Despite growing its sales by 25% in 2022 and exceeding its order intake in 2023, Lemken CEO Anthony van der Ley is forecasting a 6% to 7% drop in farm machinery sales in 2024.
The Lemken boss has put this down to inflation, high interest rates, the war in Ukraine and some continued effects of Covid-19.
In 2022, the 243-year-old German family-owned company recorded a turnover of €559m.
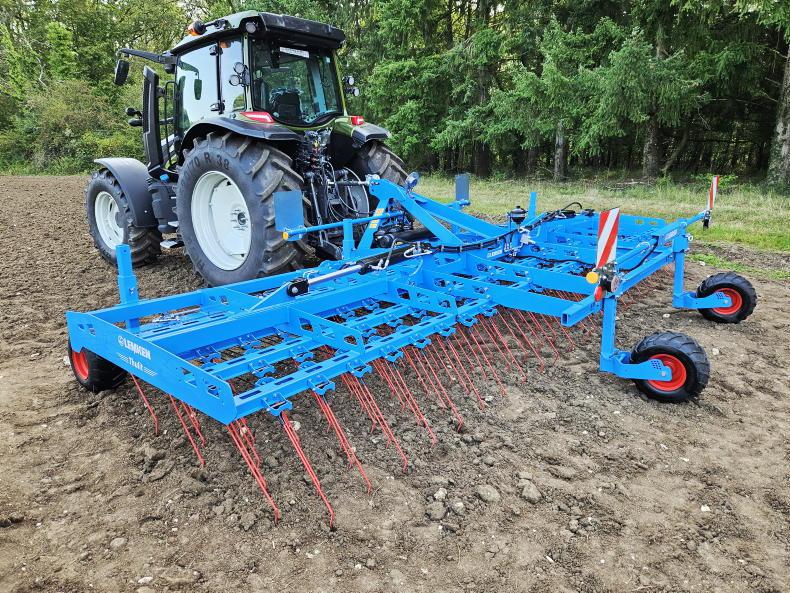
At the event, Lemken officially launched its Thulit, which is its first weeder harrow.
Today, 80% of the firm’s turnover is generated through export. The firm is currently manufacturing 15,000 machines annually, and has 1,800 employees with 30 subsidiaries across the world.
Continuing to expand
Earlier this year, Lemken agreed a deal to acquire Equalizer, a South African manufacturer of high-capacity direct drills. These include tine-based low-disturbance models, disc coulter variants and a range of precision planters.
The firm’s drills are offered with a working width of up to 24m. Lemken said there was no overlap in the company’s portfolios and that Equalizer allowed Lemken to cater for markets it had not been able to serve up to then.
Also, in the past 12 months, Lemken has invested in the Dutch ag-tech specialist business Track32. Track32 is a software company which specialises in offering artificial intelligence (AI) solutions. The move was not entirely out of the blue, with Lemken already having been working with the company, jointly developing its IC-Weeder AI, which is a mechanical hoeing machine that distinguishes between sugar beets and weeds. 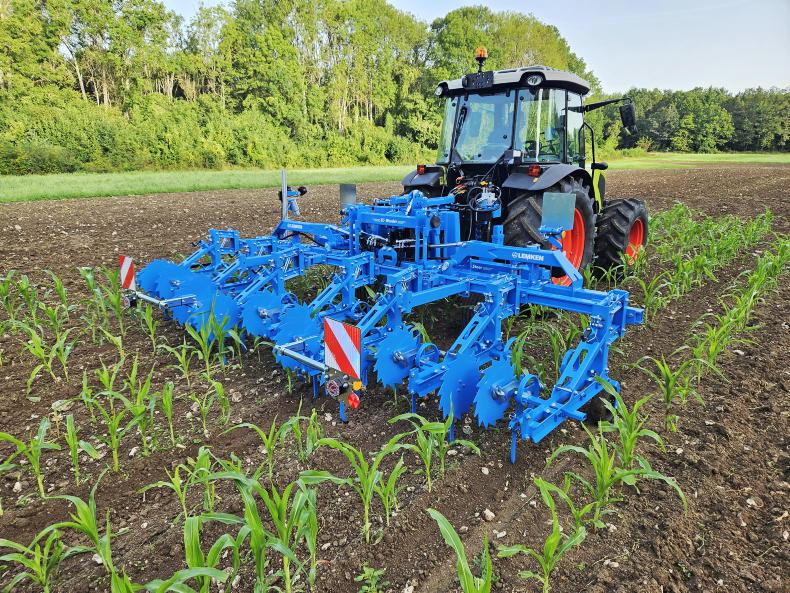
Going forward, all Steketee machines will now be delivered in Lemken blue instead of Steketee red.
Steketee finally becomes blue
Five years ago, Lemken acquired the Dutch manufacturer, Steketee. Its goal was to expand its crop care product portfolio with implements for mechanical weed control and future-oriented camera-assisted machine guidance.
Soon after at the end of 2020, Lemken made the decision to permanently discontinue the production of its conventional sprayers.
At the time, CEO Anthony van der Ley said that after 10 years in this market the company did not achieve a market share worth continuing production for, and that the legal requirements for sprayers were increasing and becoming more and more disparate.
Instead, Lemken put time and money into expanding the Steketee portfolio. Based in the southwest of the Netherlands, Steketee was initially employing 30 to 35 staff, which has now increased to 66 people.
Since the acquisition, Steketee has been channelled through Lemken’s wider dealer network. In that time, Lemken has managed to triple Steketee’s turnover and further develop its range of mechanical weeders. At present, its three largest markets are France, Germany and China.
At the event in France, Lemken announced that it was now fully integrating its crop care business, meaning Steketee is becoming Lemken. This means all Steketee machines will be delivered in Lemken blue instead of Steketee red. This is the same as what Lemken did with the two sprayer makers, RTS and Jacoby, which it purchased in 2005.
New factory
At the time of the Steketee takeover, Lemken made the decision to keep production in the Netherlands as that is where the staff expertise was located. It took out a five-year lease on the factory from the brand’s previous owner.
This month, Lemken will begin building a new factory for its crop care range.
This will be built on a 5ha site in Dinteloord, 24km away from the current manufacturing facility in the Netherlands.
Lemken says this new factory will enable them to increase output by two to three times its current production, and the manufacturer plans to double its staff there in the coming years.
As part of this process, Lemken says its product portfolio of machines for mechanical weed control and chemical crop protection will be continuously adapted and expanded.
At the event, Lemken officially launched its Thulit, which is its first weeder harrow, which it says is the last piece in the puzzle to round off its range of mechanical weed control implements.
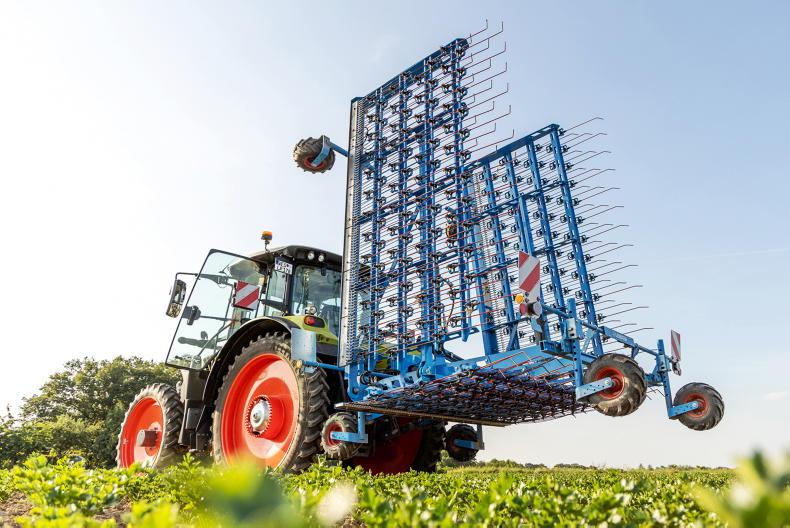
The Thulit harrow will initially be available in limited quantities in working widths of six and nine metres for the spring of 2024.
Featuring four beams and eight rows of harrow tines, Lemken has opted for a new concept of individual hydraulic tine pressure adjustment, over the typical spring combination setup.
The manufacturer says this ensures that the tines deliver more even pressure across the full working surface, especially on uneven ground.
The pressure can be continuously adjusted to up to 5kg per tine, while driving, designed to carry out a good job during the sensitive crop growth stages. The tines are arranged with a line spacing of 31.25mm.
A straightforward quick-change system makes it easy to replace the harrow tines.
Lemken says that due to its generous clearance height and design that removes the need for the usual springs, it is almost impossible to find plants getting caught underneath the frame.
The hydraulic system further supports width section control within the frame sections, to avoid multiple passes across parts of the field.
The firm noted that minimising the frame weight was a core aim in designing this machine. This was achieved by reducing the number of moving parts in comparison to similar models. For transport, the tines fold in automatically.
The Thulit harrow will initially be available in limited quantities in working widths of six and nine metres for the spring of 2024.
IC Light gains
new camera
The firm introduced its new IC-Light+ camera on its mechanical hoes to capture the near-infrared range for easier weed detection in crops with a high proportion of blue in the leaves.
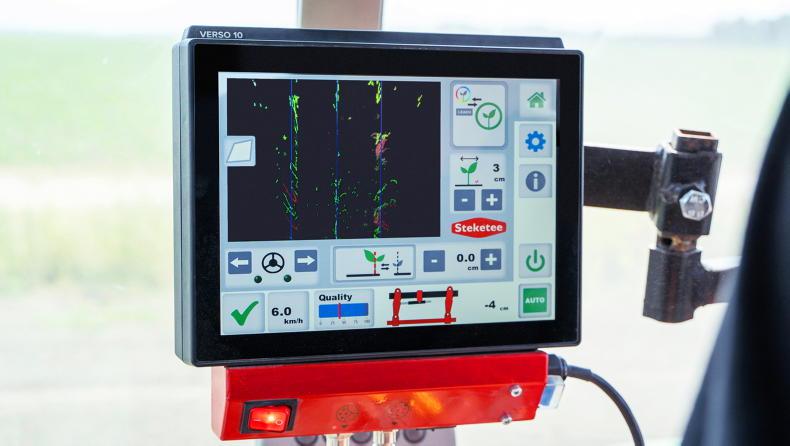
The system is operated via the IC-Light terminal, and allows hoeing as close as 2cm from plants at speeds of up to 15km/h.
This differs to the firm’s standard IC-Light camera system, which distinguishes between shades of green and red. Lemken says the additional tones of blue captured by the IC-Light+ is very beneficial when working in onions, leeks, broccoli and red cabbage.
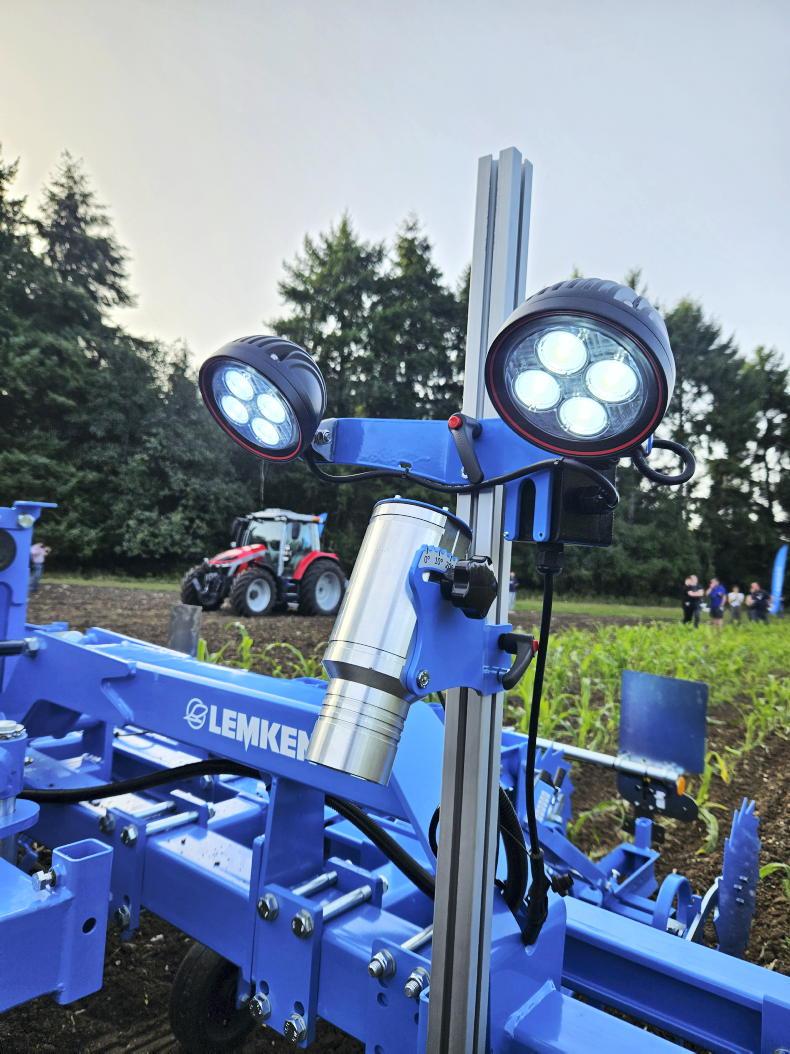
The camera captured the near-infrared range for easier weed detection in crops with a high proportion of blue in the leaves.
It says the internally developed camera system allows young plants or those with a particularly fine structure to be better identified.
Lemken even claims the new camera system is capable of working with onions the size of a pin.
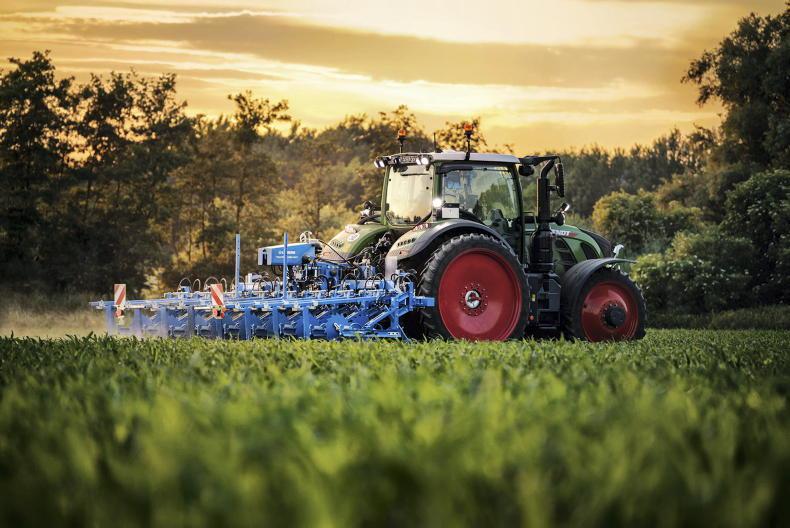
Lemken even claims the new camera system is capable of working with onions the size of a pin.
The system is operated via the IC-Light terminal, and allows hoeing as close as 2cm from plants at speeds of up to 15km/h.
The camera detects up to five rows of plants at a time and controls the steering of the hoeing machine between the rows.
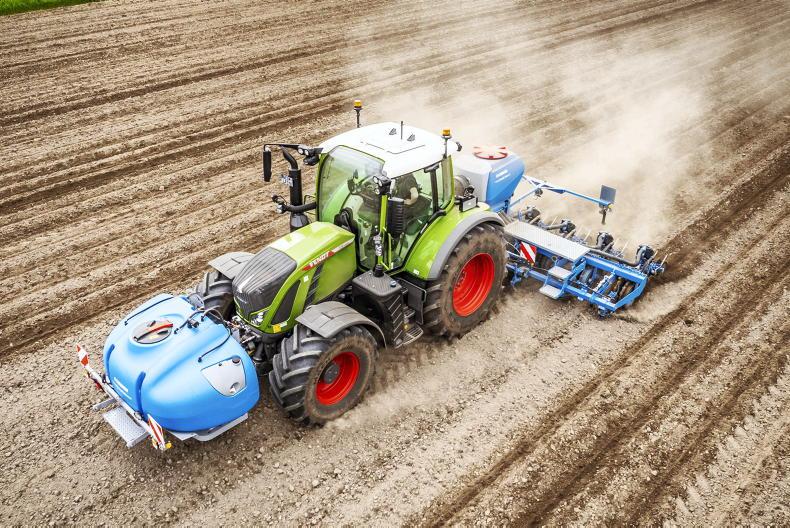
New functions include electrical single-row deactivation via IsoBus which enables row-by-row automatic section control by means of GPS.
More functions for front tanks
The SprayHub front tank can now be used with the SprayKit and a rear-mounted hoeing machine for band spraying during hoeing.
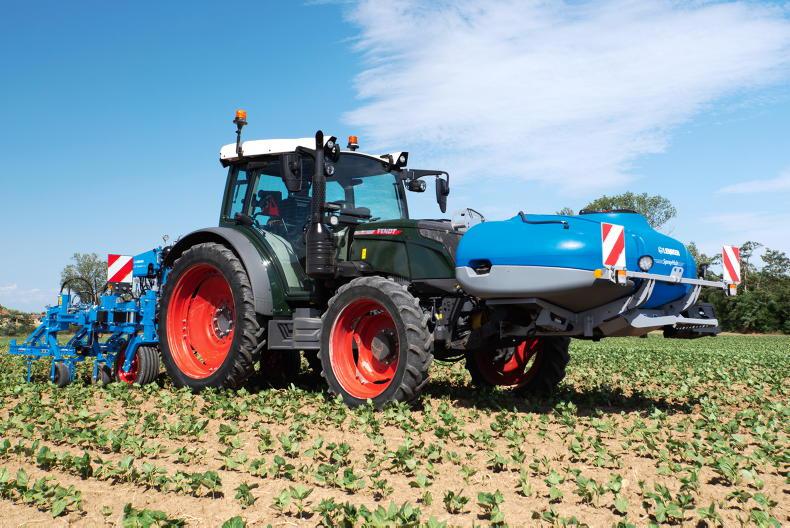
The SprayHub front tank can now be used with the SprayKit and a rear-mounted hoeing machine for band spraying during hoeing.
It is possible to run two nozzles per row, so that the herbicide can be sprayed from the side and under the leaves of the crops. Lemken says that the combination of hoeing and band spraying in one pass can reduce the workload by up to 60%.
Available in 1,100- or 1,500-litre capacities, the standard spec of the SprayHub includes a clean water tank, hand wash tank, filling filter, agitator, cleaning systems and dedicated controls. The IsoBus controlled tank can be operated via the iQblue spray software.
New functions include electrical single-row deactivation via IsoBus which enables row-by-row automatic section control by means of GPS.
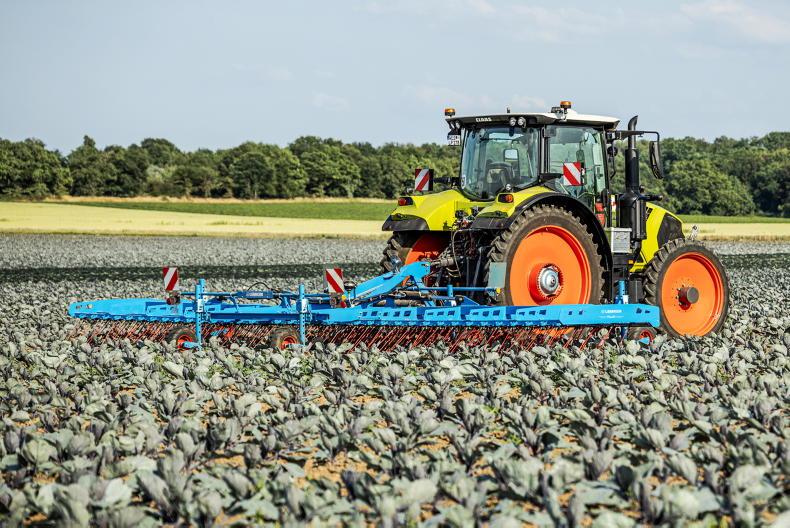
Featuring four beams and eight rows of harrow tines, Lemken has opted for a new concept of individual hydraulic tine pressure adjustment, over the typical spring combination setup.
In addition, the unit can be set up to apply liquid fertiliser. Other options include an induction nozzle to help break up solids and a CTS connection for contactless induction. The application of liquid fertiliser is also possible.
The SprayHub front tank can be combined with a wide range of different machines, while the SprayKit can be adjusted to any specific application.
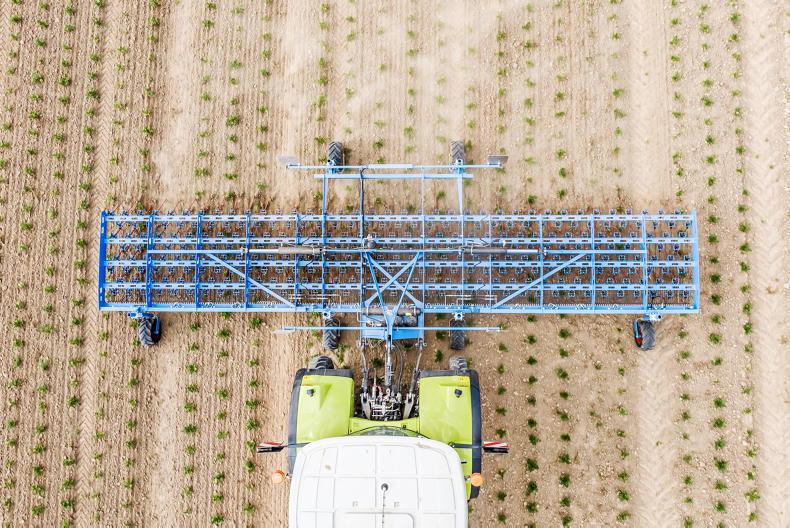
The tines are arranged with a line spacing of 31.25mm.
Despite growing its sales by 25% in 2022 and exceeding its order intake in 2023, Lemken CEO Anthony van der Ley is forecasting a 6% to 7% drop in farm machinery sales in 2024.
The Lemken boss has put this down to inflation, high interest rates, the war in Ukraine and some continued effects of Covid-19.
In 2022, the 243-year-old German family-owned company recorded a turnover of €559m.
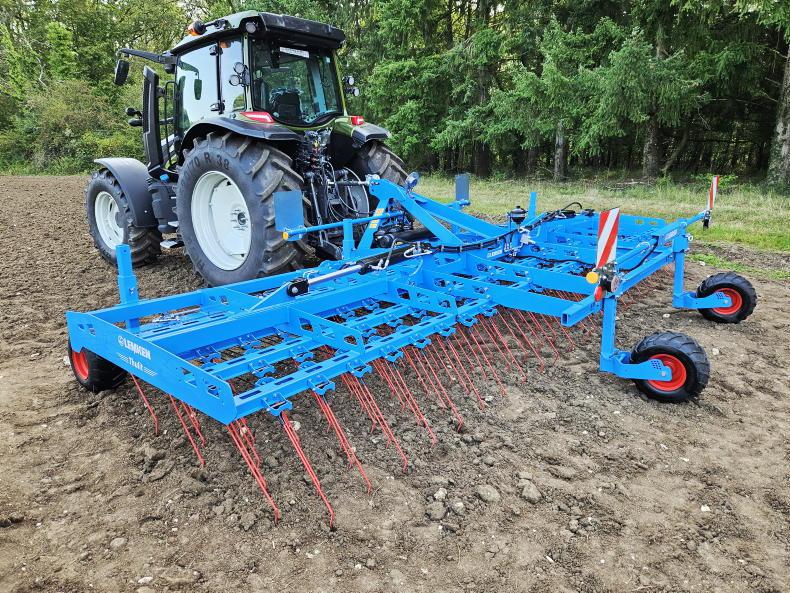
At the event, Lemken officially launched its Thulit, which is its first weeder harrow.
Today, 80% of the firm’s turnover is generated through export. The firm is currently manufacturing 15,000 machines annually, and has 1,800 employees with 30 subsidiaries across the world.
Continuing to expand
Earlier this year, Lemken agreed a deal to acquire Equalizer, a South African manufacturer of high-capacity direct drills. These include tine-based low-disturbance models, disc coulter variants and a range of precision planters.
The firm’s drills are offered with a working width of up to 24m. Lemken said there was no overlap in the company’s portfolios and that Equalizer allowed Lemken to cater for markets it had not been able to serve up to then.
Also, in the past 12 months, Lemken has invested in the Dutch ag-tech specialist business Track32. Track32 is a software company which specialises in offering artificial intelligence (AI) solutions. The move was not entirely out of the blue, with Lemken already having been working with the company, jointly developing its IC-Weeder AI, which is a mechanical hoeing machine that distinguishes between sugar beets and weeds. 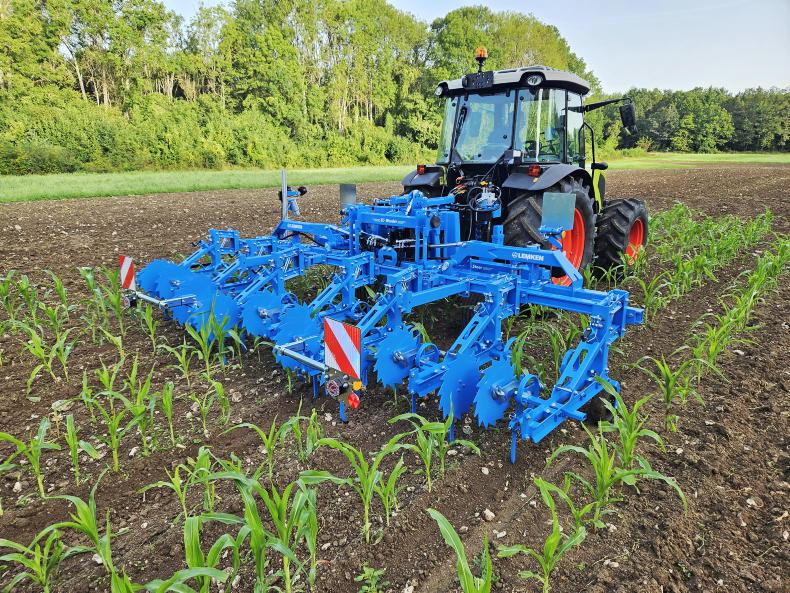
Going forward, all Steketee machines will now be delivered in Lemken blue instead of Steketee red.
Steketee finally becomes blue
Five years ago, Lemken acquired the Dutch manufacturer, Steketee. Its goal was to expand its crop care product portfolio with implements for mechanical weed control and future-oriented camera-assisted machine guidance.
Soon after at the end of 2020, Lemken made the decision to permanently discontinue the production of its conventional sprayers.
At the time, CEO Anthony van der Ley said that after 10 years in this market the company did not achieve a market share worth continuing production for, and that the legal requirements for sprayers were increasing and becoming more and more disparate.
Instead, Lemken put time and money into expanding the Steketee portfolio. Based in the southwest of the Netherlands, Steketee was initially employing 30 to 35 staff, which has now increased to 66 people.
Since the acquisition, Steketee has been channelled through Lemken’s wider dealer network. In that time, Lemken has managed to triple Steketee’s turnover and further develop its range of mechanical weeders. At present, its three largest markets are France, Germany and China.
At the event in France, Lemken announced that it was now fully integrating its crop care business, meaning Steketee is becoming Lemken. This means all Steketee machines will be delivered in Lemken blue instead of Steketee red. This is the same as what Lemken did with the two sprayer makers, RTS and Jacoby, which it purchased in 2005.
New factory
At the time of the Steketee takeover, Lemken made the decision to keep production in the Netherlands as that is where the staff expertise was located. It took out a five-year lease on the factory from the brand’s previous owner.
This month, Lemken will begin building a new factory for its crop care range.
This will be built on a 5ha site in Dinteloord, 24km away from the current manufacturing facility in the Netherlands.
Lemken says this new factory will enable them to increase output by two to three times its current production, and the manufacturer plans to double its staff there in the coming years.
As part of this process, Lemken says its product portfolio of machines for mechanical weed control and chemical crop protection will be continuously adapted and expanded.
At the event, Lemken officially launched its Thulit, which is its first weeder harrow, which it says is the last piece in the puzzle to round off its range of mechanical weed control implements.
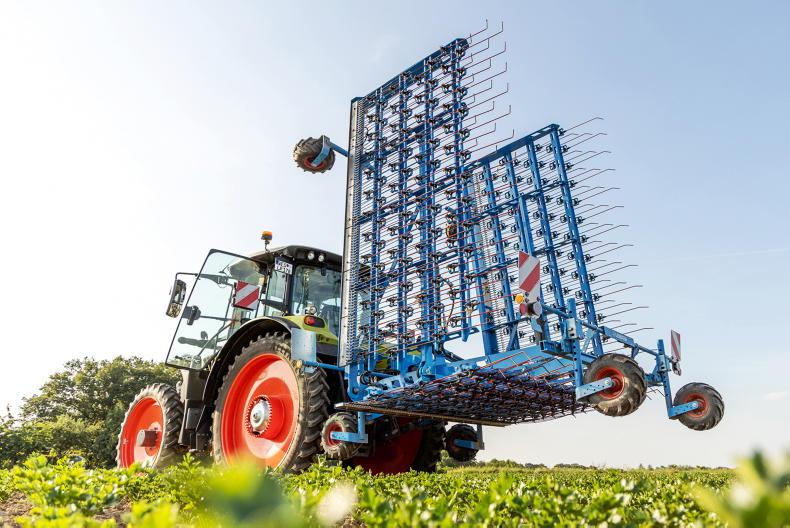
The Thulit harrow will initially be available in limited quantities in working widths of six and nine metres for the spring of 2024.
Featuring four beams and eight rows of harrow tines, Lemken has opted for a new concept of individual hydraulic tine pressure adjustment, over the typical spring combination setup.
The manufacturer says this ensures that the tines deliver more even pressure across the full working surface, especially on uneven ground.
The pressure can be continuously adjusted to up to 5kg per tine, while driving, designed to carry out a good job during the sensitive crop growth stages. The tines are arranged with a line spacing of 31.25mm.
A straightforward quick-change system makes it easy to replace the harrow tines.
Lemken says that due to its generous clearance height and design that removes the need for the usual springs, it is almost impossible to find plants getting caught underneath the frame.
The hydraulic system further supports width section control within the frame sections, to avoid multiple passes across parts of the field.
The firm noted that minimising the frame weight was a core aim in designing this machine. This was achieved by reducing the number of moving parts in comparison to similar models. For transport, the tines fold in automatically.
The Thulit harrow will initially be available in limited quantities in working widths of six and nine metres for the spring of 2024.
IC Light gains
new camera
The firm introduced its new IC-Light+ camera on its mechanical hoes to capture the near-infrared range for easier weed detection in crops with a high proportion of blue in the leaves.
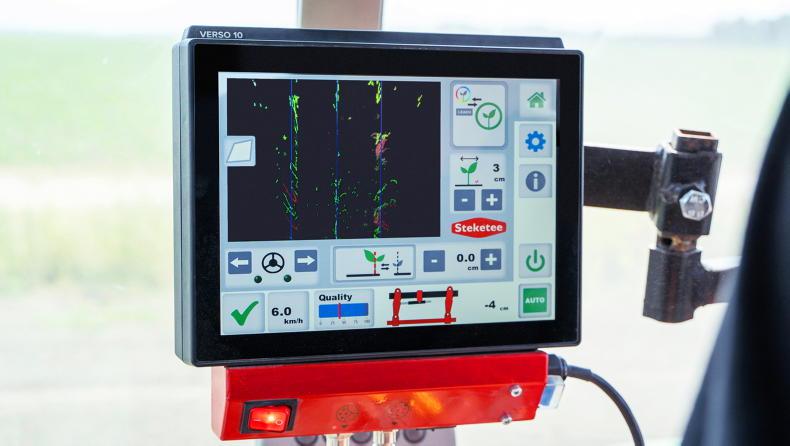
The system is operated via the IC-Light terminal, and allows hoeing as close as 2cm from plants at speeds of up to 15km/h.
This differs to the firm’s standard IC-Light camera system, which distinguishes between shades of green and red. Lemken says the additional tones of blue captured by the IC-Light+ is very beneficial when working in onions, leeks, broccoli and red cabbage.
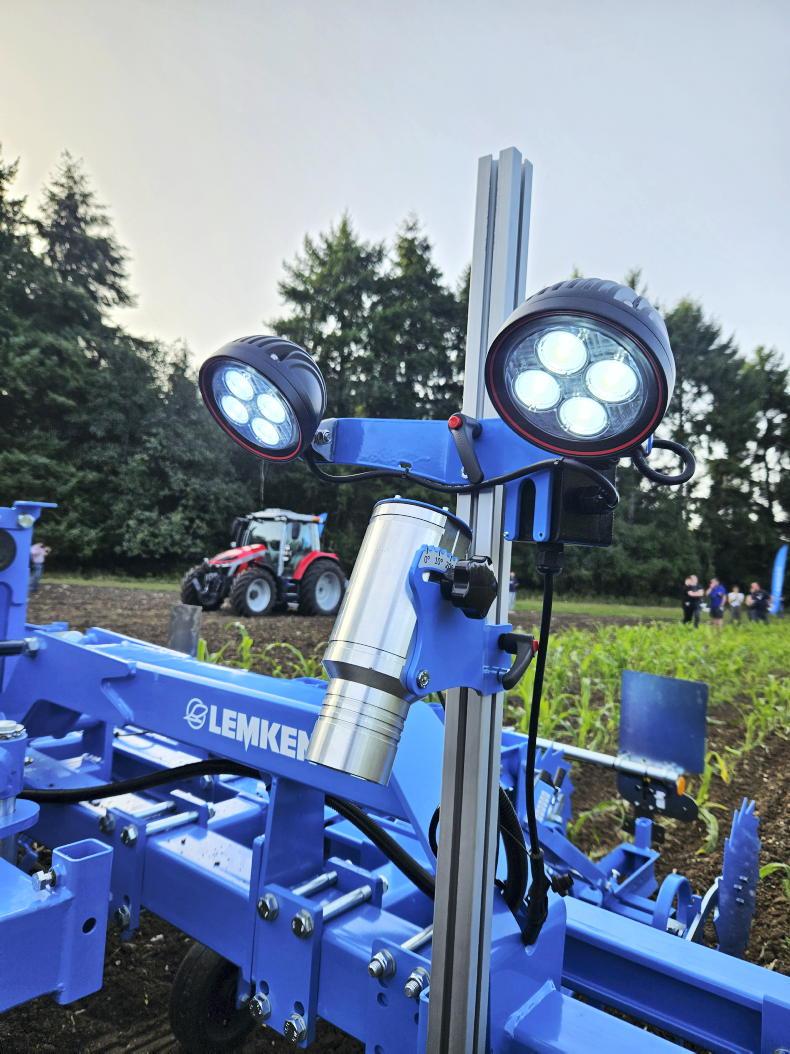
The camera captured the near-infrared range for easier weed detection in crops with a high proportion of blue in the leaves.
It says the internally developed camera system allows young plants or those with a particularly fine structure to be better identified.
Lemken even claims the new camera system is capable of working with onions the size of a pin.
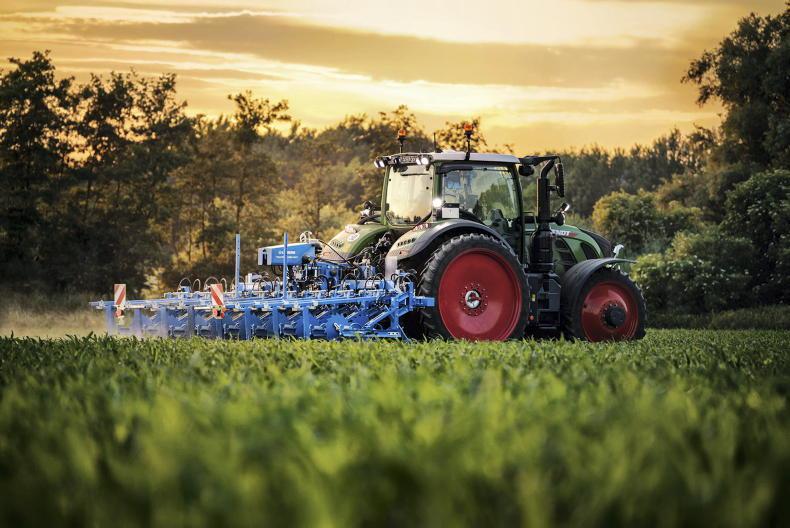
Lemken even claims the new camera system is capable of working with onions the size of a pin.
The system is operated via the IC-Light terminal, and allows hoeing as close as 2cm from plants at speeds of up to 15km/h.
The camera detects up to five rows of plants at a time and controls the steering of the hoeing machine between the rows.
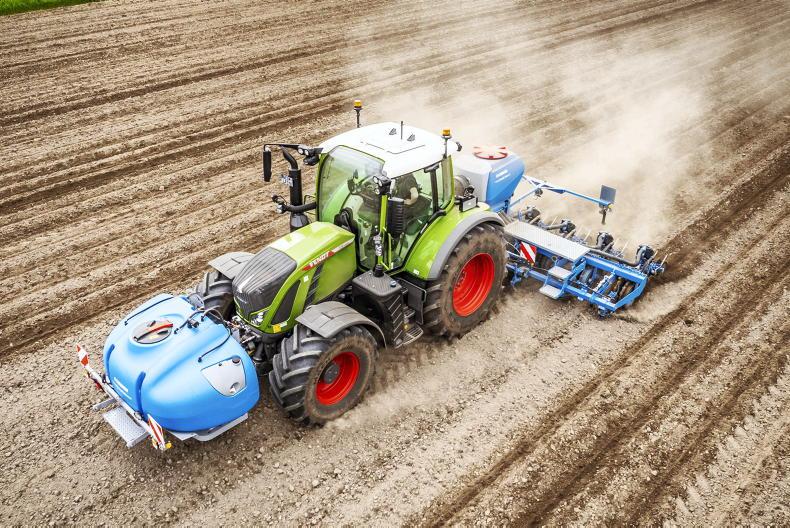
New functions include electrical single-row deactivation via IsoBus which enables row-by-row automatic section control by means of GPS.
More functions for front tanks
The SprayHub front tank can now be used with the SprayKit and a rear-mounted hoeing machine for band spraying during hoeing.
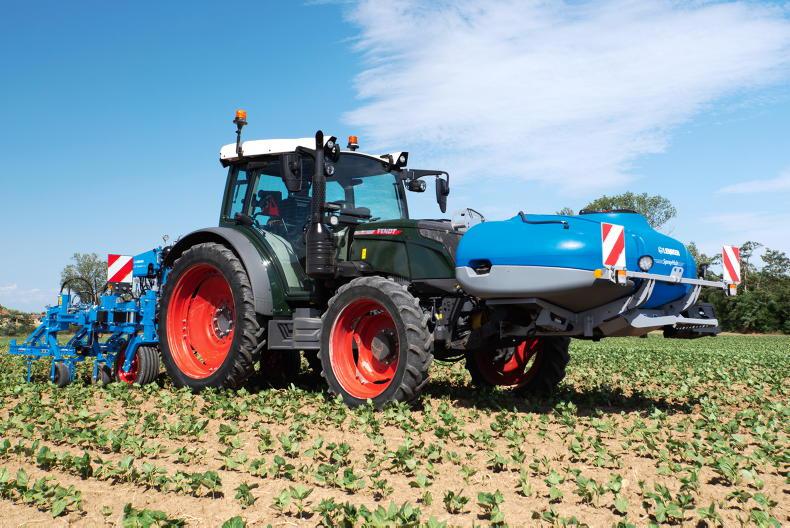
The SprayHub front tank can now be used with the SprayKit and a rear-mounted hoeing machine for band spraying during hoeing.
It is possible to run two nozzles per row, so that the herbicide can be sprayed from the side and under the leaves of the crops. Lemken says that the combination of hoeing and band spraying in one pass can reduce the workload by up to 60%.
Available in 1,100- or 1,500-litre capacities, the standard spec of the SprayHub includes a clean water tank, hand wash tank, filling filter, agitator, cleaning systems and dedicated controls. The IsoBus controlled tank can be operated via the iQblue spray software.
New functions include electrical single-row deactivation via IsoBus which enables row-by-row automatic section control by means of GPS.
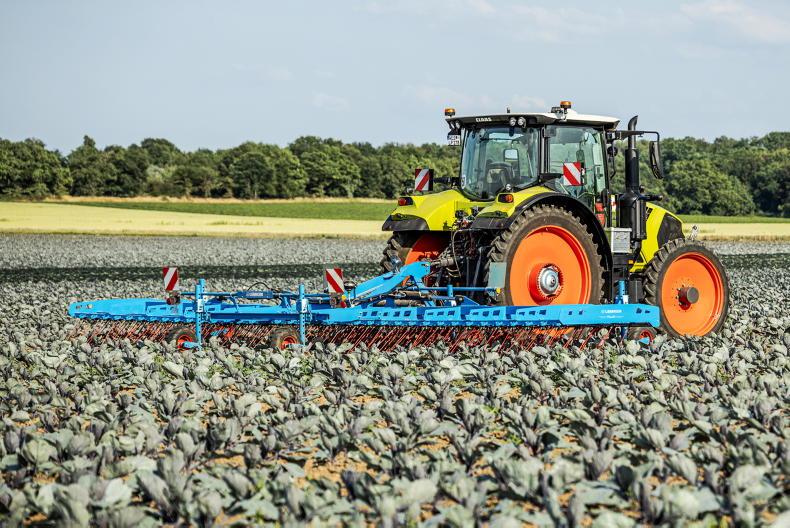
Featuring four beams and eight rows of harrow tines, Lemken has opted for a new concept of individual hydraulic tine pressure adjustment, over the typical spring combination setup.
In addition, the unit can be set up to apply liquid fertiliser. Other options include an induction nozzle to help break up solids and a CTS connection for contactless induction. The application of liquid fertiliser is also possible.
The SprayHub front tank can be combined with a wide range of different machines, while the SprayKit can be adjusted to any specific application.
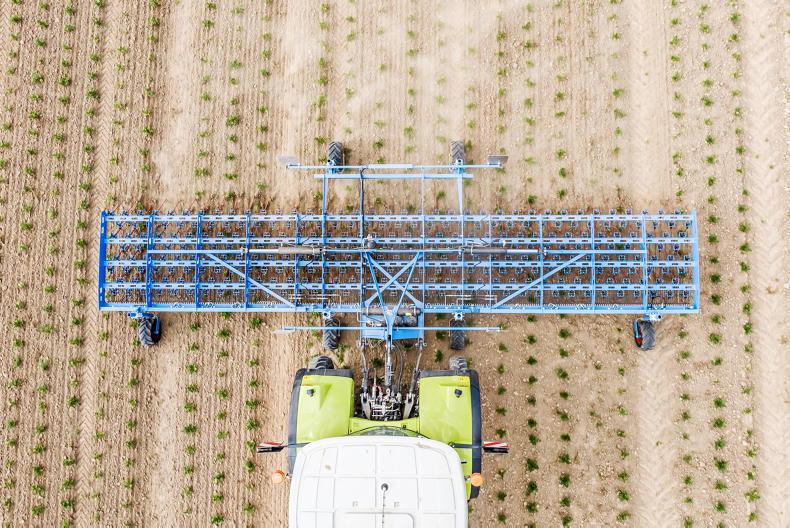
The tines are arranged with a line spacing of 31.25mm.
SHARING OPTIONS: