Building a successful farm-based renewable energy business requires seizing opportunities as they arise and adapting to new ones as they emerge. This was the path taken by Gavin Winters of Winters Renewables, based in Co Tyrone.
Gavin began by growing willow and supplying and maintaining boilers, but now operates a 500kW anaerobic digestion plant and supplies woodchip to customers in the mid-Ulster and northwest regions.
The Irish Farmers Journal recently visited Gavin to learn more about his journey.
Willow and woodchip boilers
With a degree in agricultural engineering from Harper Adams University, Gavin worked in agri-contracting and suckler farming before focusing on his biomass business. In the mid-2000s, he availed of a grant to help cover the cost of planting 130ac of willow on his land.
At the time, there was significant talk and hype around growing willow and biomass crops in Northern Ireland.
He also secured funding to develop a 250m2 woodchip drying floor, with the aim of drying woodchip down to 15% to 20% moisture and supplying local biomass boilers.
Dried woodchip was burned in a boiler to create heat to dry the woodchip, an expensive way of doing it, he admits.

Gavin Winters.
In 2005, Gavin took on the dealership for Guntamatic biomass boilers, selling, installing and maintaining them in both the Republic of Ireland and Northern Ireland.
When the Renewable Heat Incentive (RHI) was established in Northern Ireland, the business expanded rapidly. Gavin explains that, at one stage, along with his brother Barry, he had 11 staff working for him around the country installing boilers. This also helped develop new markets for his woodchip.
However, in 2014, Gavin decided to plough up his willow crop and return the fields to grass.
He said that the yields had gradually become poorer and his plans to use the willow for the bioremediation of sludge didn’t materialise. The returns were marginal.
Furthermore, when the RHI collapsed, the market for biomass came under pressure. He subsequently scaled back his boiler business and decided to concentrate on his anaerobic digestion (AD) pant.
However, he continued to buy in pulp wood and cuttings from local forests.
He uses contractor Rodney Nobel to chip the wood using his mobile chipper, before drying it down with his existing dryer using waste heat from the AD plant.

Gavin supplies around 1,500 tonnes of woodchip to businesses each year.
He says that this is a much simpler business model and ties in well with his AD operation.
Gavin can deliver 20m3 to 40m3 loads of woodchip anywhere within a 40-mile radius of his farm.
The woodchip can be either tipped or blown into the stores using a woodchip blower fitted to the back of one of his delivery trailers. Some customers send lorries for collection.
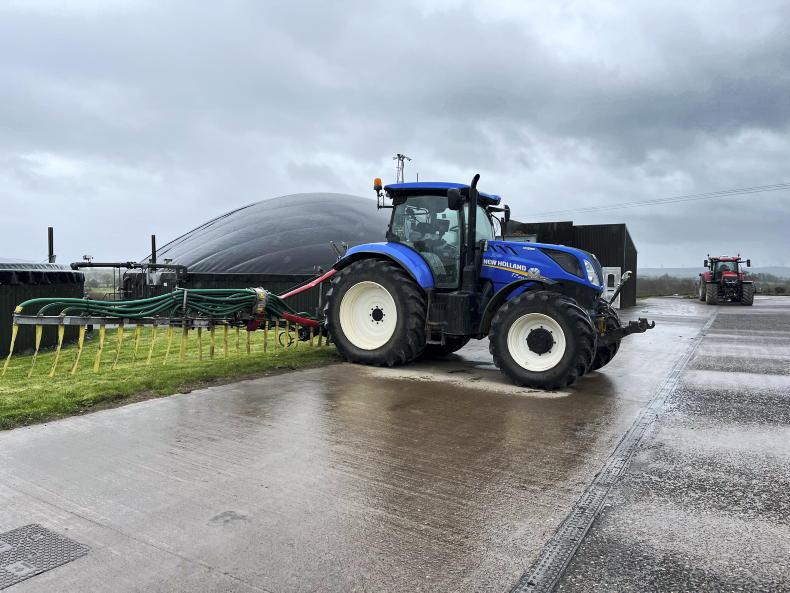
Gavin uses a dribble bar to spread digestate.
He continues to supply chip to multiple customers, all of which run biomass boilers, and include Lough Eske Castle, Donegal; Corick House Hotel, Tyrone; the Omagh Leisure Centre; and a number of nursing homes. In total, Gavin supplies around 1,500t of woodchip to businesses each year.
Anaerobic digestion plant
Realising that using woodchip to dry woodchip was costly, Gavin started looking into AD plants in 2009, with the aim of using the waste heat from the system to dry the woodchip for free.
Having access to a grid connection to export electricity was key to the viability of the plant and, luckily, he already had significant grid capacity on his farm.

Winters' renewables, 17 Shaneragh Road, Dromore, Omagh, Co Tyrone.
In 2005, he applied for permission for a large wood gasification system, and secured a significant grid connection.
Although the gasification system didn’t proceed, he subsequently applied for planning for a wind turbine.
This meant he had spare grid capacity, which would allow him to export electricity from an AD plant.
In 2009, he secured planning for the plant, and with the introduction of the Northern Ireland Renewables Obligation (NIRO) scheme in 2010, Gavin knew the AD operation would be viable.
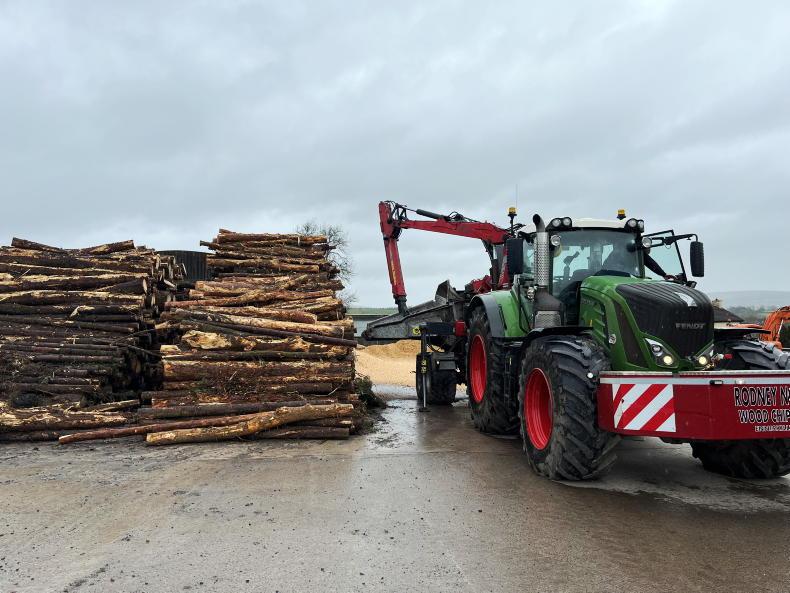
He uses contractor Rodney Nobel to chip the wood using his mobile chipper.
Like many AD plants in Northern Ireland, the project was financed by an investment firm. The project was commissioned in 2013 but, in 2020, Gavin successfully refinanced the project and took full ownership of it.
The AgriKomp AD plant produces biogas, which is then combusted in two Scania DC13 six-cylinder biogas engines, producing 500kW of electricity, most of which is exported to the grid.
He receives renewables obligation certificates for each unit of electricity generated.
A power purchase agreement (PPA) is in place for all electricity exported to the grid.
A district heating system is used to distribute the waste heat to the woodchip drying floor, his parents’ house and the farm workshop.
The plant is fed with approximately 25t of silage, 13t of lactose and 2,900 gallons of slurry per day.
He stopped using chicken manure due to inconsistent quality and concerns about antibiotic use.
The plant runs at an internal temperature of around 50°C, with an average retention time of 45 days.
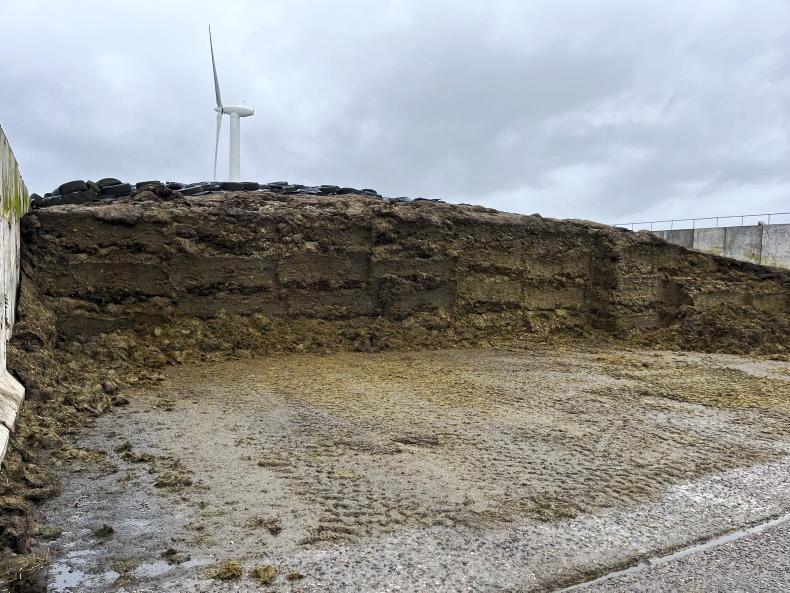
Gavin aims for four cuts of silage per year.
He aims for four cuts of silage per year across 500 acres, depending on the weather. He cannot afford to wait when the weather windows are tight, meaning that sometimes silage is harvested in less-than-ideal conditions.
Poor-quality silage produces less gas, so “you have to think of it like a dairy cow – the silage that makes the best milk makes the best gas”, he said.
Each cut is stored in a separate clamp, each of which stores around 2,500t.
This allows him to balance the quality of the silage he feeds to the plant, depending on the quality of each cut. He is due to make his first cut towards the end of April.
Most of the silage cutting and digestate spreading is done by himself and his two full-time staff with hired in help from local contractors.
Gavin uses digestate from the plant to help fertilise his silage crops and also exports it to neighbouring farms.
After every cut, he applies 2,500 to 3,000 gallons of digestate per acre along with one bag of CAN.

Gavin used an innovation grant to develop his own mobile phone app that tracks digestate use and deliveries.
He regularly analyses his digestate, which contains roughly 20 units of N, 14 units of P, and 70 units of K per 1,000 gallons.
In 2019, Gavin received an innovation grant to develop his own mobile phone app that tracks where and how much digestate has been delivered to farms and used on his own land.
He got the idea from a similar system he saw on a diet feeder to track livestock feed intake.
After securing a voucher worth £5,000 (€5,650), he drew out how he wanted the web-based app to look and function and engaged a developer from South West Regional College to design and develop it.
He now has three years’ worth of data and continues to use the app to this day.
Everything in the AD plant is recorded, from digestate, to feeding rates and biogas yield. He keeps a close eye on everything and produces quarterly reports on the plant’s performance.
Gavin says that he hears a lot of talk about biomethane plants being the next step for AD.
However, he argues that the 500kW biogas to electricity model is the ideal size for farmers, as they can be developed, run and supplied by farmers themselves.
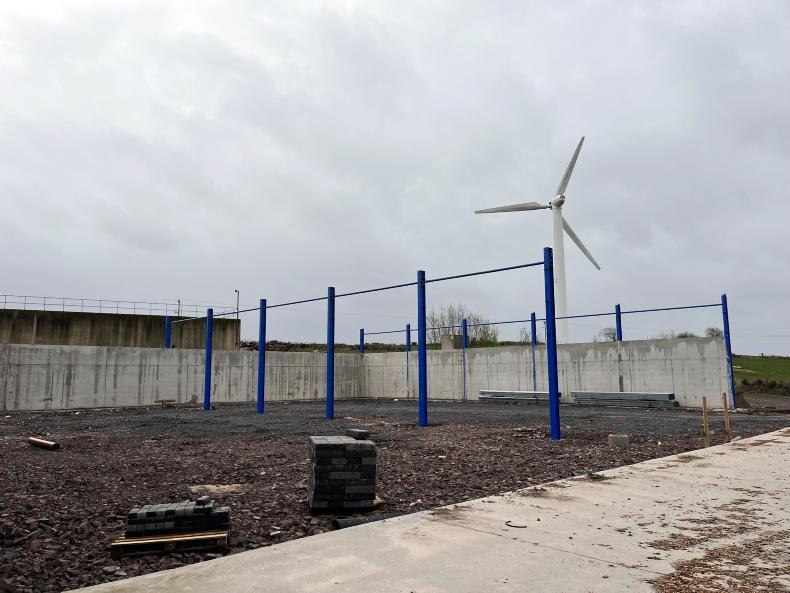
He is currently constructing a new woodchip storage shed.
Biomethane plants are significantly bigger and too large for most farmers to develop.
As a result, farmers will miss out on the chance to gain any real benefits from an AD plant, which instead will be developed by larger corporate companies.
Building a successful farm-based renewable energy business requires seizing opportunities as they arise and adapting to new ones as they emerge. This was the path taken by Gavin Winters of Winters Renewables, based in Co Tyrone.
Gavin began by growing willow and supplying and maintaining boilers, but now operates a 500kW anaerobic digestion plant and supplies woodchip to customers in the mid-Ulster and northwest regions.
The Irish Farmers Journal recently visited Gavin to learn more about his journey.
Willow and woodchip boilers
With a degree in agricultural engineering from Harper Adams University, Gavin worked in agri-contracting and suckler farming before focusing on his biomass business. In the mid-2000s, he availed of a grant to help cover the cost of planting 130ac of willow on his land.
At the time, there was significant talk and hype around growing willow and biomass crops in Northern Ireland.
He also secured funding to develop a 250m2 woodchip drying floor, with the aim of drying woodchip down to 15% to 20% moisture and supplying local biomass boilers.
Dried woodchip was burned in a boiler to create heat to dry the woodchip, an expensive way of doing it, he admits.

Gavin Winters.
In 2005, Gavin took on the dealership for Guntamatic biomass boilers, selling, installing and maintaining them in both the Republic of Ireland and Northern Ireland.
When the Renewable Heat Incentive (RHI) was established in Northern Ireland, the business expanded rapidly. Gavin explains that, at one stage, along with his brother Barry, he had 11 staff working for him around the country installing boilers. This also helped develop new markets for his woodchip.
However, in 2014, Gavin decided to plough up his willow crop and return the fields to grass.
He said that the yields had gradually become poorer and his plans to use the willow for the bioremediation of sludge didn’t materialise. The returns were marginal.
Furthermore, when the RHI collapsed, the market for biomass came under pressure. He subsequently scaled back his boiler business and decided to concentrate on his anaerobic digestion (AD) pant.
However, he continued to buy in pulp wood and cuttings from local forests.
He uses contractor Rodney Nobel to chip the wood using his mobile chipper, before drying it down with his existing dryer using waste heat from the AD plant.

Gavin supplies around 1,500 tonnes of woodchip to businesses each year.
He says that this is a much simpler business model and ties in well with his AD operation.
Gavin can deliver 20m3 to 40m3 loads of woodchip anywhere within a 40-mile radius of his farm.
The woodchip can be either tipped or blown into the stores using a woodchip blower fitted to the back of one of his delivery trailers. Some customers send lorries for collection.
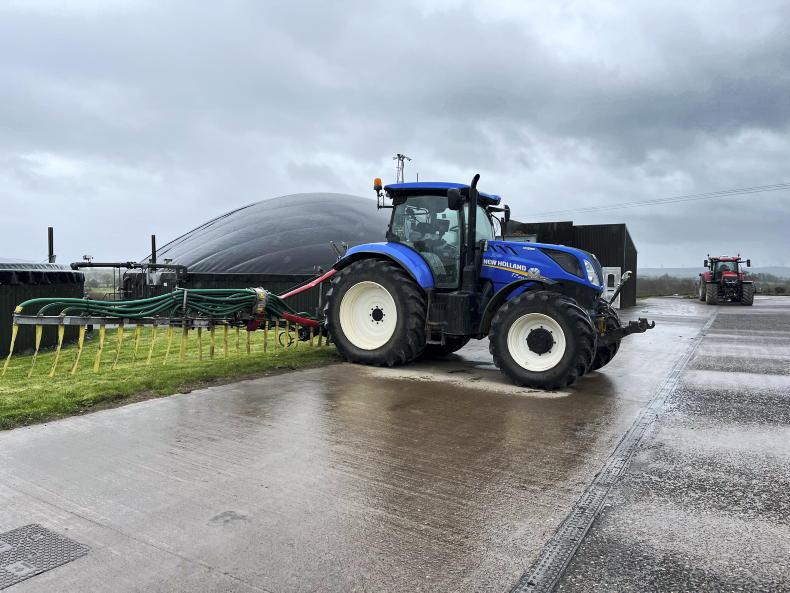
Gavin uses a dribble bar to spread digestate.
He continues to supply chip to multiple customers, all of which run biomass boilers, and include Lough Eske Castle, Donegal; Corick House Hotel, Tyrone; the Omagh Leisure Centre; and a number of nursing homes. In total, Gavin supplies around 1,500t of woodchip to businesses each year.
Anaerobic digestion plant
Realising that using woodchip to dry woodchip was costly, Gavin started looking into AD plants in 2009, with the aim of using the waste heat from the system to dry the woodchip for free.
Having access to a grid connection to export electricity was key to the viability of the plant and, luckily, he already had significant grid capacity on his farm.

Winters' renewables, 17 Shaneragh Road, Dromore, Omagh, Co Tyrone.
In 2005, he applied for permission for a large wood gasification system, and secured a significant grid connection.
Although the gasification system didn’t proceed, he subsequently applied for planning for a wind turbine.
This meant he had spare grid capacity, which would allow him to export electricity from an AD plant.
In 2009, he secured planning for the plant, and with the introduction of the Northern Ireland Renewables Obligation (NIRO) scheme in 2010, Gavin knew the AD operation would be viable.
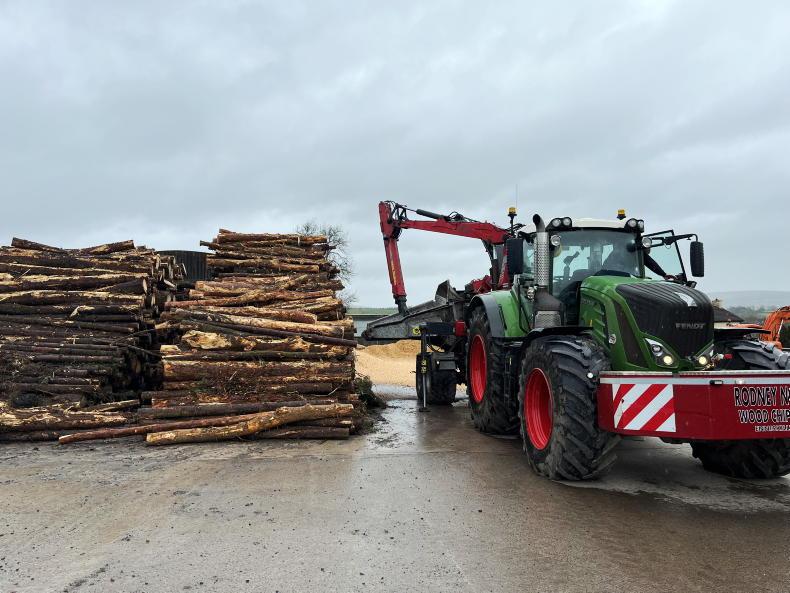
He uses contractor Rodney Nobel to chip the wood using his mobile chipper.
Like many AD plants in Northern Ireland, the project was financed by an investment firm. The project was commissioned in 2013 but, in 2020, Gavin successfully refinanced the project and took full ownership of it.
The AgriKomp AD plant produces biogas, which is then combusted in two Scania DC13 six-cylinder biogas engines, producing 500kW of electricity, most of which is exported to the grid.
He receives renewables obligation certificates for each unit of electricity generated.
A power purchase agreement (PPA) is in place for all electricity exported to the grid.
A district heating system is used to distribute the waste heat to the woodchip drying floor, his parents’ house and the farm workshop.
The plant is fed with approximately 25t of silage, 13t of lactose and 2,900 gallons of slurry per day.
He stopped using chicken manure due to inconsistent quality and concerns about antibiotic use.
The plant runs at an internal temperature of around 50°C, with an average retention time of 45 days.
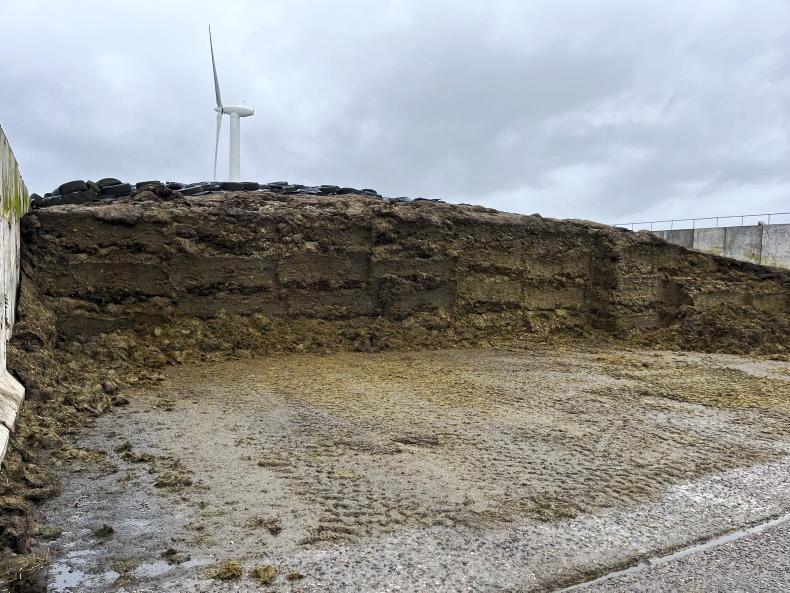
Gavin aims for four cuts of silage per year.
He aims for four cuts of silage per year across 500 acres, depending on the weather. He cannot afford to wait when the weather windows are tight, meaning that sometimes silage is harvested in less-than-ideal conditions.
Poor-quality silage produces less gas, so “you have to think of it like a dairy cow – the silage that makes the best milk makes the best gas”, he said.
Each cut is stored in a separate clamp, each of which stores around 2,500t.
This allows him to balance the quality of the silage he feeds to the plant, depending on the quality of each cut. He is due to make his first cut towards the end of April.
Most of the silage cutting and digestate spreading is done by himself and his two full-time staff with hired in help from local contractors.
Gavin uses digestate from the plant to help fertilise his silage crops and also exports it to neighbouring farms.
After every cut, he applies 2,500 to 3,000 gallons of digestate per acre along with one bag of CAN.

Gavin used an innovation grant to develop his own mobile phone app that tracks digestate use and deliveries.
He regularly analyses his digestate, which contains roughly 20 units of N, 14 units of P, and 70 units of K per 1,000 gallons.
In 2019, Gavin received an innovation grant to develop his own mobile phone app that tracks where and how much digestate has been delivered to farms and used on his own land.
He got the idea from a similar system he saw on a diet feeder to track livestock feed intake.
After securing a voucher worth £5,000 (€5,650), he drew out how he wanted the web-based app to look and function and engaged a developer from South West Regional College to design and develop it.
He now has three years’ worth of data and continues to use the app to this day.
Everything in the AD plant is recorded, from digestate, to feeding rates and biogas yield. He keeps a close eye on everything and produces quarterly reports on the plant’s performance.
Gavin says that he hears a lot of talk about biomethane plants being the next step for AD.
However, he argues that the 500kW biogas to electricity model is the ideal size for farmers, as they can be developed, run and supplied by farmers themselves.
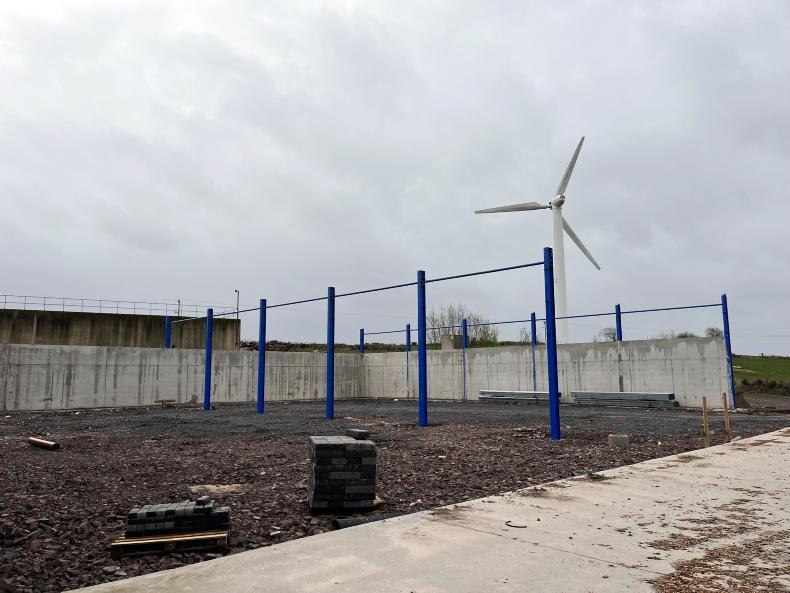
He is currently constructing a new woodchip storage shed.
Biomethane plants are significantly bigger and too large for most farmers to develop.
As a result, farmers will miss out on the chance to gain any real benefits from an AD plant, which instead will be developed by larger corporate companies.
SHARING OPTIONS: