Diesel engines have come on in leaps and bounds over the years when it comes to efficiencies and emissions. The latest Stage V emission standards have delivered a 97% reduction in NOx emissions since 1996 and a 98% reduction in particulates. Between 2010 and 2020, JCB reduced its CO2 emissions by 50% as a result of cleaner-burning engines. But, in order to get to net zero, we as an industry need to do better.
In order to meet the ambitious goal set by the European Commission of carbon neutrality by 2050 and a 55% overall reduction in greenhouse gas (GHG) emissions by 2030 the reliance on fossil fuels will need to be greatly reduced. By now most large machinery manufacturers have got to work in some form or another to develop an alternative solution to diesel-fuelled combustion engines.

JCB demonstrated its hydrogen powered Fastrac refuller tractor and hydrogen Loadall.
JCB has been one of the first horses out of the starting gate with the development of a hydrogen gas-powered combustion engine, one of the world’s first. Since the production of the first prototype engine in 2020, more than 50 units have rolled off the line at the firm’s Power Systems factory in Derbyshire, UK.
Electric
While a number of manufacturers such as those in the compact loader market now offer smaller machines in electric form, the option never tends to go beyond this point into the larger more demanding machines. The reason for this is simple – battery power doesn’t suit these categories of machines as cost, run time, charge time, weight and the physical space required to house the battery(s) are all seen as limiting factors.

While the bottom end of the engine remains largely unchanged, the major changes to suit the combustion of hydrogen gas combustion is within the top end.
JCB currently offers seven battery powered machines including a compact telehandler, mini digger, mini-tracked dumper and an electric scissor lift.
In order to achieve net zero, JCB is of the firm belief that there isn’t one true alternative to fossil fuels but instead a number of solutions depending on the machine and market. “Just because electric works and is already available doesn’t mean it should or can be used for every application. We’re not a car, we’re a machine and there’s a big difference between the two. So, it’s important we use the right technologies for the right application,” stated Tim Burnhope, JCB chief innovation and growth officer.
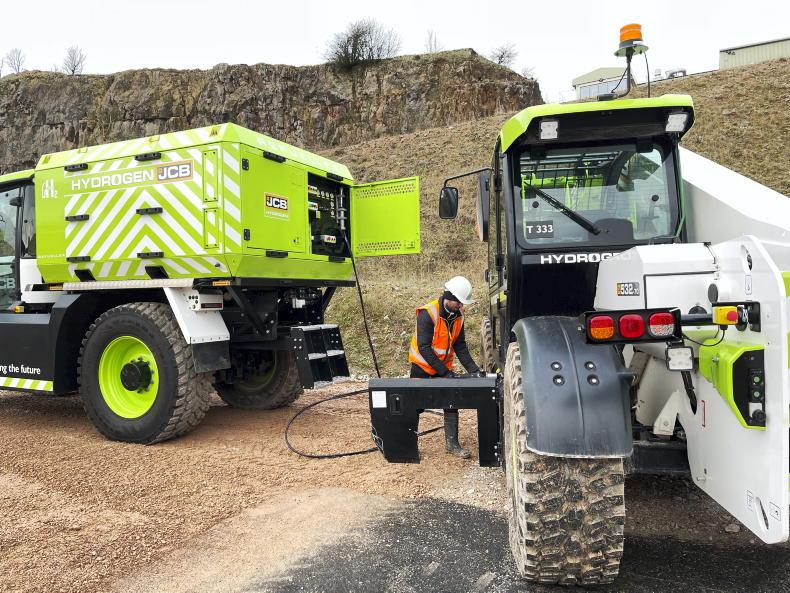
The hydrogen gas is decanted from the tube trailer and within minutes the machine’s storage tanks are full.
“Take for example our compact 525-60E loader. It’s got a 24kWh battery split into five separate packs and a total battery cost of around £10,000 (€11,300). The total purchase cost is 1.9 times more than the diesel counterpart and the weight is pretty much the same. But, scaling up remains the issue.
“An electric Fastrac with a 1,000kWh output capable of working 16 hours daily would require 200 of these battery packs causing the machine to cost around £400,000 (€453,500), up to 4.3 times more than the existing diesel variant and at a weight in excess of 10,000kg.”
Why hydrogen?
New Holland has very much settled its focuses on methane gas combustion engines with its T6 methane CNG tractor available on the market and T7 LNG tractor in final stages of development. JCB on the other hand has focused its attentions on a hydrogen-fuelled future.

A JCB Ecomax diesel engine (left) beside the hydrogen combustion engine (right).
JCB’s goal is a complete net zero solution which it believes can be achieved from green hydrogen (hydrogen produced in a renewable manner). Once hydrogen fuel is combusted or the chemical reaction takes place within the fuel cell, the by-product is steam/water, unlike the burning of methane which produces CO2.
This belief in hydrogen has laid the foundations for JCB’s Road to Zero project, a project JCB chair Lord Bamford personally feels strongly about.
Hydrogen fuel cells
Having initially looked at a number of other alternative fuels, hydrogen was (and remains) the most attractive solution according to JCB. The starting point was the use of a Nissan-supplied fuel cell which the company fitted to a 20t X series digger in 2019.
“It was here we started to understand the complex challenge of integrating a fuel cell into a piece of construction equipment. We soon realised that fuel cells do not like transient load. Slewing and lowering the dipper arm doesn’t demand much energy. It’s when lifting and digging that the demand is placed on the fuel cell. To combat this continuous spike in load, a battery store was needed for the sudden release of energy,” Tim said.

In terms of hydrogen capacity, JCB is quoting run times similar to a diesel Loadall.
“For longevity of a fuel cell it needs to be operated in a clean environment to prevent internal membranes clogging up. Essentially, fuel cells are too complex and too expensive for the market we wanted to serve.”
According to Tim, a fuel cell machine would cost the end user roughly three times the price of its diesel counterpart with considerably higher running cost. The deionised coolant alone needed for one excavator’s fuel cell would cost over £2,000 (€2,268). Bearing all these factors in mind, JCB said it has concluded the exploration of hydrogen fuel cell technology as an alternative solution.
Hydrogen gas
Ruling out the use of fuel cells for construction and agricultural applications, the firm set itself the challenge in July 2020 of developing a hydrogen-fuelled combustion engine that would operate identical or better than a diesel engine and refuel in a similar manner. By December 2020 a hydrogen-powered engine was running. To achieve the hydrogen combustion engine JCB said it wasn’t a matter of modifying a diesel engine but instead having to go back to first principles engineering.

Aside from cost, fuel cell technology cant handle the transient load cycles very well.
“We wouldn’t take diesel and put it in petrol and expect it to work OK. But that’s the approach a lot of others have taken,” said Tim, believing this to be the downfall of other companies to date.
Two years on, development is now complete with over 50 engines manufactured so far on the existing engine production line in Derbyshire. The result is a patented zero CO2 hydrogen gas-fuelled combustion engine.
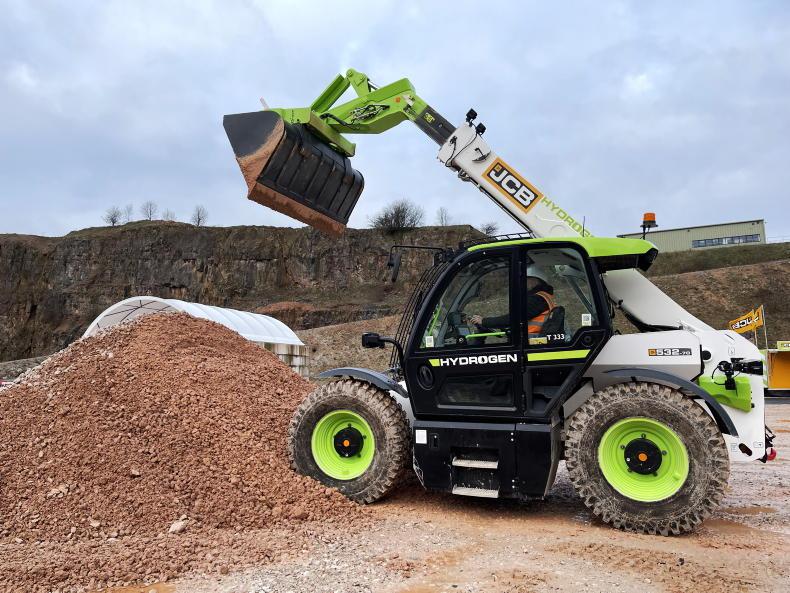
Compared with diesel, both power and torque remain unchanged with the hydrogen engine.
The physical makeup of the engine isn’t really all that different to a traditional diesel engine. The induction system, pistons and cylinder head along with the addition of spark plugs are the major differences. Otherwise, the bottom end of the engine remains largely unchanged.

The refuelling process is clean and only takes a matter of minutes.
In a nutshell, the hydrogen gas and air mixture is injected into the chamber via common rail injection at a lowered pressure. A variable geometry turbo forces air into the cylinders before combustion. Then hydrogen-specific spark plugs ignite the mixture at a lower temperature providing a clean CO2-free burn, according to Ryan Ballard, powertrain engineering director at JCB.
Key to the combustion process is a lean mix of fuel with a hydrogen to air ratio of 1:100. Combustion takes place at a much lower temperature due to the fuel to air mix. The other main difference to the engine is the steam management system which keeps water vapour produced from the combustion cycle away from the engine. A special oil that doesn’t emulsify in water is used. Although the current oil being used is derived from fossil fuels, JCB has said it is looking at ‘green’ fossil fuel-free oils for the future.

JCB recently unveiled its very own designed and built mobile refuelling bowser to take the fuel to the machines.
With 97% of JCB’s machines refuelled via diesel bowers, it was important that the hydrogen gas engine would be done in a similar fashion. In order to do this JCB has developed a hydrogen bowser with capacity to refuel 16 backhoe loaders. The hydrogen gas is decanted from the tube trailer and within minutes the machine’s storage tanks are full.
Interestingly, hydrogen combustion engines are not a new innovation – it was more so reliability and efficiency that proved the issue. Frenchman Francois Isaac de Rivas invented a hydrogen fuelled spark ignition internal combustion engine in 1807.
What is hydrogen fuel?
Hydrogen is a manmade fuel that produces zero carbon when spent. Essentially, it is created when water (H20) molecules are split, a process that can also be carbon-free if carried out using a renewable process. While hydrogen is the most abundant chemical substance on earth, in the form of water and organic matter, it remains scarce in pure form which is how it is required when used as a fuel.
Once hydrogen is consumed in a fuel cell, the only byproduct is water. When combusted it produces steam/water and a small level of NOx. Although hydrogen gas has a low density it has a high energy density. One kilogram of hydrogen has about the same energy as 2.8kg of diesel. Aside from storage, these traits leave it as attractive as a fuel option. The downside is that hydrogen requires energy to produce. Hydrogen can be produced through several methods including natural gas reforming, electrolysis, as well as solar-driven and biological processes.
Hydrogen fuel is classified as either green or blue hydrogen. Green hydrogen has no associated C02 emission and is formed using a renewable process ie through electrolysis using renewable electricity. Blue hydrogen is derived from thermal processes such as natural gas reforming, which emits C02.

The hydrogen bowser can be transported either on the back of a modified Fastrac tractor or on a trailer.
Early hydrogen developments tended to be in the form of a fuel cell which is essentially a chemical reaction between hydrogen and oxygen. This tends to be a costly and lazy process that requires substantial cooling and a clean environment.
Test units
Given that the hydrogen engine physically resembles a diesel engine, fitment to existing equipment ranges largely the same.
“With the fuel cell project, it took the team six months to configure the fuel cell, six weeks to do the installation and a further six weeks to get the electronics to work.
“The hydrogen combustion engine was sent over the assembly line on Friday and was ready for testing in the backhoe the following Thursday. This is what makes it the real winner,” Tim said. A hydrogen engine was also fitted to a 532.70 Loadall and 3CX backhoe for testing and evaluation. The main challenge surrounding hydrogen is storage. Instead of one large traditional fuel tank, hydrogen gas is stored in separate interconnected tanks. This is in order to keep wall thickness to a minimum. Each tank is wrapped in carbon fibre for further strength. According to JCB, its tanks are designed to withstand the impact of a bullet.
The hydrogen gas is stored in a liquid state in these tanks at 350 bar and – 250°C. Hydrogen is moved from the refueller tank at 450 bar to the machine by means of pressure differential. Fuel is then delivered to the engine at 20 bar.
JCB is keen to stress the similarities between driving a hydrogen-powered Loadall and the traditional diesel variant in terms of power, torque and response. Although, slow to give definite run time figures JCB said run time using the current tank setup is very similar to that of the diesel-powered Loadall.
Fuel infrastructure
With the drive towards alternative fuels, whether it’s methane or hydrogen there’s always going to be a chicken or egg scenario – which comes first the infrastructure or the fuel? JCB understands this but feel someone has to make the initial move. Now that it has the engine solution, sourcing green hydrogen is the next biggest challenge, the firm said.
“The hydrogen industry in the UK is now advancing faster than before. There were only three or four projects working on hydrogen production in the UK less than three years ago. Now there are over 105 active programmes to manufacture hydrogen,” Tim stated.
For now, JCB is continuing with further testing of its hydrogen engines both in industry and on its test rigs inside the powertrain factory. It hopes to start full commercial production as early as this year (2023).
Diesel engines have come on in leaps and bounds over the years when it comes to efficiencies and emissions. The latest Stage V emission standards have delivered a 97% reduction in NOx emissions since 1996 and a 98% reduction in particulates. Between 2010 and 2020, JCB reduced its CO2 emissions by 50% as a result of cleaner-burning engines. But, in order to get to net zero, we as an industry need to do better.
In order to meet the ambitious goal set by the European Commission of carbon neutrality by 2050 and a 55% overall reduction in greenhouse gas (GHG) emissions by 2030 the reliance on fossil fuels will need to be greatly reduced. By now most large machinery manufacturers have got to work in some form or another to develop an alternative solution to diesel-fuelled combustion engines.

JCB demonstrated its hydrogen powered Fastrac refuller tractor and hydrogen Loadall.
JCB has been one of the first horses out of the starting gate with the development of a hydrogen gas-powered combustion engine, one of the world’s first. Since the production of the first prototype engine in 2020, more than 50 units have rolled off the line at the firm’s Power Systems factory in Derbyshire, UK.
Electric
While a number of manufacturers such as those in the compact loader market now offer smaller machines in electric form, the option never tends to go beyond this point into the larger more demanding machines. The reason for this is simple – battery power doesn’t suit these categories of machines as cost, run time, charge time, weight and the physical space required to house the battery(s) are all seen as limiting factors.

While the bottom end of the engine remains largely unchanged, the major changes to suit the combustion of hydrogen gas combustion is within the top end.
JCB currently offers seven battery powered machines including a compact telehandler, mini digger, mini-tracked dumper and an electric scissor lift.
In order to achieve net zero, JCB is of the firm belief that there isn’t one true alternative to fossil fuels but instead a number of solutions depending on the machine and market. “Just because electric works and is already available doesn’t mean it should or can be used for every application. We’re not a car, we’re a machine and there’s a big difference between the two. So, it’s important we use the right technologies for the right application,” stated Tim Burnhope, JCB chief innovation and growth officer.
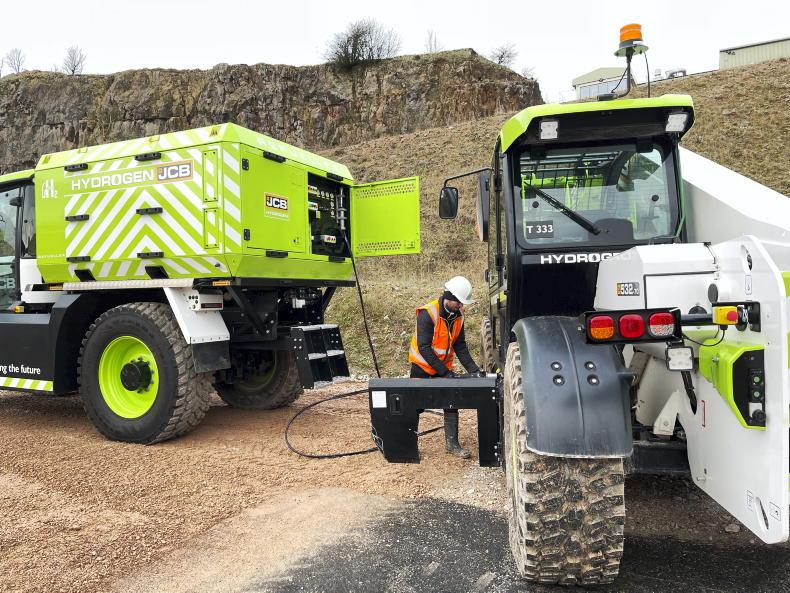
The hydrogen gas is decanted from the tube trailer and within minutes the machine’s storage tanks are full.
“Take for example our compact 525-60E loader. It’s got a 24kWh battery split into five separate packs and a total battery cost of around £10,000 (€11,300). The total purchase cost is 1.9 times more than the diesel counterpart and the weight is pretty much the same. But, scaling up remains the issue.
“An electric Fastrac with a 1,000kWh output capable of working 16 hours daily would require 200 of these battery packs causing the machine to cost around £400,000 (€453,500), up to 4.3 times more than the existing diesel variant and at a weight in excess of 10,000kg.”
Why hydrogen?
New Holland has very much settled its focuses on methane gas combustion engines with its T6 methane CNG tractor available on the market and T7 LNG tractor in final stages of development. JCB on the other hand has focused its attentions on a hydrogen-fuelled future.

A JCB Ecomax diesel engine (left) beside the hydrogen combustion engine (right).
JCB’s goal is a complete net zero solution which it believes can be achieved from green hydrogen (hydrogen produced in a renewable manner). Once hydrogen fuel is combusted or the chemical reaction takes place within the fuel cell, the by-product is steam/water, unlike the burning of methane which produces CO2.
This belief in hydrogen has laid the foundations for JCB’s Road to Zero project, a project JCB chair Lord Bamford personally feels strongly about.
Hydrogen fuel cells
Having initially looked at a number of other alternative fuels, hydrogen was (and remains) the most attractive solution according to JCB. The starting point was the use of a Nissan-supplied fuel cell which the company fitted to a 20t X series digger in 2019.
“It was here we started to understand the complex challenge of integrating a fuel cell into a piece of construction equipment. We soon realised that fuel cells do not like transient load. Slewing and lowering the dipper arm doesn’t demand much energy. It’s when lifting and digging that the demand is placed on the fuel cell. To combat this continuous spike in load, a battery store was needed for the sudden release of energy,” Tim said.

In terms of hydrogen capacity, JCB is quoting run times similar to a diesel Loadall.
“For longevity of a fuel cell it needs to be operated in a clean environment to prevent internal membranes clogging up. Essentially, fuel cells are too complex and too expensive for the market we wanted to serve.”
According to Tim, a fuel cell machine would cost the end user roughly three times the price of its diesel counterpart with considerably higher running cost. The deionised coolant alone needed for one excavator’s fuel cell would cost over £2,000 (€2,268). Bearing all these factors in mind, JCB said it has concluded the exploration of hydrogen fuel cell technology as an alternative solution.
Hydrogen gas
Ruling out the use of fuel cells for construction and agricultural applications, the firm set itself the challenge in July 2020 of developing a hydrogen-fuelled combustion engine that would operate identical or better than a diesel engine and refuel in a similar manner. By December 2020 a hydrogen-powered engine was running. To achieve the hydrogen combustion engine JCB said it wasn’t a matter of modifying a diesel engine but instead having to go back to first principles engineering.

Aside from cost, fuel cell technology cant handle the transient load cycles very well.
“We wouldn’t take diesel and put it in petrol and expect it to work OK. But that’s the approach a lot of others have taken,” said Tim, believing this to be the downfall of other companies to date.
Two years on, development is now complete with over 50 engines manufactured so far on the existing engine production line in Derbyshire. The result is a patented zero CO2 hydrogen gas-fuelled combustion engine.
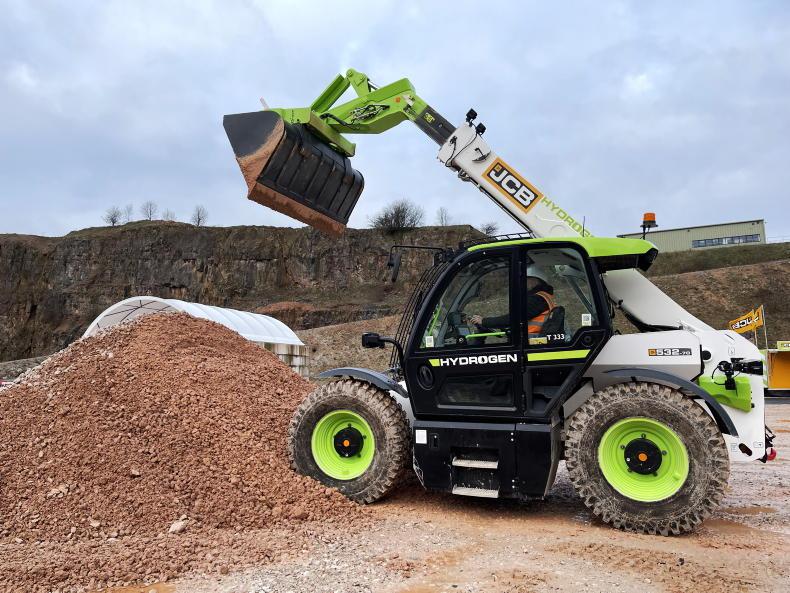
Compared with diesel, both power and torque remain unchanged with the hydrogen engine.
The physical makeup of the engine isn’t really all that different to a traditional diesel engine. The induction system, pistons and cylinder head along with the addition of spark plugs are the major differences. Otherwise, the bottom end of the engine remains largely unchanged.

The refuelling process is clean and only takes a matter of minutes.
In a nutshell, the hydrogen gas and air mixture is injected into the chamber via common rail injection at a lowered pressure. A variable geometry turbo forces air into the cylinders before combustion. Then hydrogen-specific spark plugs ignite the mixture at a lower temperature providing a clean CO2-free burn, according to Ryan Ballard, powertrain engineering director at JCB.
Key to the combustion process is a lean mix of fuel with a hydrogen to air ratio of 1:100. Combustion takes place at a much lower temperature due to the fuel to air mix. The other main difference to the engine is the steam management system which keeps water vapour produced from the combustion cycle away from the engine. A special oil that doesn’t emulsify in water is used. Although the current oil being used is derived from fossil fuels, JCB has said it is looking at ‘green’ fossil fuel-free oils for the future.

JCB recently unveiled its very own designed and built mobile refuelling bowser to take the fuel to the machines.
With 97% of JCB’s machines refuelled via diesel bowers, it was important that the hydrogen gas engine would be done in a similar fashion. In order to do this JCB has developed a hydrogen bowser with capacity to refuel 16 backhoe loaders. The hydrogen gas is decanted from the tube trailer and within minutes the machine’s storage tanks are full.
Interestingly, hydrogen combustion engines are not a new innovation – it was more so reliability and efficiency that proved the issue. Frenchman Francois Isaac de Rivas invented a hydrogen fuelled spark ignition internal combustion engine in 1807.
What is hydrogen fuel?
Hydrogen is a manmade fuel that produces zero carbon when spent. Essentially, it is created when water (H20) molecules are split, a process that can also be carbon-free if carried out using a renewable process. While hydrogen is the most abundant chemical substance on earth, in the form of water and organic matter, it remains scarce in pure form which is how it is required when used as a fuel.
Once hydrogen is consumed in a fuel cell, the only byproduct is water. When combusted it produces steam/water and a small level of NOx. Although hydrogen gas has a low density it has a high energy density. One kilogram of hydrogen has about the same energy as 2.8kg of diesel. Aside from storage, these traits leave it as attractive as a fuel option. The downside is that hydrogen requires energy to produce. Hydrogen can be produced through several methods including natural gas reforming, electrolysis, as well as solar-driven and biological processes.
Hydrogen fuel is classified as either green or blue hydrogen. Green hydrogen has no associated C02 emission and is formed using a renewable process ie through electrolysis using renewable electricity. Blue hydrogen is derived from thermal processes such as natural gas reforming, which emits C02.

The hydrogen bowser can be transported either on the back of a modified Fastrac tractor or on a trailer.
Early hydrogen developments tended to be in the form of a fuel cell which is essentially a chemical reaction between hydrogen and oxygen. This tends to be a costly and lazy process that requires substantial cooling and a clean environment.
Test units
Given that the hydrogen engine physically resembles a diesel engine, fitment to existing equipment ranges largely the same.
“With the fuel cell project, it took the team six months to configure the fuel cell, six weeks to do the installation and a further six weeks to get the electronics to work.
“The hydrogen combustion engine was sent over the assembly line on Friday and was ready for testing in the backhoe the following Thursday. This is what makes it the real winner,” Tim said. A hydrogen engine was also fitted to a 532.70 Loadall and 3CX backhoe for testing and evaluation. The main challenge surrounding hydrogen is storage. Instead of one large traditional fuel tank, hydrogen gas is stored in separate interconnected tanks. This is in order to keep wall thickness to a minimum. Each tank is wrapped in carbon fibre for further strength. According to JCB, its tanks are designed to withstand the impact of a bullet.
The hydrogen gas is stored in a liquid state in these tanks at 350 bar and – 250°C. Hydrogen is moved from the refueller tank at 450 bar to the machine by means of pressure differential. Fuel is then delivered to the engine at 20 bar.
JCB is keen to stress the similarities between driving a hydrogen-powered Loadall and the traditional diesel variant in terms of power, torque and response. Although, slow to give definite run time figures JCB said run time using the current tank setup is very similar to that of the diesel-powered Loadall.
Fuel infrastructure
With the drive towards alternative fuels, whether it’s methane or hydrogen there’s always going to be a chicken or egg scenario – which comes first the infrastructure or the fuel? JCB understands this but feel someone has to make the initial move. Now that it has the engine solution, sourcing green hydrogen is the next biggest challenge, the firm said.
“The hydrogen industry in the UK is now advancing faster than before. There were only three or four projects working on hydrogen production in the UK less than three years ago. Now there are over 105 active programmes to manufacture hydrogen,” Tim stated.
For now, JCB is continuing with further testing of its hydrogen engines both in industry and on its test rigs inside the powertrain factory. It hopes to start full commercial production as early as this year (2023).
SHARING OPTIONS: