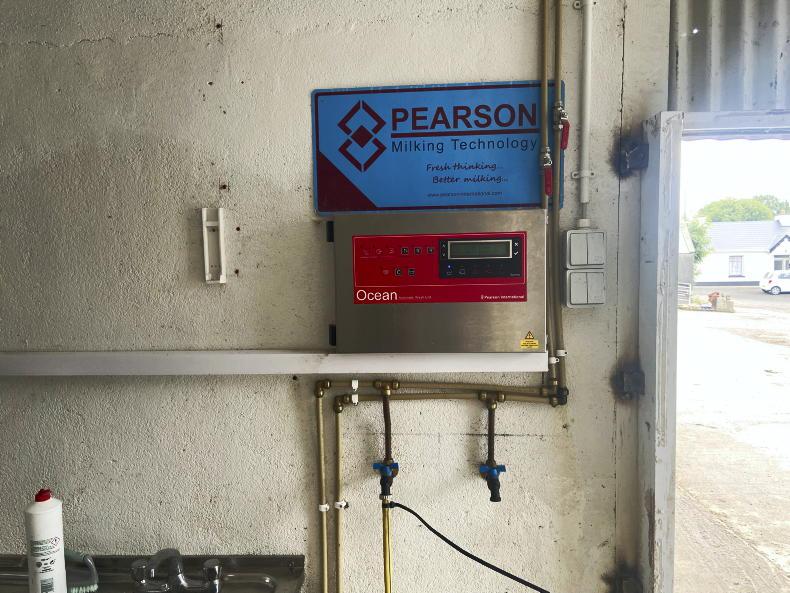
Automatic wash unit on the Hughes's farm.
Shane decided against installing a dump line but has two dump buckets that plug into the vacuum line when milking a cow whose milk is being dumped.
A dropper from the vacuum line is placed in between every second unit. This means that a cow with mastitis is not being milked with a cluster that is potentially going to be placed on a clean cow next. It’s also quicker to use as there are no hoses to be changed in order to milk the dump cow.
“The plant can be upgraded with extra technology at any time in the future without changing what I already have, which was a big attraction of Pearson for me. I don’t have feed to yield but it’s something I would consider in the future.
“Generally, the cows are on a flat rate but I manually increase the feed to the higher yielders by pressing a button on the unit which will just feed that cow,” Shane says.

Individual feeders can be upgraded to feed to yield in time.
He says the milk meters are very useful for picking up any sick or problem cows as they will generally be back in milk. A few cases of pneumonia back in spring were detected early by monitoring the yields.
All the cows are Holstein Friesian and were purchased from three herds with help from Bobby Franks from the IHFA.
Liners and milk pipes are all red silicone and Shane opted for lightweight plastic shells, which are much lighter than the traditional stainless steel shells and are more pleasant to handle on cold days, he says. Front and back air gates can be operated from anywhere in the pit.
Milk quality is impressive so far with SCC averaging 50,000 to 70,000 cells/ml and TBC averaging 5,000 to 8,000 cfu/ml since they started milking.

Special Pearson dump bucket and milking unit.
All cows are wiped and stripped before clusters are attached. Shane and Brenda do 90% of the milkings together, with Brenda doing it on her own during the busy days when Shane is away at silage.
Jarlath Colleran got his own electrician to do the wiring for the new parlour, meaning Shane had very few people to deal with when the parlour was being constructed. An 8t top-fill meal bin was purchased off Condon Engineering. Shane says this is handy as if he ever runs out of meal it can be filled from the bucket of the loader.
Overall, the Hughes family are delighted with their investments and decision to go into dairy farming.
The sale of the suckler cows and cattle helped to purchase the dairy stock and a 10-year loan was taken out to part-fund the parlour and building work.
In terms of just the milking facilities, the plant cost €5,936 excluding VAT per unit including full meal feeding system and all stall work.

The top fill meal bin holds 8t.
A new 9,600-litre Packo bulk tank was installed at a cost of €23,562 excluding VAT.
A further €37,000 was spent between building work, digging tanks, slats, etc, for the milking parlour and collecting yard bringing the total spend to just over €143,000 for the 14-unit milking facility.
A TAMS grant was claimed and because Shane and Brenda are in a farm partnership, the investment ceiling was increased.
One area that Shane is bothered about is the amount of water being collected daily between washing the plant and cleaning the floors and yard area. He calculates that there are about 1,600 gallons of soiled water being gathered daily but is not sure on how this can be reduced without compromising on hygiene.
The parlour and milking facilities are looking spotless and you can see the pride that the family takes in producing quality milk.
Farming a total of 52ha outside Foxford in Co Mayo, Shane and Brenda Hughes are readjusting to life as dairy farmers.
The Hughes family got out of dairy farming in 2003. At the time, they were milking a small number of cows in very old facilities and the investments required, in the midst of the quota era, just didn’t stack up.
In the meantime, Shane worked off-farm in construction, built up a herd of 65 suckler cows and a sheep flock and set up a farm machinery contracting business also.
The lure of dairy returned and, in 2020, Shane and Brenda made the decision to get back into milking cows.
The long-term plan is to milk between 80 and 100 cows which they hope will be sufficient to provide a good family farm income for their three children – Charlie, Ciara and Conor.
The farm is in two splits, with 25ha in the milking block supporting a herd of 69 cows presently.
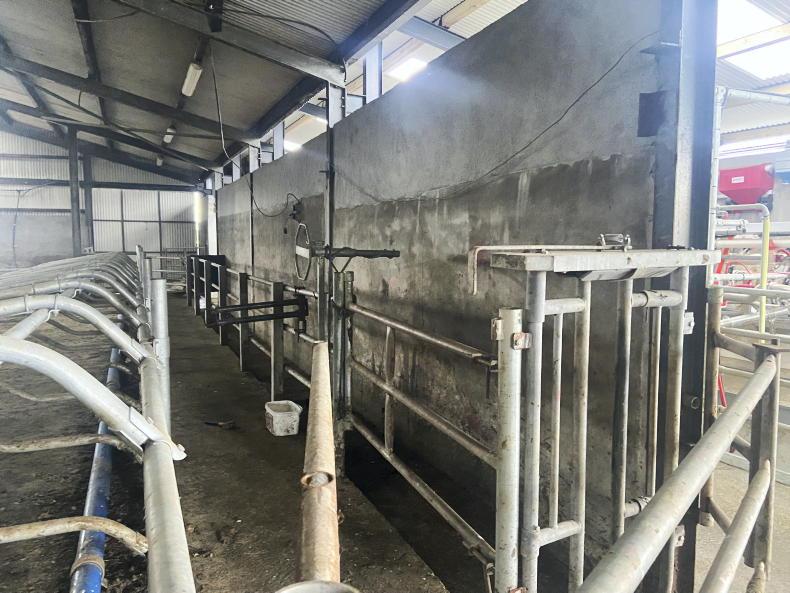
The crush is built on to the side of the parlour.
Calves, heifers and most of the silage are all on the out-farm located about two miles away.
The first task was to work on roadways, water and fencing, with all of this work starting in March 2020. Building work began in August 2020.
Existing cattle and sheep sheds on the farm were converted to cow cubicles. A new slatted tank was constructed to double as extra slurry storage and as a collecting yard. A new silage slab was also constructed.
The 14-unit Pearson milking parlour was built in an existing lean-to on to the now cubicle shed. The cows enter the slatted and roofed collecting yard and exit the parlour by turning left and back into the shed where they have the option of going through a new crush or down the feed passage and out to the fields.

The new 14-unit Pearson on Shane Hughes's farm.
“I had originally planned to put the parlour at the other side of the shed, closer to the house but there is more space and cow flow is better where it went.
“The other side of the shed is a straw-bedded area for calving cows and rearing calves. We use the old sheep hurdles as calf pens and they work great,” Shane says.
There are now 82 cubicles in the yard on the home farm, with 50 cubicles in a shed on the out-farm, where the heifers stay for the winter. Shane used to make all round-bale silage in the past but a new silage slab means he is making pit silage and drawing it back from the out-farm.
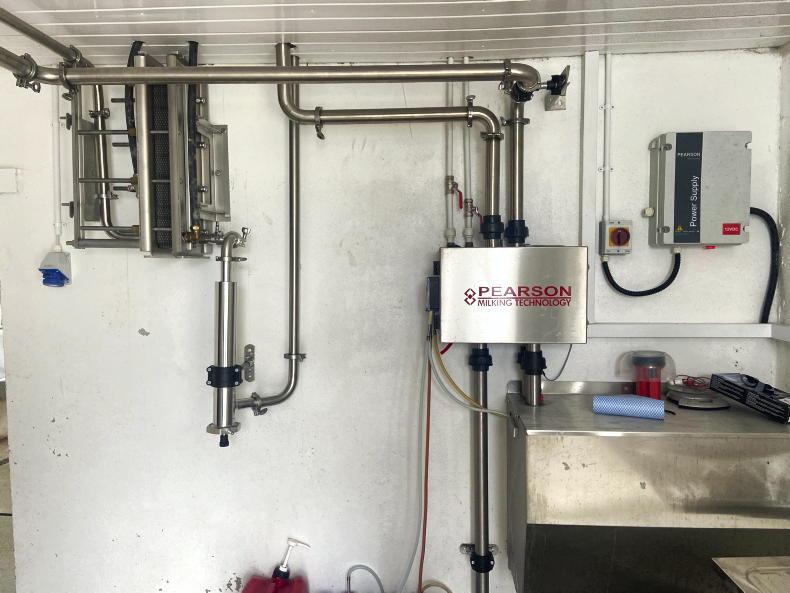
The dairy is finished to a high level.
The integration of the cubicles into the existing shed on the home farm has been excellent.
A small flow channel links up the new tank with the existing tank. The building work was completed by Ray Kelly, whom Shane and Brenda have nothing but good things to say about. Shane helped him throughout with the concrete and steel work. Four new automatic scrapers were installed to keep passageways clean.
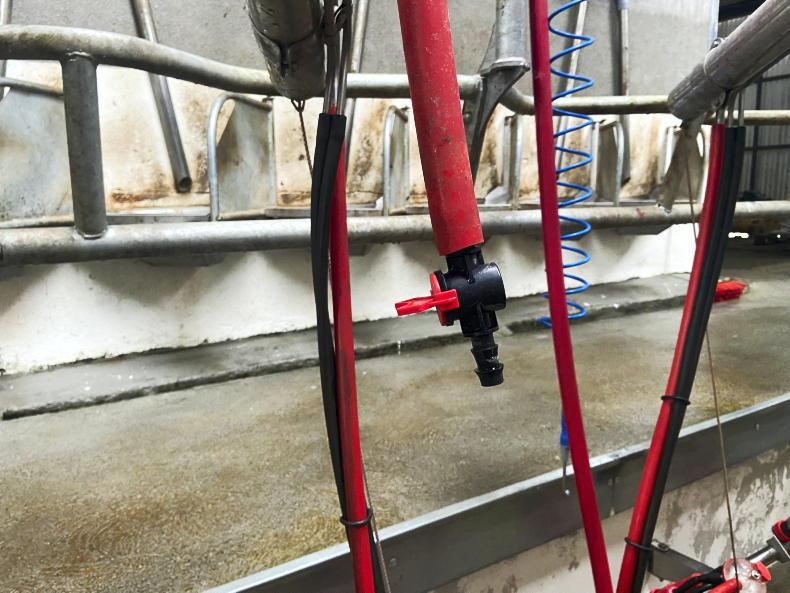
Vacuum line to plug in dump bucket.
A new 14-unit Pearson parlour was installed by local dealer Jarlath Colleran. Shane was humming and hawing about how many units to install but, in the end, he settled for 14.
A high level of technology is employed, with automatic cluster removers, variable speed vacuum pump, milk meters, automatic meal feeders and an automatic wash system.
A zig-zag rump rail and angled meal trough means that the cows line up well, even with nearly all heifers in the herd this year. The plant is at two foot six inch centres, with cow stands and pit 6ft wide. As is the norm with Pearson parlours, the parlour came factory-assembled so all that needed to be done was to fix the four stanchions in concrete and bolt the horizontal supports on to the walls.
Even the washdown hoses were installed on the plant at the factory.
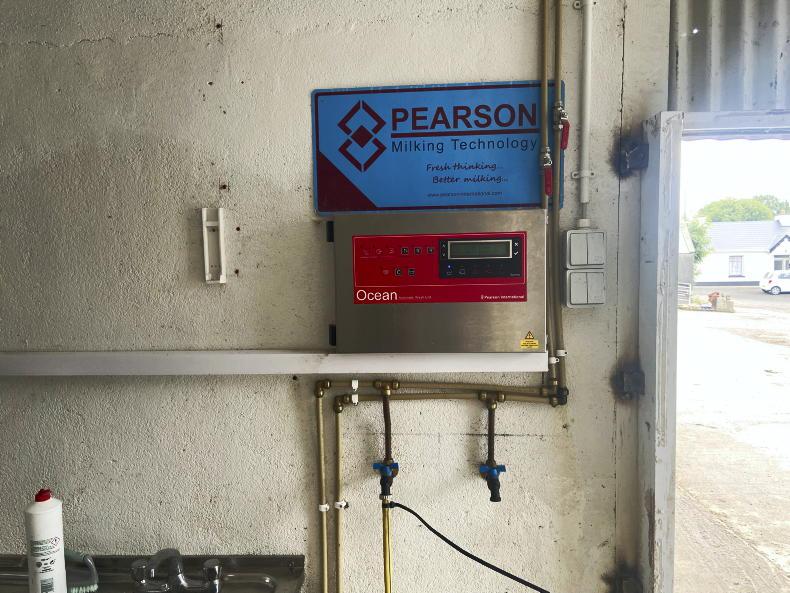
Automatic wash unit on the Hughes's farm.
Shane decided against installing a dump line but has two dump buckets that plug into the vacuum line when milking a cow whose milk is being dumped.
A dropper from the vacuum line is placed in between every second unit. This means that a cow with mastitis is not being milked with a cluster that is potentially going to be placed on a clean cow next. It’s also quicker to use as there are no hoses to be changed in order to milk the dump cow.
“The plant can be upgraded with extra technology at any time in the future without changing what I already have, which was a big attraction of Pearson for me. I don’t have feed to yield but it’s something I would consider in the future.
“Generally, the cows are on a flat rate but I manually increase the feed to the higher yielders by pressing a button on the unit which will just feed that cow,” Shane says.

Individual feeders can be upgraded to feed to yield in time.
He says the milk meters are very useful for picking up any sick or problem cows as they will generally be back in milk. A few cases of pneumonia back in spring were detected early by monitoring the yields.
All the cows are Holstein Friesian and were purchased from three herds with help from Bobby Franks from the IHFA.
Liners and milk pipes are all red silicone and Shane opted for lightweight plastic shells, which are much lighter than the traditional stainless steel shells and are more pleasant to handle on cold days, he says. Front and back air gates can be operated from anywhere in the pit.
Milk quality is impressive so far with SCC averaging 50,000 to 70,000 cells/ml and TBC averaging 5,000 to 8,000 cfu/ml since they started milking.

Special Pearson dump bucket and milking unit.
All cows are wiped and stripped before clusters are attached. Shane and Brenda do 90% of the milkings together, with Brenda doing it on her own during the busy days when Shane is away at silage.
Jarlath Colleran got his own electrician to do the wiring for the new parlour, meaning Shane had very few people to deal with when the parlour was being constructed. An 8t top-fill meal bin was purchased off Condon Engineering. Shane says this is handy as if he ever runs out of meal it can be filled from the bucket of the loader.
Overall, the Hughes family are delighted with their investments and decision to go into dairy farming.
The sale of the suckler cows and cattle helped to purchase the dairy stock and a 10-year loan was taken out to part-fund the parlour and building work.
In terms of just the milking facilities, the plant cost €5,936 excluding VAT per unit including full meal feeding system and all stall work.

The top fill meal bin holds 8t.
A new 9,600-litre Packo bulk tank was installed at a cost of €23,562 excluding VAT.
A further €37,000 was spent between building work, digging tanks, slats, etc, for the milking parlour and collecting yard bringing the total spend to just over €143,000 for the 14-unit milking facility.
A TAMS grant was claimed and because Shane and Brenda are in a farm partnership, the investment ceiling was increased.
One area that Shane is bothered about is the amount of water being collected daily between washing the plant and cleaning the floors and yard area. He calculates that there are about 1,600 gallons of soiled water being gathered daily but is not sure on how this can be reduced without compromising on hygiene.
The parlour and milking facilities are looking spotless and you can see the pride that the family takes in producing quality milk.
SHARING OPTIONS: