Based in Ballycroy, Co Mayo, Padraig Grealis began his agricultural contracting career in 1989 with a 43in Gyro single-chop harvester. Since then, the contracting business has grown organically and is now split evenly between agricultural work, plant hire and construction work.
Today, Padraig is joined full time by his sons, Raymond and Colm. On the side, the family keeps a herd of spring and autumn-calving suckler cows.
Why Massey Ferguson?
“I started out first with a second-hand Welger RP12S in 1991. The Welger brand best suited our conditions. They were lighter and had a better intake than the competitors. We started out too with a RoCo Engineering wrapper and from there onto a single-dispenser McHale.
“In the years that followed, I had RP200s, 202s, 220s, 235s and 245s, the latter being branded Lely Welger. They got progressively better as the years passed. The drop floor which was first added to the RP235 was probably the single biggest leap forward. By the early 2000s I was averaging 10,000 bales annually with one baler,” said Padraig.
Between the years of 2012 and 2013, the team decided to put out a second baler, a second RP245 and upgrade to a Tanco 1400 V wrapper. Typically, balers were replaced between 30,000 and 40,000 bales. At the time, other Lely machines in the fleet included a front- and side-mounted set of mowers, a rake and a power harrow, all of which were referred to as good machines.
Up until 2021, the Grealis’ continued to run two RP245 balers, before trading the older RP245 for an RB 3130F Protec combination baler wrapper from Johnston Equipment in Co Longford. At this point, Lely Welger brand had been incorporated by AGCO under the Massey Ferguson brand.
Raymond said: “We deliberated buying a combi unit for almost two years before biting the bullet. Rising costs around labour, machinery and fuel triggered the idea. But, working quite a lot of marginal land, we thought it would suit 30% to 40% of the jobs.
“Having briefly looked at other brands, the Protec stood out, helped by the fact it was a baler that we knew well. It seemed a better balanced machine over some of the others and the way in which the wrapping ring folded left it almost as manoeuvrable as a standard machine,” he pointed out.
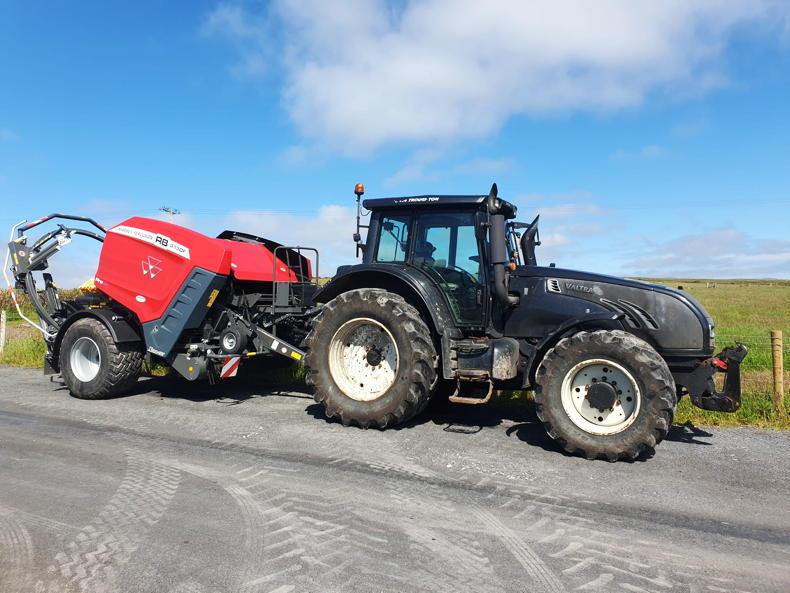
The RB 3130F Protec combination baler is now run alongside a Lely Welger RP245 and Tanco 1400V wrapper.
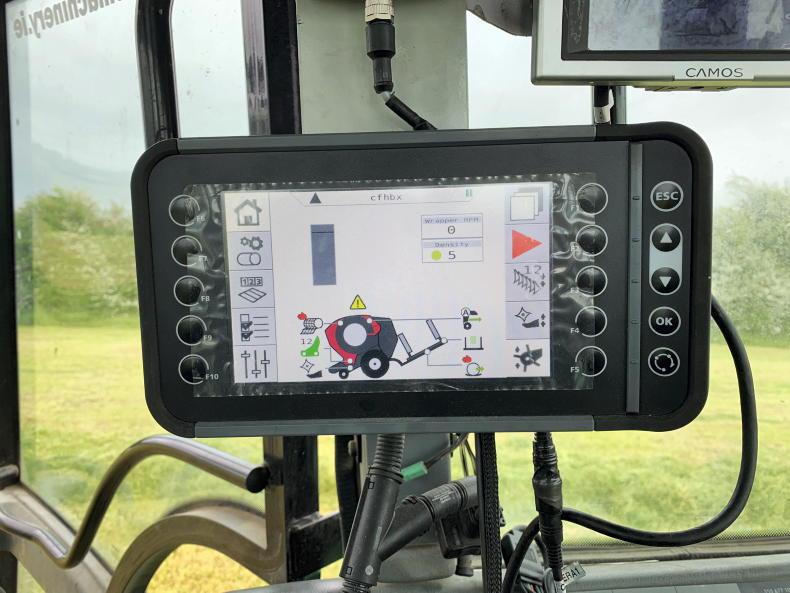
The E-Link Pro touch screen terminal is easily worked.

The wrapping cycle takes around 25 seconds to apply seven layers of film, Raymond said.
Pickup and chopping unit
“After 15,000 bales I’ve replaced one tine. The camless pickup has been a big saving in labour. At the start of every season we traditionally replaced all pickup cam bearings, which is now one job less. When Lely Welger initially went camless, we found a small issue with short grass building up in front of the rotor, but that was quickly rectified on the next baler. When rakes first arrived on the scene, we never had an issue lifting three 10ft rows of grass where others struggled. This has always been a major attraction to the brand, Raymond stated.
The RB 3130F Protec is fitted with a five-tine-bar camless pickup. At either end of the 2.25m pickup are large 25cm diameter feeding augers designed to direct the crop into the rotor.
The Grealis’ opted for the Xtracut 17 knife chopping unit over the 25 knife option. The knife bank is essentially split into two, a bank of eight knives and a bank of nine knives. The shortest chop length is achieved when both banks are engaged together.
Raymond runs either eight or nine knives at a time and alternates to a fresh bank each day. After two days or 1,000 bales all knives are removed and sharpened using a Göweil knife sharpener.
“On average, we have found that blunt knives increase fuel consumption by up to 20/hr. Based on current diesel prices, this could be a saving of up to €200 per day. So it pays to keep knives sharp,” explained Raymond.
Massey use a two-stage drop anti-blockage system. Stage one is Hydroflexcontrol system, whereby the floor automatically lowers slightly to absorb minor blockages and allow them pass through. If this doesn’t suffice and a complete blockage occurs then the floor can be hydraulically lowered.
Inside the bale chamber are 18 Powergrip rollers, each manufactured from a seamless solid tube, with 10 ribs on each. Rollers have never proved an issue for the lads.
“In all our time spent with Lely Welgers, we’ve only replaced one roller. After 40,000 bales, our current RP245 needs a roller bearing replaced and a new set of chains, which is nothing considering the work it has done,” Raymond said.
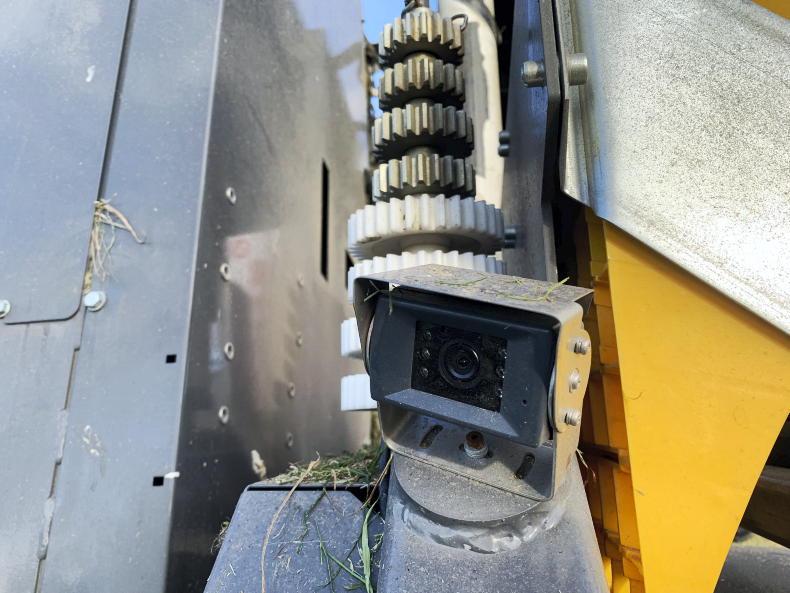
Any issues with the wrapping cycle can be quickly spotted from the cab, thanks to the camera.
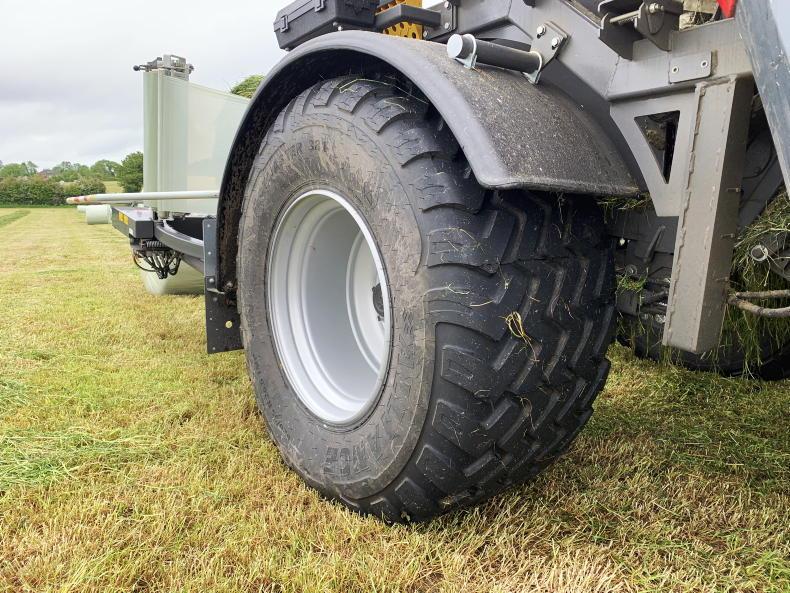
The RB 3130F Protec is fitted with 620/55 R26.5 tyres.
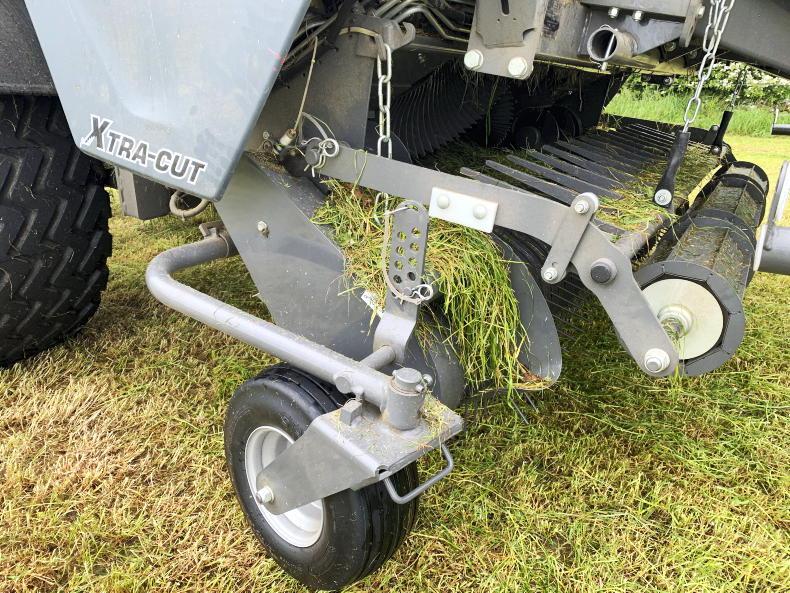
The RB 3130F Protec is fitted with a 2.25m five-tine-bar, camless pickup.
How has it performed?
Since its arrival in June 2021, the RB 3130F Protec has surpassed its 15,000 bale, trouble free. Being a load-sensing machine, the only compatible tractor in the yard of predominately Valtra tractors was a T202.
“It was an easy machine to get to grips with. Load-sensing is a great comfort and easy on the tractor. After our first year, we were surprised with how well the baler travelled, even in marginal areas. It now does at least 50% of all baling, much more than we anticipated. Although helped by the 620mm tyres, once a conscious effort is made to keep weight to a minimum by dropping bales off on approach to wet areas then it will travel as well as a standard baler,” Raymond said.
“We’ve always been of the belief that the latched chamber door makes dense, firm bales. Once it’s closed, there’s no chance it can creep open. The only difference with its chamber compared to the RP245 is that one of the floor rollers has been added to the door. This allows it to lift out of the way when the bale is transferring to the wrapping table, meaning only one roller bears the weight of the bale and eliminates bridging. The transfer system is smooth and reliable, regardless if it’s a hill or a side slope you’re on. The wrapping cycle takes between 23 and 24 seconds. I tend to run the baler in full auto mode, with the exception of releasing bales from the wrapping table manually. One thing about the transfer system is that chaff and debris builds up quite easily and quickly around the transfer mechanism and axle. This would be one of the minor areas that would benefit from a design tweak.
“The E-Link Pro touchscreen terminal is straightforward and displays all necessary information on the home screen. There is also a camera to show the wrapper table,” concluded Raymond.
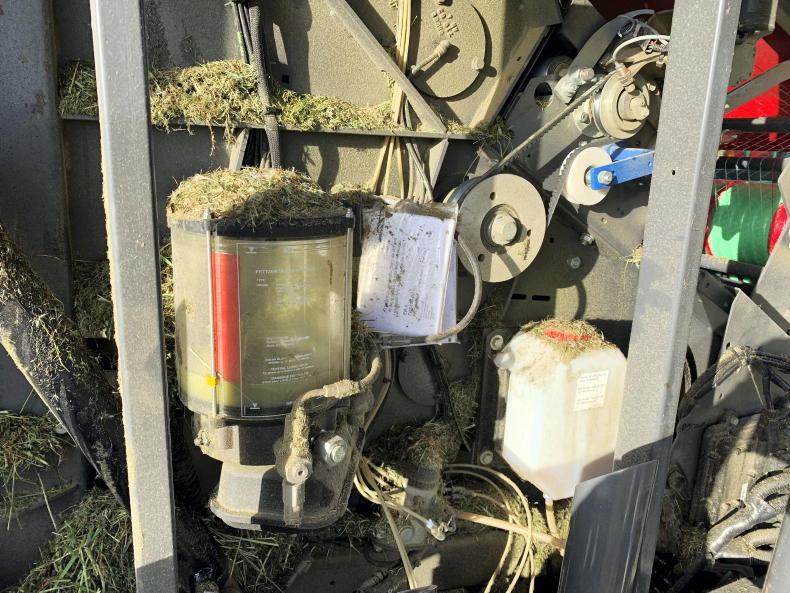
Since automatic chain lube systems have come fitted on balers, Padraig has seen a huge increase in chain lifespan.
“After 33 years of Welger, Lely Welger and now Massey Ferguson, the important part is that the after all the rebranding, the product hasn’t lost its identity. All the original reasons why I went with the brand 33 years ago remain the same today. Meanwhile, the areas needing improved were improved. Everything from performance to running costs, service and resale couldn’t be faulted. The backup we’ve had through the years has been and continues to be excellent,” said Padraig.
“It was definitely the right move. The Protec is a serious piece of kit and there are serious cost benefits to running a combination unit. Given that we work quite a bit of marginal land, I don’t think we could do without a standard baler and wrapper either,” said Raymond.

The family still runs a 2017 Lely Welger RP245 standard baler alongside the combi unit.
Weight: 5,990kg. Tyres: 620/55 R26.5 Alliance.Length: 5.9m (transport). Knives: 17-knife selectable floor (combinations; 0,8,9,17). Bale chamber: 18 rollers, (1.25m Bale diameter). Terminal: E-Link pro monitor and Isobus compatible. Pickup: 2.25m five-tine bar camless. List price: €100,000 plus VAT.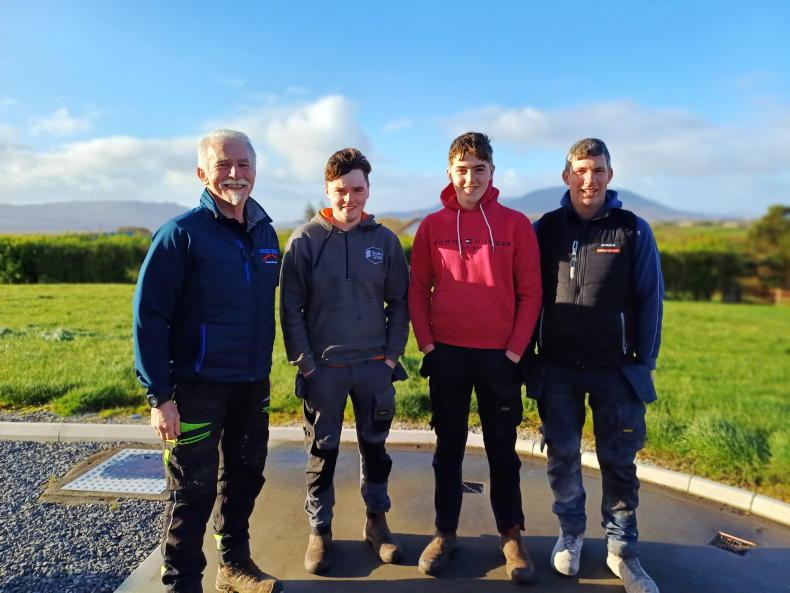
Left to right: Padraig Grealis, Sean O'Boyle, Cormac McManamon and Raymond Grealis.
Likes
Pickup and rotor intake.Weight distribution.? Dislikes
Grass and chaff builds up around axle and transfer unit.
Based in Ballycroy, Co Mayo, Padraig Grealis began his agricultural contracting career in 1989 with a 43in Gyro single-chop harvester. Since then, the contracting business has grown organically and is now split evenly between agricultural work, plant hire and construction work.
Today, Padraig is joined full time by his sons, Raymond and Colm. On the side, the family keeps a herd of spring and autumn-calving suckler cows.
Why Massey Ferguson?
“I started out first with a second-hand Welger RP12S in 1991. The Welger brand best suited our conditions. They were lighter and had a better intake than the competitors. We started out too with a RoCo Engineering wrapper and from there onto a single-dispenser McHale.
“In the years that followed, I had RP200s, 202s, 220s, 235s and 245s, the latter being branded Lely Welger. They got progressively better as the years passed. The drop floor which was first added to the RP235 was probably the single biggest leap forward. By the early 2000s I was averaging 10,000 bales annually with one baler,” said Padraig.
Between the years of 2012 and 2013, the team decided to put out a second baler, a second RP245 and upgrade to a Tanco 1400 V wrapper. Typically, balers were replaced between 30,000 and 40,000 bales. At the time, other Lely machines in the fleet included a front- and side-mounted set of mowers, a rake and a power harrow, all of which were referred to as good machines.
Up until 2021, the Grealis’ continued to run two RP245 balers, before trading the older RP245 for an RB 3130F Protec combination baler wrapper from Johnston Equipment in Co Longford. At this point, Lely Welger brand had been incorporated by AGCO under the Massey Ferguson brand.
Raymond said: “We deliberated buying a combi unit for almost two years before biting the bullet. Rising costs around labour, machinery and fuel triggered the idea. But, working quite a lot of marginal land, we thought it would suit 30% to 40% of the jobs.
“Having briefly looked at other brands, the Protec stood out, helped by the fact it was a baler that we knew well. It seemed a better balanced machine over some of the others and the way in which the wrapping ring folded left it almost as manoeuvrable as a standard machine,” he pointed out.
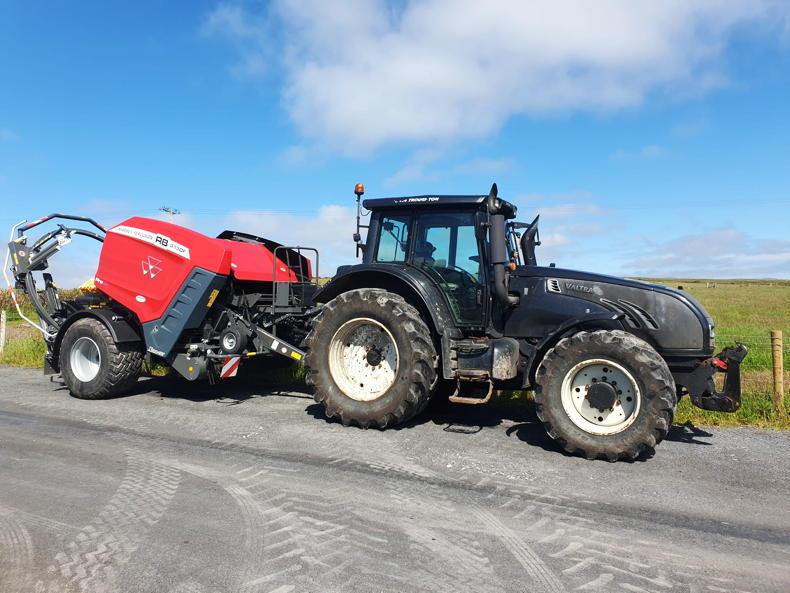
The RB 3130F Protec combination baler is now run alongside a Lely Welger RP245 and Tanco 1400V wrapper.
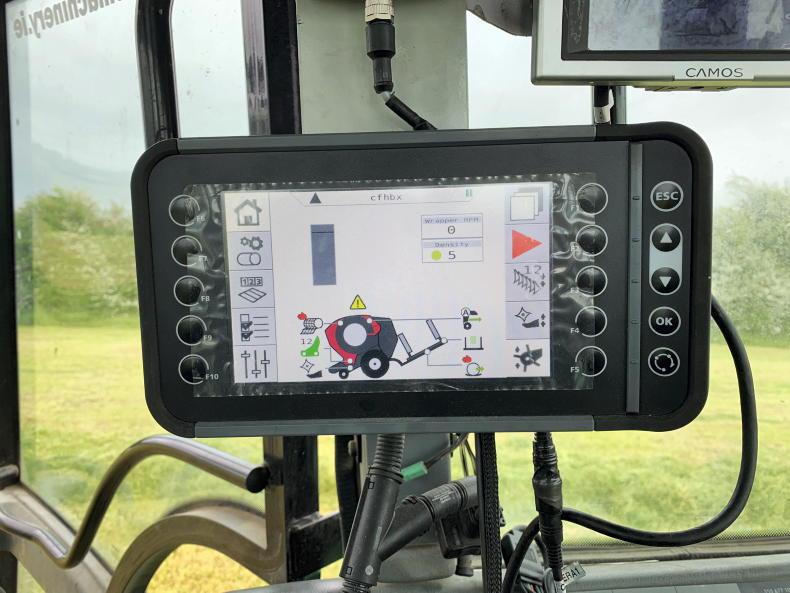
The E-Link Pro touch screen terminal is easily worked.

The wrapping cycle takes around 25 seconds to apply seven layers of film, Raymond said.
Pickup and chopping unit
“After 15,000 bales I’ve replaced one tine. The camless pickup has been a big saving in labour. At the start of every season we traditionally replaced all pickup cam bearings, which is now one job less. When Lely Welger initially went camless, we found a small issue with short grass building up in front of the rotor, but that was quickly rectified on the next baler. When rakes first arrived on the scene, we never had an issue lifting three 10ft rows of grass where others struggled. This has always been a major attraction to the brand, Raymond stated.
The RB 3130F Protec is fitted with a five-tine-bar camless pickup. At either end of the 2.25m pickup are large 25cm diameter feeding augers designed to direct the crop into the rotor.
The Grealis’ opted for the Xtracut 17 knife chopping unit over the 25 knife option. The knife bank is essentially split into two, a bank of eight knives and a bank of nine knives. The shortest chop length is achieved when both banks are engaged together.
Raymond runs either eight or nine knives at a time and alternates to a fresh bank each day. After two days or 1,000 bales all knives are removed and sharpened using a Göweil knife sharpener.
“On average, we have found that blunt knives increase fuel consumption by up to 20/hr. Based on current diesel prices, this could be a saving of up to €200 per day. So it pays to keep knives sharp,” explained Raymond.
Massey use a two-stage drop anti-blockage system. Stage one is Hydroflexcontrol system, whereby the floor automatically lowers slightly to absorb minor blockages and allow them pass through. If this doesn’t suffice and a complete blockage occurs then the floor can be hydraulically lowered.
Inside the bale chamber are 18 Powergrip rollers, each manufactured from a seamless solid tube, with 10 ribs on each. Rollers have never proved an issue for the lads.
“In all our time spent with Lely Welgers, we’ve only replaced one roller. After 40,000 bales, our current RP245 needs a roller bearing replaced and a new set of chains, which is nothing considering the work it has done,” Raymond said.
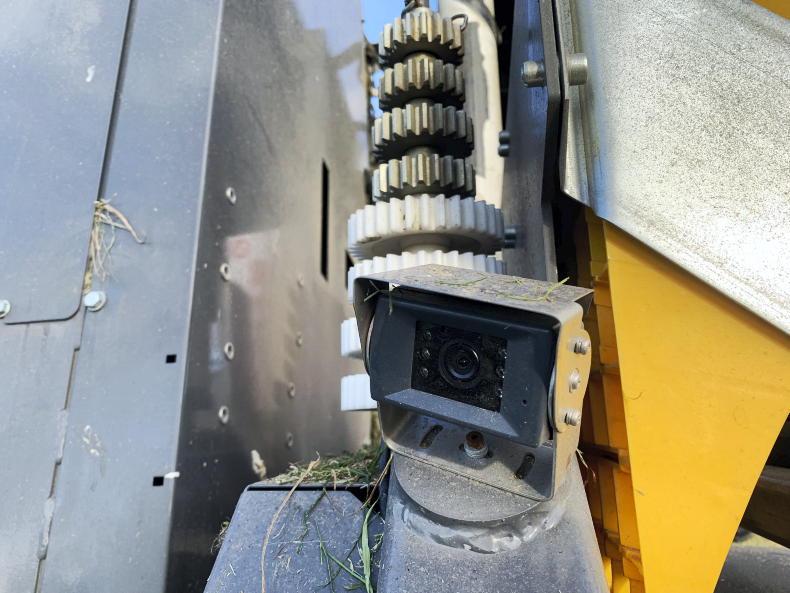
Any issues with the wrapping cycle can be quickly spotted from the cab, thanks to the camera.
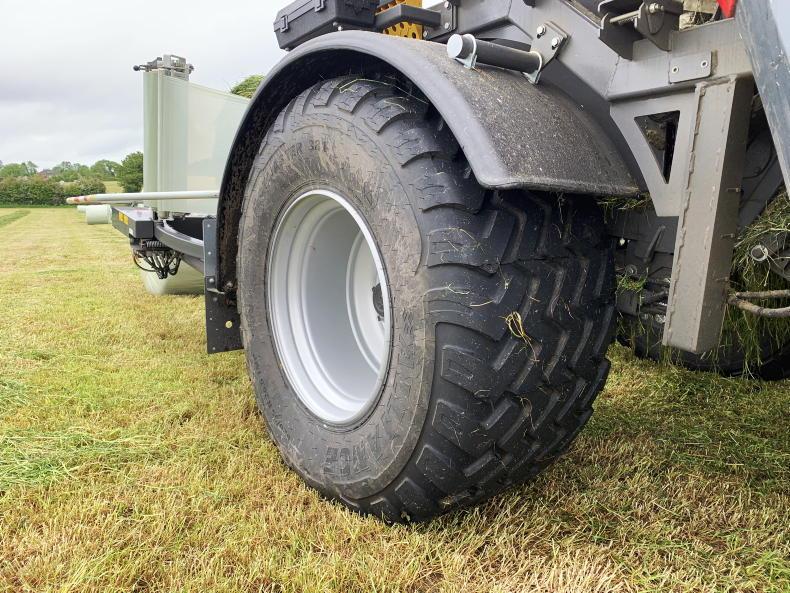
The RB 3130F Protec is fitted with 620/55 R26.5 tyres.
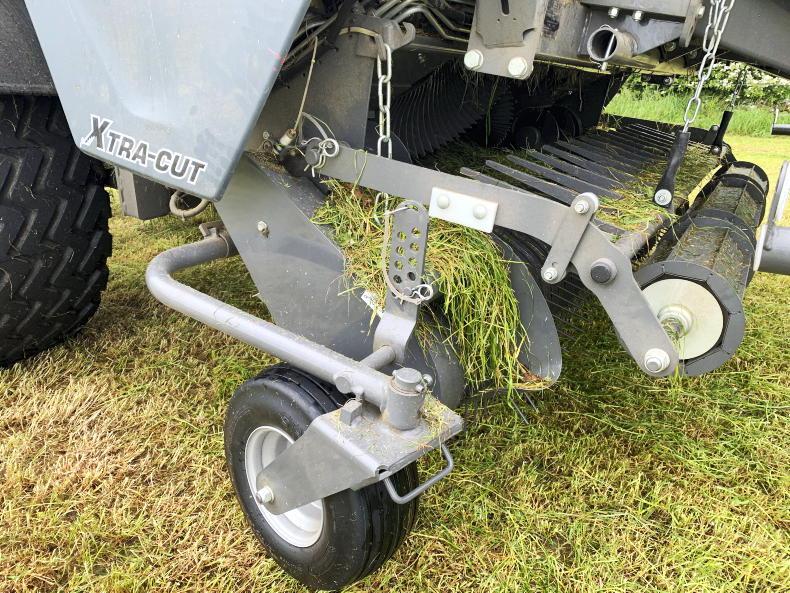
The RB 3130F Protec is fitted with a 2.25m five-tine-bar, camless pickup.
How has it performed?
Since its arrival in June 2021, the RB 3130F Protec has surpassed its 15,000 bale, trouble free. Being a load-sensing machine, the only compatible tractor in the yard of predominately Valtra tractors was a T202.
“It was an easy machine to get to grips with. Load-sensing is a great comfort and easy on the tractor. After our first year, we were surprised with how well the baler travelled, even in marginal areas. It now does at least 50% of all baling, much more than we anticipated. Although helped by the 620mm tyres, once a conscious effort is made to keep weight to a minimum by dropping bales off on approach to wet areas then it will travel as well as a standard baler,” Raymond said.
“We’ve always been of the belief that the latched chamber door makes dense, firm bales. Once it’s closed, there’s no chance it can creep open. The only difference with its chamber compared to the RP245 is that one of the floor rollers has been added to the door. This allows it to lift out of the way when the bale is transferring to the wrapping table, meaning only one roller bears the weight of the bale and eliminates bridging. The transfer system is smooth and reliable, regardless if it’s a hill or a side slope you’re on. The wrapping cycle takes between 23 and 24 seconds. I tend to run the baler in full auto mode, with the exception of releasing bales from the wrapping table manually. One thing about the transfer system is that chaff and debris builds up quite easily and quickly around the transfer mechanism and axle. This would be one of the minor areas that would benefit from a design tweak.
“The E-Link Pro touchscreen terminal is straightforward and displays all necessary information on the home screen. There is also a camera to show the wrapper table,” concluded Raymond.
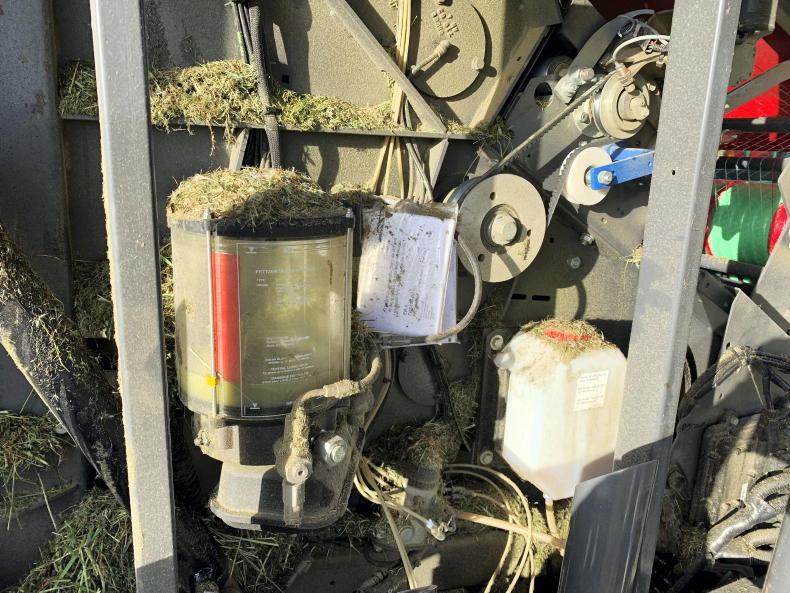
Since automatic chain lube systems have come fitted on balers, Padraig has seen a huge increase in chain lifespan.
“After 33 years of Welger, Lely Welger and now Massey Ferguson, the important part is that the after all the rebranding, the product hasn’t lost its identity. All the original reasons why I went with the brand 33 years ago remain the same today. Meanwhile, the areas needing improved were improved. Everything from performance to running costs, service and resale couldn’t be faulted. The backup we’ve had through the years has been and continues to be excellent,” said Padraig.
“It was definitely the right move. The Protec is a serious piece of kit and there are serious cost benefits to running a combination unit. Given that we work quite a bit of marginal land, I don’t think we could do without a standard baler and wrapper either,” said Raymond.

The family still runs a 2017 Lely Welger RP245 standard baler alongside the combi unit.
Weight: 5,990kg. Tyres: 620/55 R26.5 Alliance.Length: 5.9m (transport). Knives: 17-knife selectable floor (combinations; 0,8,9,17). Bale chamber: 18 rollers, (1.25m Bale diameter). Terminal: E-Link pro monitor and Isobus compatible. Pickup: 2.25m five-tine bar camless. List price: €100,000 plus VAT.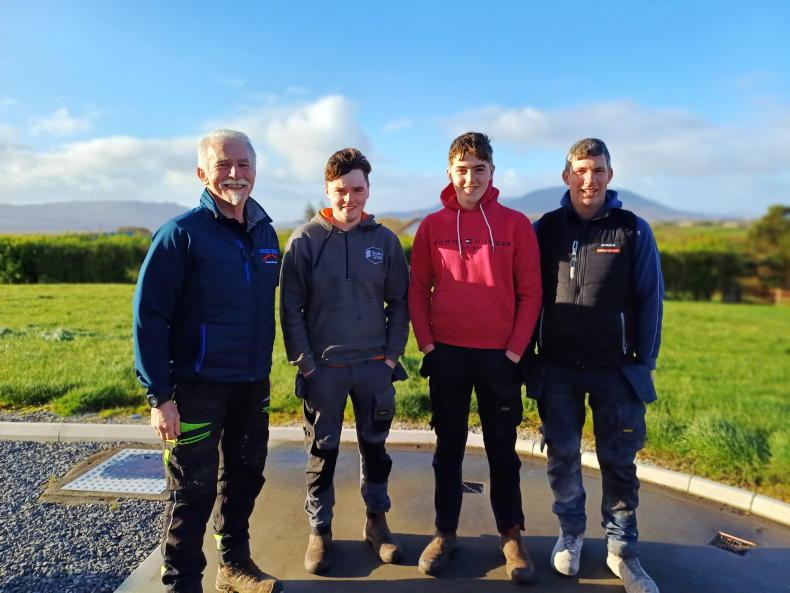
Left to right: Padraig Grealis, Sean O'Boyle, Cormac McManamon and Raymond Grealis.
Likes
Pickup and rotor intake.Weight distribution.? Dislikes
Grass and chaff builds up around axle and transfer unit.
SHARING OPTIONS: