From time to time the FTMTA executive council presents a gold award to a person who has given a long or outstanding service to the association or the agricultural machinery industry.
This award is open to all working FTMTA member firms and its staff.
The Irish Farmers Journal sat down with recent recipients the McHale brothers to discuss their road to success.
Humble beginnings
McHale was founded by Padraic and Martin McHale in the mid 1980s.
Before Padraic started manufacturing, he sold used tractors and machinery from 1976.
He was later joined in this business by his younger brother Martin. Coming from a farming background and a family of 15, the brothers knew the value of hard work.
The manufacturing company evolved from a farm machinery retail outlet that is still in existence today.
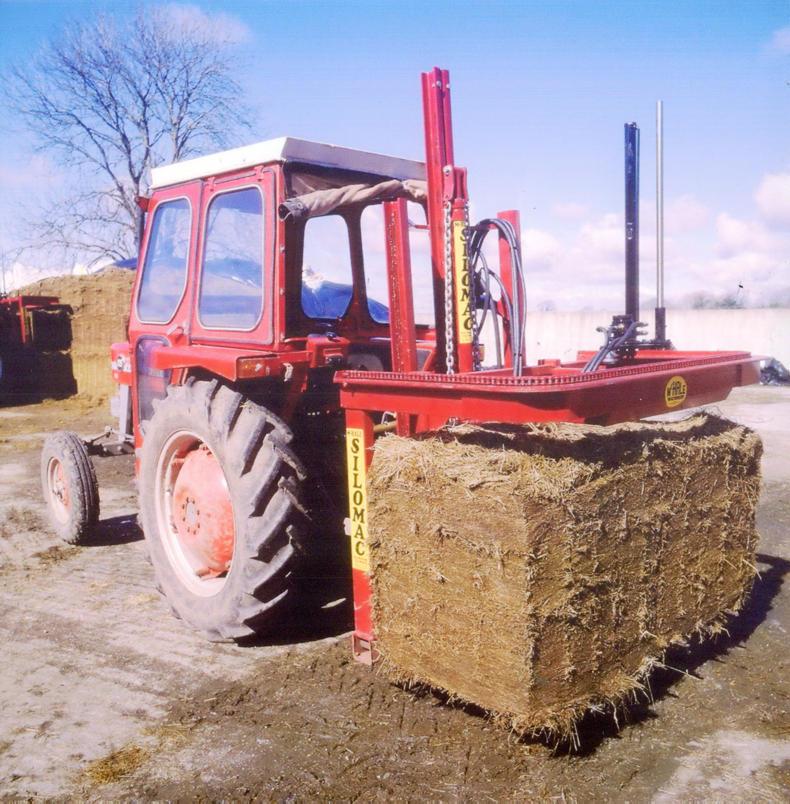
During the summer of 1982 the McHale brothers built a Silage Block Cutter and the following winter tested it on the home farm while refining it.
The brothers explained how this background was an excellent foundation for the design and manufacture of farm machinery, simply due to its direct contact with the end user.
The brothers decided to get into manufacturing when they saw a gap in the market for machinery to cut pit silage in the west of Ireland.
The following year the brothers started to manufacture and sell their blockcutters locally
At the time, imported machines found it hard to deal with the long grass in the area. As a result the brothers opted to design a machine they felt would do a better job.
During the summer of 1982 they built a silage block cutter and the following winter tested it on the home farm while refining it.
The first product was a Silomac blockcutter. A range of slurry pumping equipment followed this.
The following year the brothers started to manufacture and sell their blockcutters locally.
Later, Martin began to establish a dealer network around Ireland and after this appointed dealers in Scotland and the UK.
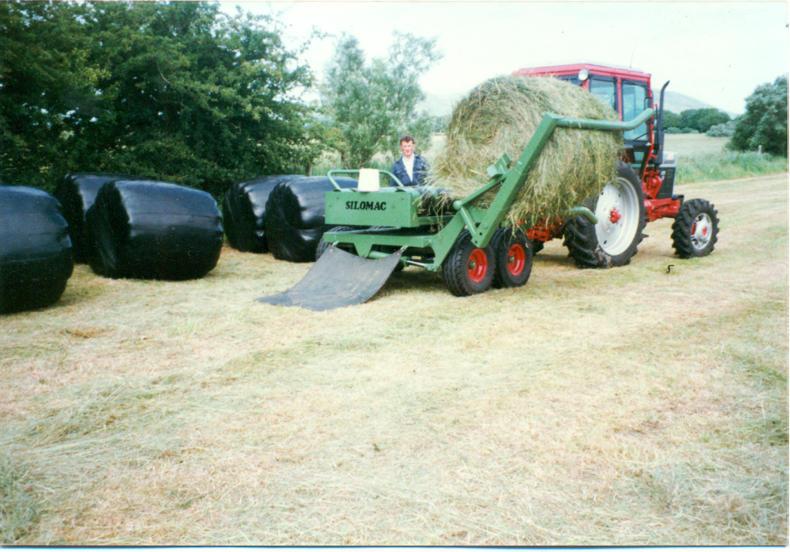
Martin McHale with one of the early bale wrappers.
One of the first more unusual markets was Iceland.
In the early days Padraic looked after product design and manufacturing while Martin looked after sales and marketing.
Although the business has grown substantially since, both brothers are still actively involved in the business and still manage these areas.
In 1987, McHale manufactured its first round bale wrapper and a few years later in 1989 made a conscious decision to specialise in this area and grow the company through market development.
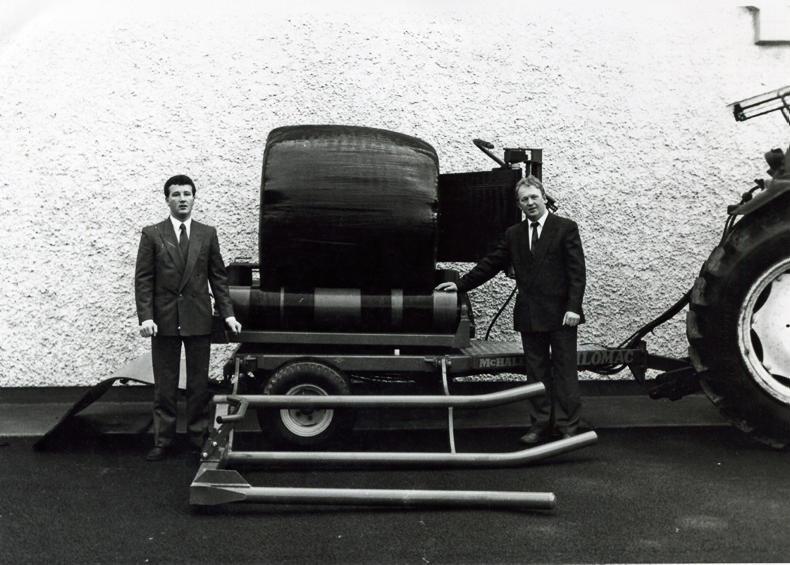
In 1987, McHale manufactured its first round bale wrapper.
Martin then travelled to the UK and began to develop a dealer network.
Today this network consists of 70 dealers, many of whom have been working with McHale for over 30 years.
Establishment of the McHale brand
Martin explained that, “in 1989 or 1990 before the first Smithfield show we had some concern about how Silomac would translate as it moved into export markets.
As a result, we decided to rebrand the range under the McHale name.”
Outside the UK, one of the first exports markets actively targeted was Australia in 1994.
Martin said: “Australia was a good move for us. The grass season in Australia started in August or September each year when the European season was coming to a close. As a result, we could keep the factory busy all year round. In addition, for a company of our size at the time all our promotional material could be used as the language was the same. Today we still follow the grass season around the world and when the season finishes in the northern hemisphere we do good business in Australia, New Zealand, South Korea, Japan, China, South Africa and Chile.”
In 1995, Martin took the McHale name to Europe when he participated at the Agritechnica Show in Hanover in Germany
In the mid 1990s McHale started working on a range of square bale wrappers for field and static wrapping, unveiling the 995 linkage and trailed square bale wrappers and later the high-output 998.
In 1995, Martin took the McHale name to Europe when he participated at the Agritechnica Show in Hanover in Germany and sought distributors across Europe.
McHale achieved ISO certification for its quality standards in 1997 and also received numerous company awards for export and performance including the AIB export award and the Wang export company award.
New factory
By 1999, the company was shipping to 25 countries. To keep up with demand, McHale relocated from its home in Kilmaine and moved seven miles over the road to a 20ac greenfield site in Ballinrobe, building a 100,000 square foot manufacturing plant.
A new research and development department was later constructed.
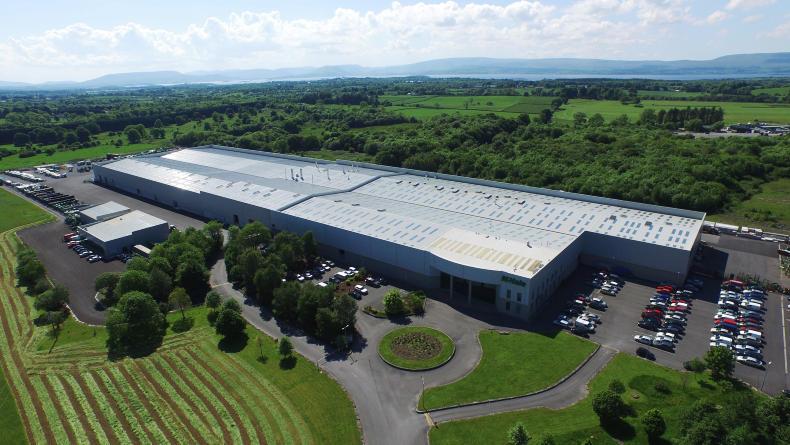
Aerial view of the McHale Manufacturing Facility in Ballinrobe.
This is still run by Padraic and a number of key engineers who have been with the company since the R&D function was formally established in 1994.
Today, over 10% of the Mayo workforce are involved in new product development.
Over the years the plant has expanded and is now 320,000 square feet (8ac of roofed area).
Birth of the Fusion
By the turn of the century, many contractors had started to tow wrappers after their balers so that both jobs could be done with one tractor and one man.
The McHale brothers saw a niche in the market.
At this stage, the brothers had 20 years’ experience with manufacturing bale wrappers and selling balers in the harsh west of Ireland conditions, often described by other European manufacturers as the most challenging in Europe due to the difficult ground conditions and the heavy rainfall.
The McHale brothers harnessed their knowledge across their dealer network as most dealers also sold some brand of baler.
The brothers explained that when they put all the information together it became clear that the market wanted a more reliable heavy-duty baler with stronger shafts, rollers, bearings and heavier chains.
Padraic said: “Down through the years we have always got great support and feedback from both our Irish dealers and customers in relation to product development and testing. This provided us with a solid foundation for the development of products which could compete on a world stage.”
Unlike a lot of other players in the market, McHale did not have a baler to start with so it was not blinded by any traditional concept.
As a result, the team developed an integrated baler wrapper, which split like a clamshell where the lower section of the bale chamber transferred the bale.
This machine was unique in that it had a vertical wrapping ring instead of the more traditional twin-rotating dispenser formation.
When combined, the patented bale transfer and vertical wrapper ring resulted in a machine that could deliver up to 15% more output from a more compact machine.
This was highlighted when the McHale design team received the prestigious Royal Agricultural Society of England’s (RASE) Gold Medal at the 2005 Royal Show.
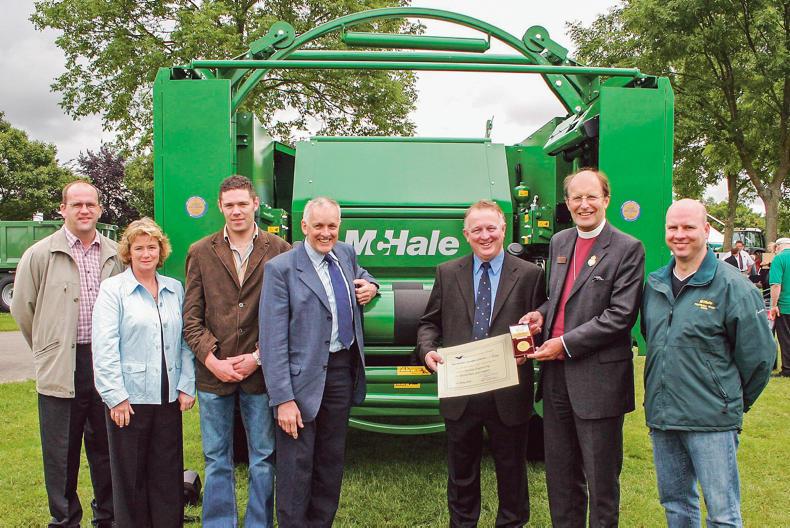
Padraic and Martina McHale with key members of the McHale R&D Team, James Heaney, Donal Collins, Patsy O’Connor and Gerry Sheridan accept the RASE Gold medal at the Royal Show.
The RASE machinery awards are unique in that they are based on a rigorous examination of machine performance by agri-contractors and farmers. These judges chose the McHale Fusion Integrated Baler Wrapper for its economy of operation, compact dimensions, its ability to work well on sloping land, high output and the company reputation.
Padraic said: “When the integrated baler wrapper was developed we described the concept to our dealer network and asked them to come up with a name and offered a trip to Ireland as a prize. Our importer in Greece came up with the Fusion name. Over time we have developed a strong brand around this name”.
Fixed chamber baler
In 2005, the company launched a standard fixed chamber baler.
The brothers explained that this machine was designed as a direct result of customer demand. They noted that the baler used 85% of the components used in the Fusion.
In 2009, the company launched the V660 variable chamber or belt baler which was targeted at drier climates
Due to its success, in 2007 a non-chopper baler, the F540, and a fully automatic baler, the F560, were also added to the range.
Over the years, the models have been superseded by the latest models in the fixed chamber baler range, namely the F5400, F5500, F5600 and F5600 Plus.
In 2009, the company launched the V660 variable chamber or belt baler which was targeted at drier climates around the world where there was demand for larger bales.
Today, McHale offers a total of nine balers in it range. This comprises three balers in the Fusion integrated range, four balers in the F5000 fixed chamber range and two balers in the V6 variable chamber range.
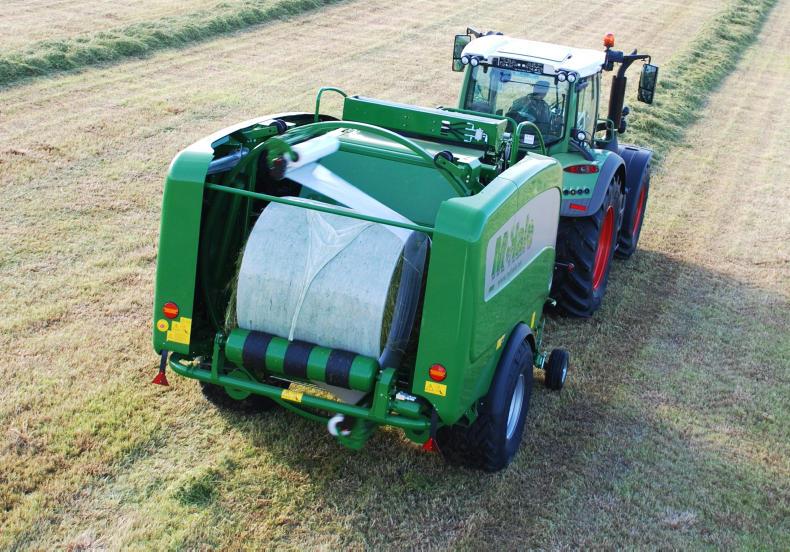
Fusion 3 Plus launched in 2013 – Innovative film binding results in better silage quality and easier to feed out bales.
In 2015 McHale widened its grass line range to include its Pro Glide range of front, rear and combination mowers.
The brothers explained that all mowers in the range have a number of key patents.
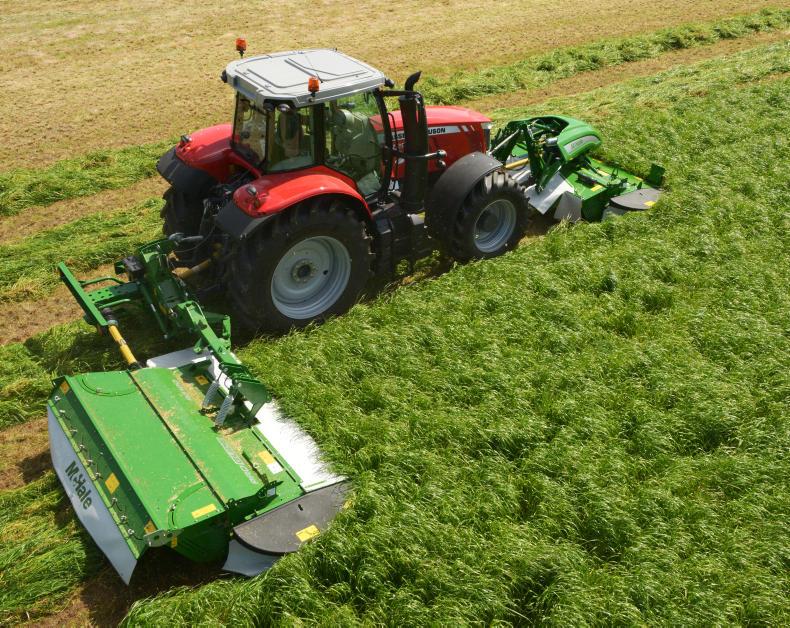
Pro Glide front and rear mower working on the factory test plot in Ballinrobe in 2015.
At the 2017 Irish Ploughing Championships McHale unveiled two models in its centre delivery rake range – the R62-72 & R68-78.
The McHale story is one of two brothers taking a voyage from humble beginnings and building a team helping to achieve worldwide commercial success.
Today, the company is one of the largest employers in the region, with exports accounting for 90% of sales.
Their products can be seen working in 55 countries around the world.
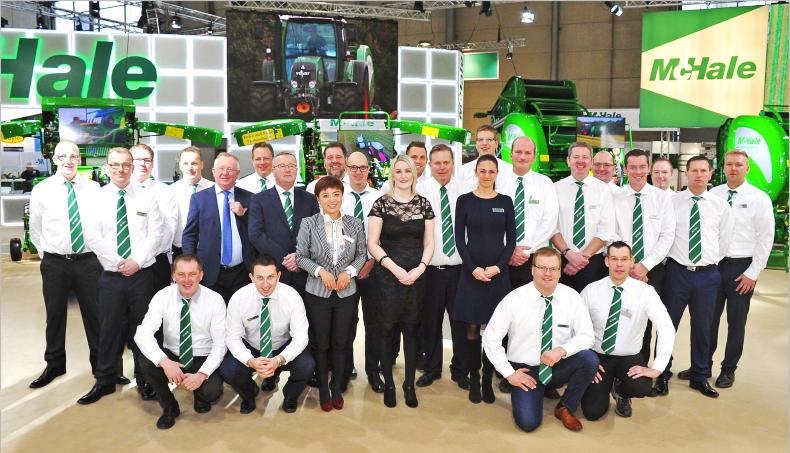
McHale sales team for the Agritechnica Show in Hanover 2017.
The brothers noted that their success can be attributed to the company’s philosophy of specialisation, intensive testing/product development with end users and a commitment to investing in research and development and the latest production technologies
Padraic emphasised that McHale is a team: “Many of the people have been with myself and Martin for between 15 and 30 years. As the business has grown these people have taken on new challenges, developed new ideas and grown the business. This team has been fundamental to our success and I would like to thank them for their continued hard work, support and commitment.”
“We are constantly looking for people to grow the team and have a number of exciting vacancies on our website which we need to fill over the coming months.”
McHale will be at the Agri Careers Expo in the RDS on 14 February.
From time to time the FTMTA executive council presents a gold award to a person who has given a long or outstanding service to the association or the agricultural machinery industry.
This award is open to all working FTMTA member firms and its staff.
The Irish Farmers Journal sat down with recent recipients the McHale brothers to discuss their road to success.
Humble beginnings
McHale was founded by Padraic and Martin McHale in the mid 1980s.
Before Padraic started manufacturing, he sold used tractors and machinery from 1976.
He was later joined in this business by his younger brother Martin. Coming from a farming background and a family of 15, the brothers knew the value of hard work.
The manufacturing company evolved from a farm machinery retail outlet that is still in existence today.
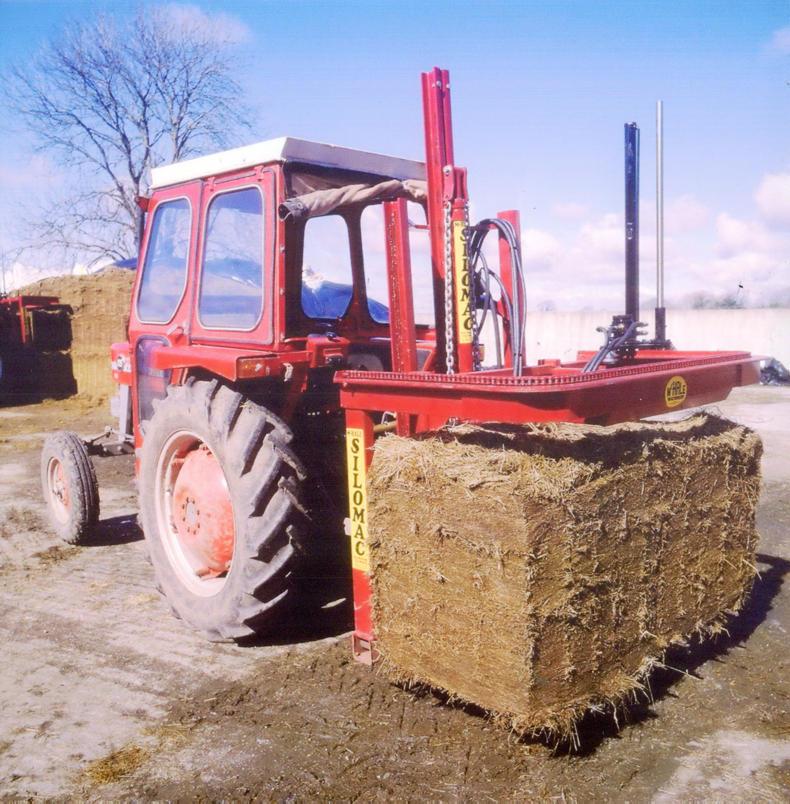
During the summer of 1982 the McHale brothers built a Silage Block Cutter and the following winter tested it on the home farm while refining it.
The brothers explained how this background was an excellent foundation for the design and manufacture of farm machinery, simply due to its direct contact with the end user.
The brothers decided to get into manufacturing when they saw a gap in the market for machinery to cut pit silage in the west of Ireland.
The following year the brothers started to manufacture and sell their blockcutters locally
At the time, imported machines found it hard to deal with the long grass in the area. As a result the brothers opted to design a machine they felt would do a better job.
During the summer of 1982 they built a silage block cutter and the following winter tested it on the home farm while refining it.
The first product was a Silomac blockcutter. A range of slurry pumping equipment followed this.
The following year the brothers started to manufacture and sell their blockcutters locally.
Later, Martin began to establish a dealer network around Ireland and after this appointed dealers in Scotland and the UK.
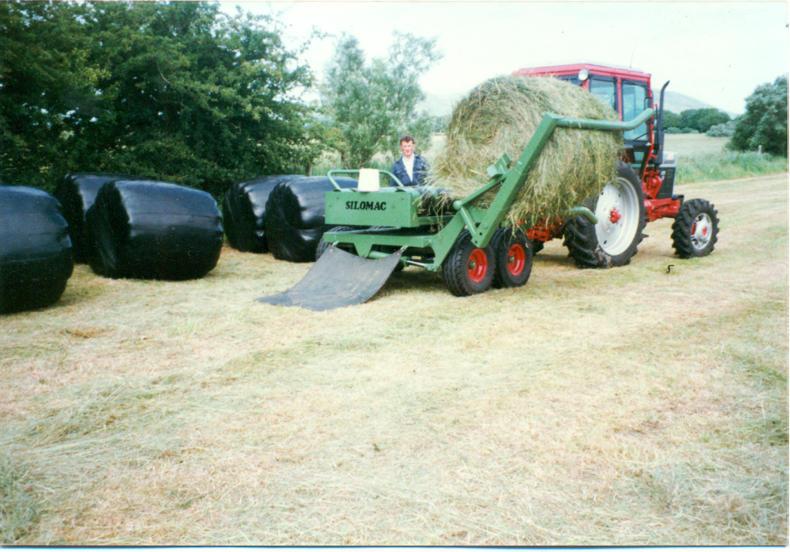
Martin McHale with one of the early bale wrappers.
One of the first more unusual markets was Iceland.
In the early days Padraic looked after product design and manufacturing while Martin looked after sales and marketing.
Although the business has grown substantially since, both brothers are still actively involved in the business and still manage these areas.
In 1987, McHale manufactured its first round bale wrapper and a few years later in 1989 made a conscious decision to specialise in this area and grow the company through market development.
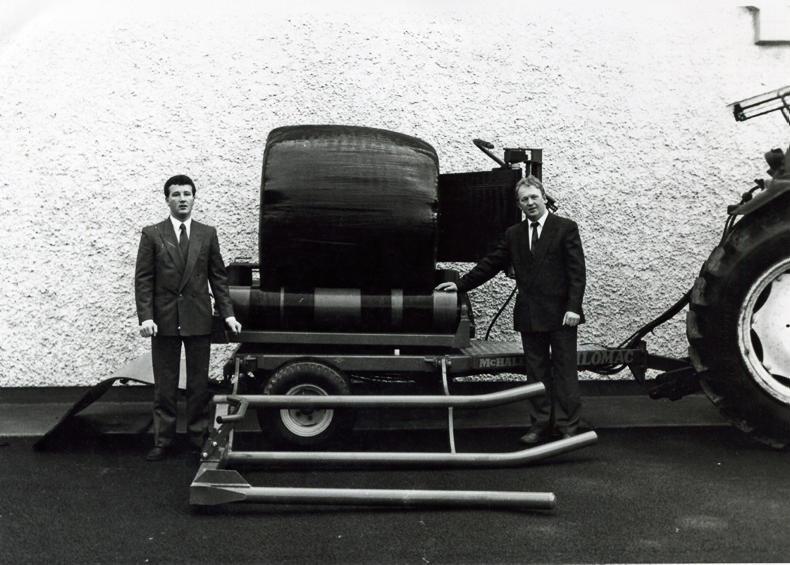
In 1987, McHale manufactured its first round bale wrapper.
Martin then travelled to the UK and began to develop a dealer network.
Today this network consists of 70 dealers, many of whom have been working with McHale for over 30 years.
Establishment of the McHale brand
Martin explained that, “in 1989 or 1990 before the first Smithfield show we had some concern about how Silomac would translate as it moved into export markets.
As a result, we decided to rebrand the range under the McHale name.”
Outside the UK, one of the first exports markets actively targeted was Australia in 1994.
Martin said: “Australia was a good move for us. The grass season in Australia started in August or September each year when the European season was coming to a close. As a result, we could keep the factory busy all year round. In addition, for a company of our size at the time all our promotional material could be used as the language was the same. Today we still follow the grass season around the world and when the season finishes in the northern hemisphere we do good business in Australia, New Zealand, South Korea, Japan, China, South Africa and Chile.”
In 1995, Martin took the McHale name to Europe when he participated at the Agritechnica Show in Hanover in Germany
In the mid 1990s McHale started working on a range of square bale wrappers for field and static wrapping, unveiling the 995 linkage and trailed square bale wrappers and later the high-output 998.
In 1995, Martin took the McHale name to Europe when he participated at the Agritechnica Show in Hanover in Germany and sought distributors across Europe.
McHale achieved ISO certification for its quality standards in 1997 and also received numerous company awards for export and performance including the AIB export award and the Wang export company award.
New factory
By 1999, the company was shipping to 25 countries. To keep up with demand, McHale relocated from its home in Kilmaine and moved seven miles over the road to a 20ac greenfield site in Ballinrobe, building a 100,000 square foot manufacturing plant.
A new research and development department was later constructed.
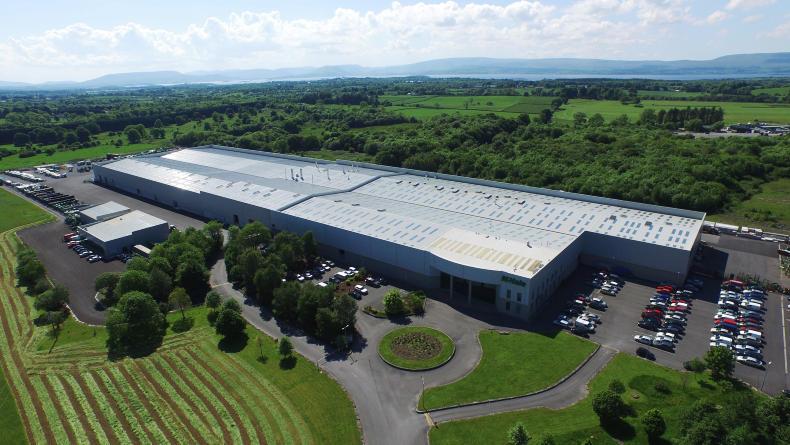
Aerial view of the McHale Manufacturing Facility in Ballinrobe.
This is still run by Padraic and a number of key engineers who have been with the company since the R&D function was formally established in 1994.
Today, over 10% of the Mayo workforce are involved in new product development.
Over the years the plant has expanded and is now 320,000 square feet (8ac of roofed area).
Birth of the Fusion
By the turn of the century, many contractors had started to tow wrappers after their balers so that both jobs could be done with one tractor and one man.
The McHale brothers saw a niche in the market.
At this stage, the brothers had 20 years’ experience with manufacturing bale wrappers and selling balers in the harsh west of Ireland conditions, often described by other European manufacturers as the most challenging in Europe due to the difficult ground conditions and the heavy rainfall.
The McHale brothers harnessed their knowledge across their dealer network as most dealers also sold some brand of baler.
The brothers explained that when they put all the information together it became clear that the market wanted a more reliable heavy-duty baler with stronger shafts, rollers, bearings and heavier chains.
Padraic said: “Down through the years we have always got great support and feedback from both our Irish dealers and customers in relation to product development and testing. This provided us with a solid foundation for the development of products which could compete on a world stage.”
Unlike a lot of other players in the market, McHale did not have a baler to start with so it was not blinded by any traditional concept.
As a result, the team developed an integrated baler wrapper, which split like a clamshell where the lower section of the bale chamber transferred the bale.
This machine was unique in that it had a vertical wrapping ring instead of the more traditional twin-rotating dispenser formation.
When combined, the patented bale transfer and vertical wrapper ring resulted in a machine that could deliver up to 15% more output from a more compact machine.
This was highlighted when the McHale design team received the prestigious Royal Agricultural Society of England’s (RASE) Gold Medal at the 2005 Royal Show.
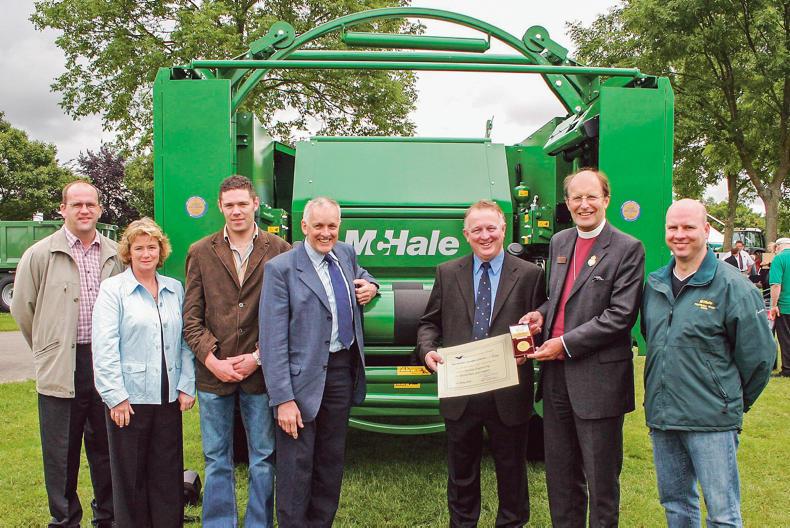
Padraic and Martina McHale with key members of the McHale R&D Team, James Heaney, Donal Collins, Patsy O’Connor and Gerry Sheridan accept the RASE Gold medal at the Royal Show.
The RASE machinery awards are unique in that they are based on a rigorous examination of machine performance by agri-contractors and farmers. These judges chose the McHale Fusion Integrated Baler Wrapper for its economy of operation, compact dimensions, its ability to work well on sloping land, high output and the company reputation.
Padraic said: “When the integrated baler wrapper was developed we described the concept to our dealer network and asked them to come up with a name and offered a trip to Ireland as a prize. Our importer in Greece came up with the Fusion name. Over time we have developed a strong brand around this name”.
Fixed chamber baler
In 2005, the company launched a standard fixed chamber baler.
The brothers explained that this machine was designed as a direct result of customer demand. They noted that the baler used 85% of the components used in the Fusion.
In 2009, the company launched the V660 variable chamber or belt baler which was targeted at drier climates
Due to its success, in 2007 a non-chopper baler, the F540, and a fully automatic baler, the F560, were also added to the range.
Over the years, the models have been superseded by the latest models in the fixed chamber baler range, namely the F5400, F5500, F5600 and F5600 Plus.
In 2009, the company launched the V660 variable chamber or belt baler which was targeted at drier climates around the world where there was demand for larger bales.
Today, McHale offers a total of nine balers in it range. This comprises three balers in the Fusion integrated range, four balers in the F5000 fixed chamber range and two balers in the V6 variable chamber range.
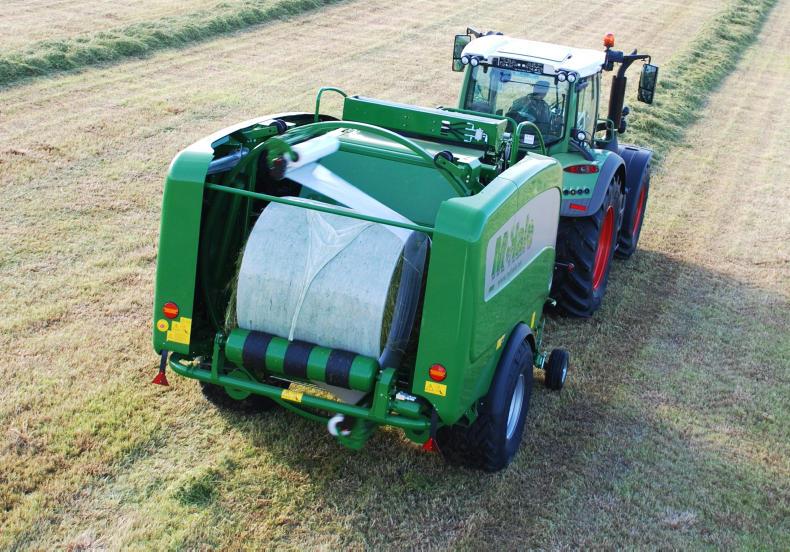
Fusion 3 Plus launched in 2013 – Innovative film binding results in better silage quality and easier to feed out bales.
In 2015 McHale widened its grass line range to include its Pro Glide range of front, rear and combination mowers.
The brothers explained that all mowers in the range have a number of key patents.
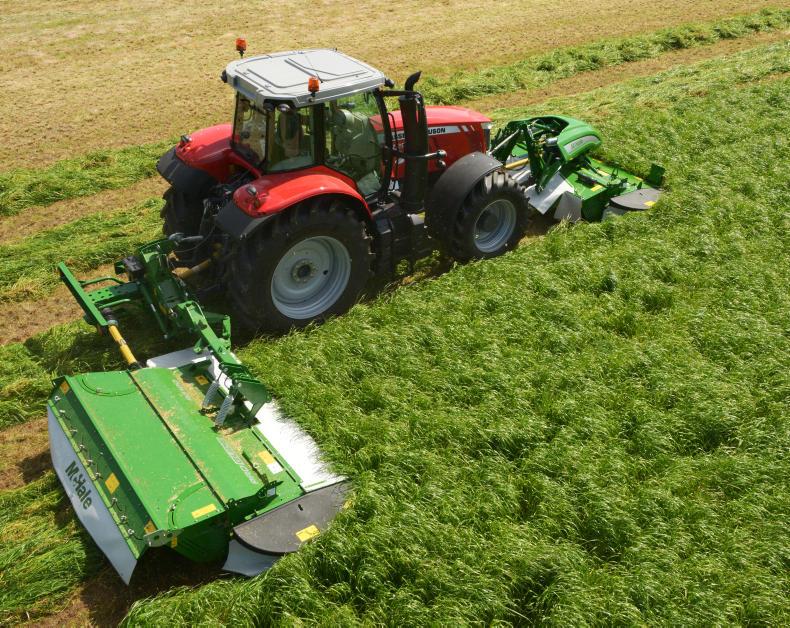
Pro Glide front and rear mower working on the factory test plot in Ballinrobe in 2015.
At the 2017 Irish Ploughing Championships McHale unveiled two models in its centre delivery rake range – the R62-72 & R68-78.
The McHale story is one of two brothers taking a voyage from humble beginnings and building a team helping to achieve worldwide commercial success.
Today, the company is one of the largest employers in the region, with exports accounting for 90% of sales.
Their products can be seen working in 55 countries around the world.
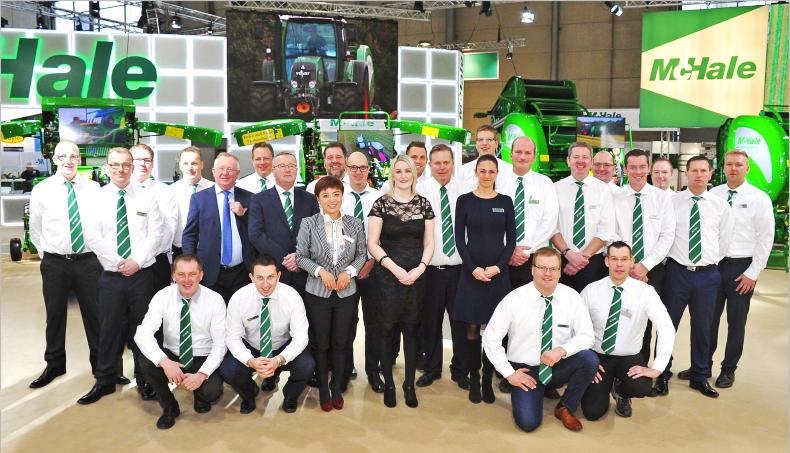
McHale sales team for the Agritechnica Show in Hanover 2017.
The brothers noted that their success can be attributed to the company’s philosophy of specialisation, intensive testing/product development with end users and a commitment to investing in research and development and the latest production technologies
Padraic emphasised that McHale is a team: “Many of the people have been with myself and Martin for between 15 and 30 years. As the business has grown these people have taken on new challenges, developed new ideas and grown the business. This team has been fundamental to our success and I would like to thank them for their continued hard work, support and commitment.”
“We are constantly looking for people to grow the team and have a number of exciting vacancies on our website which we need to fill over the coming months.”
McHale will be at the Agri Careers Expo in the RDS on 14 February.
SHARING OPTIONS: