Situated along the coast of Larne, Co Antrim, James Moore farms alongside his father Samuel and brother Johnathan. The main farm enterprises are dairy and sheep, comprising 250 pedigree Holstein cows and a flock of 100 Dorest ewes. Milking cows three times daily on a largely indoor platform sees a considerable reliance on good-quality silage.
The Moores felt the best way to ensure quality was to start cutting their own silage which first started in the 1970s after they bought a single-chop harvester. Today, a Pöttinger Jumbo 6010 forage wagon is responsible for most of the silage made on farm. Last year, a combination baler was bought for a number of reasons.
The primary reasons was an influx in the number of bales made annually, partly due to limited pit space and increased cow numbers on the farm. Although the forage wagon was present on farm, James felt the time consumed opening and resealing the pit for strong paddocks coming out of the rotation and the later fourth and fifth cuts was a non-runner. On the other hand, bales suit their farming system for the purposes of buffer feeding.
Why Pöttinger?
While scouting the baler market, James insisted on a machine with as short of chop length. “We tend to feed the sheep bales so a short chop is important for intakes as well as handling. The more cleans cuts and the higher the density of the bales, the better from a preservation point of view. Tightly packed bales are equally as important as a well-rolled silage pit from a preservation point of view.
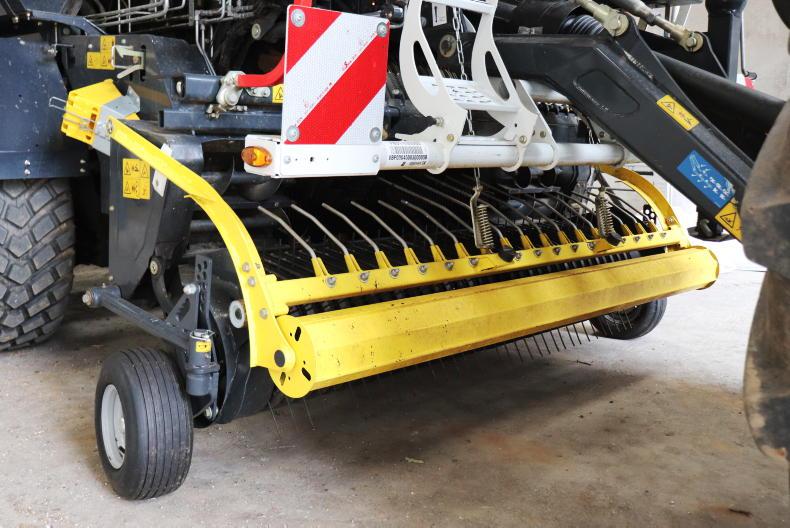
The Impress 125 FC Pro is fitted with a 2.3m wide pickup.
A baler-wrapper combination was the machine of choice based on machinery and labour resources. The two brands that appealed to James were Pöttinger and Kuhn, the Pöttinger in particular based on its 32-knife chopping unit. However, a Kuhn i-Bio and Pöttinger Impress 125 FC Pro were demonstrated.
Both balers performed well but what seriously impressed James was the performance of the chopping unit, in addition to the build and design of the baler. After striking a deal, the Moores’ baler arrived last April.
Pickup
The Impress 125 FC Pro is fitted with a 2.3m pickup reel comprising five rows of tines and fixed guide wheels which do not need to be removed for transport. Pöttinger suspends its pickups centrally, meaning it has the ability to pivot 120mm to the sides in a pendulum motion to adapt to ground contours.
The pickup can be set to automatically lift while film/net binding is taking place.
The intake rotor is closely positioned to the pickup reel, a feature James felt was important providing short leafy grass is what’s baled predominantly. The rotor measures 650mm in diameter and 1.15m in width. Supporting the pickup are twin augers on either side, ensuring material is fed through the rotor.
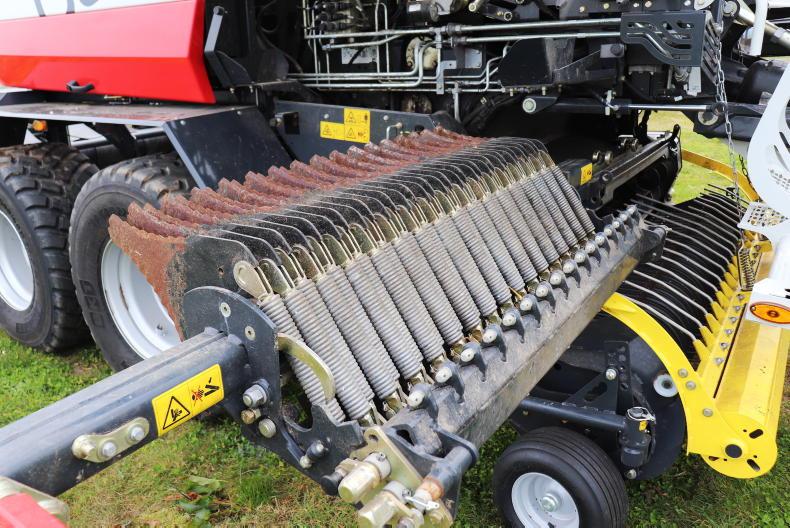
Each of the 32 knives are individually spring protected.
Unlike almost all other balers on the market, Pöttinger rotates its rotor upwards, feeding the crop over it and through the chopping unit before entering the chamber. The knock-on effect of this is the positioning of the knife bank above the rotor presenting itself for ease of access, a super feature, James pointed out. The drawbar on James’s baler is equipped with the hydraulic drawbar.
Chopping unit
The positioning of the chopping unit has two main benefits. Firstly, crop flows directly into the baler and doesn’t follow the traditional curved path. This, James feels, is key to its intake capabilities. The second benefit is a cleaner cut as the knives are positioned above the rotor and therefore slots cannot collect debris.
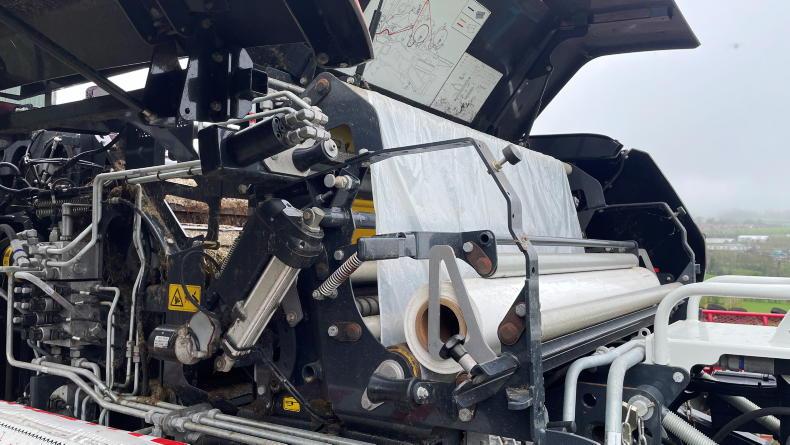
Both film and net binding is supported with the Impress.
The knife bank contains a maximum of 32 knives through two groups of 16. Every knife is individually spring-loaded for protection purposes. Knife groups can be set up in numerous configurations depending on the operator or customers requirements. While the knife bank can be moved in and out of working position through the terminal, switching between knife groups is done manually on James’s machine. He tends to run the full 32 knives for the shortest 36mm theoretical chop.
“Leaving chop length aside, the difference we noticed between running 16 and 32 knives is density. The 32-knife bales weighed up to 950kg, a full 100kg more than the bales chopped with 16 knives.”
Once the knife bank is disengaged and its rams removed, it pulls right out to the side like a drawer using the same principle as the brand’s forage wagons. “The knife bank slides on rollers, leaving it pretty much effortless. With the knives being reversible, I can have the bank pulled out and all knives rotated in a matter of minutes. If this was the case with all balers I think we’d see contractors sharpening knives more often.”

The Expert 75 Isobus terminal is clear and easily navigated through.
Chamber and binding
The bale chamber is fitted with 18 rollers and is capable of producing bales 1.20m in width and 1.25m in diameter. Roller wall thickness ranges from 3.5mm to 4.5mm, with the latter located to the front to withstand greater load.
James’s machine is capable of film binding in addition to traditional net binding. Switching between the two binding options is done manually according to James, although he tends to only use the film. “The film application process is fast. As well as binding the bale better, which is important with such a fine chop, the film helps the bale preserve better. Although there was a two-roll dispenser option, it wasn’t something we needed.”
Bale shape and density is another trait James likes about the Impress baler. Through the terminal, density can be adjusted depending on the crop. Sensors monitor the density within the chamber and display a fill percentage as well as arrows to indicate whether the operator needs to keep left or right on the swath to fill the respective side of the chamber and produce an even bale.
Bale transfer and wrapper
Once ejected from the chamber, bales are transferred via the linear transfer system and loaded on to the tilted wrapping table. Guide bars are fitted to prevent the bales from twisting. The wrapping arm is controlled from below in order to keep gravity low according to Pöttinger. At 36rpm, James described the wrapper as fast. Cameras allow the process to be monitored from the cab.
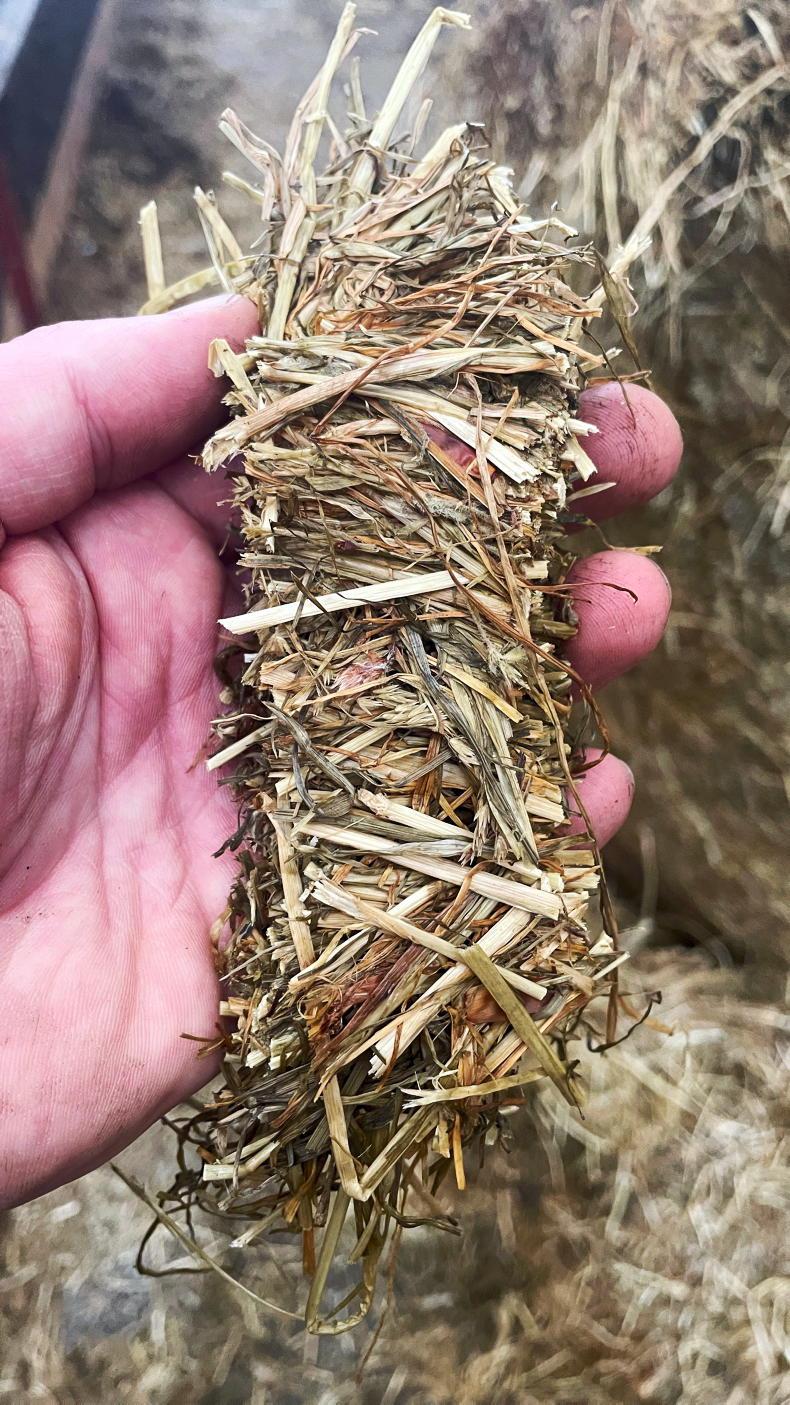
With the full 32 knives a 36mm chop length is possible.
In the event of wrap tearing, it is detected and bale rotation speed is automatically reduced so that the correct number of layers are applied with only the one roll. Rear-mounted controls are fitted as standard to operate all wrapper functions from ground level.
Under the side panels there is capacity to carry 12 additional rolls of wrap. These holders raise and lower hydraulically. Below this there is space for one roll of net or binding film.
Controls
Like almost all balers nowadays, the Impress is fully automatic, from binding right through to wrapping and drop-off. However, the option is there to work the baler and wrapper combination manually.
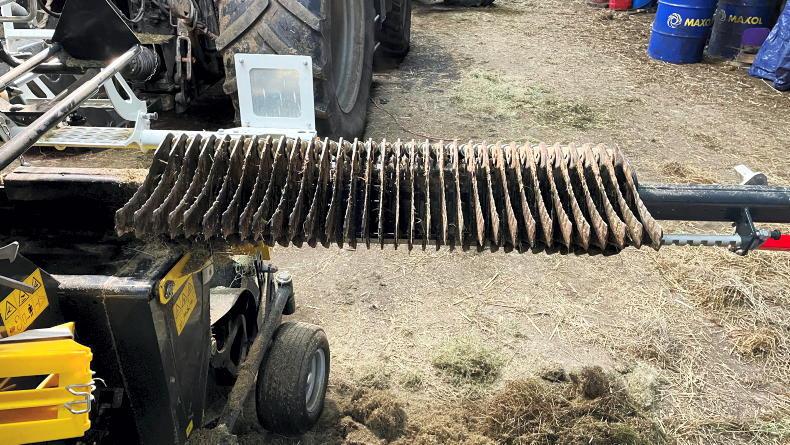
The drawer like knife bank pulls out to the side for access.
In addition to full Isobus control, Pöttinger offers three terminal options, Power Control, Expert 75 Isobus terminal or the CCI 1200 Isobus terminal. James opted for the Expert 75 display which he feels is easily used and navigated through. It is fitted with a 5.6in display which can be operated via touchscreen or using the keys and scroll wheel provided. All functions can be operated using the terminal via load sensing.
After one full season of use and over 2,000 bales made, the Moores are well impressed (pun intended) by the baler wrapper combination.
“We were pleased with how it performed all summer. The real proof was the quality of bale produced when it came to feeding. Once the wrap and film is removed the bale just disintegrates.
“In addition to the 1,500 bales we made for ourselves, we baled over 500 bales for neighbouring farmers. One of whom is a sheep farmer who makes haylage and loves the consistently short chop.
“It’s a well built and engineered machine which I am confident will last us for many years. The ongoing service provided by our local dealers Hunter Kane & Son was key in sticking with the brand,” James outlined.
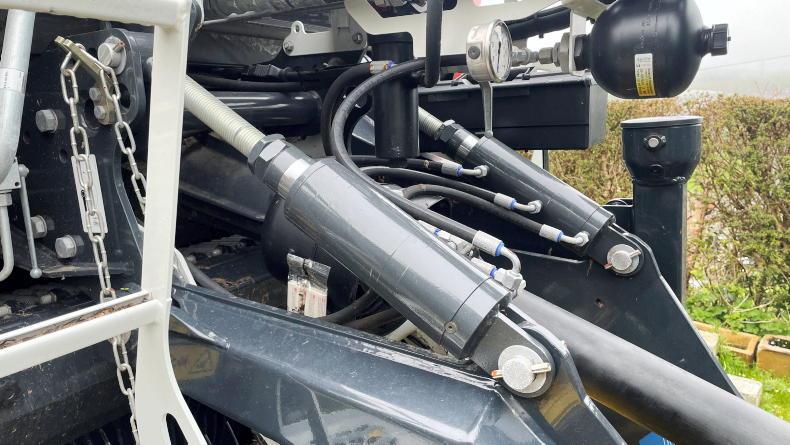
James opted for the optional hydraulic drawbar.
Weight: 7,600kg.
Tyres: 520/55 R22.5.
Knives: 32 knives, two banks of 16 knives.
Bale chamber: 18 rollers.
Terminal: Expert 75 Isobus 5.6in.
Pickup: 2.3m, five-tine bar.
Feed rotor diameter: 650mm x 1.15m.
Length: 7.24m (23.8ft).
Width: 2.89m (9.5ft).
Situated along the coast of Larne, Co Antrim, James Moore farms alongside his father Samuel and brother Johnathan. The main farm enterprises are dairy and sheep, comprising 250 pedigree Holstein cows and a flock of 100 Dorest ewes. Milking cows three times daily on a largely indoor platform sees a considerable reliance on good-quality silage.
The Moores felt the best way to ensure quality was to start cutting their own silage which first started in the 1970s after they bought a single-chop harvester. Today, a Pöttinger Jumbo 6010 forage wagon is responsible for most of the silage made on farm. Last year, a combination baler was bought for a number of reasons.
The primary reasons was an influx in the number of bales made annually, partly due to limited pit space and increased cow numbers on the farm. Although the forage wagon was present on farm, James felt the time consumed opening and resealing the pit for strong paddocks coming out of the rotation and the later fourth and fifth cuts was a non-runner. On the other hand, bales suit their farming system for the purposes of buffer feeding.
Why Pöttinger?
While scouting the baler market, James insisted on a machine with as short of chop length. “We tend to feed the sheep bales so a short chop is important for intakes as well as handling. The more cleans cuts and the higher the density of the bales, the better from a preservation point of view. Tightly packed bales are equally as important as a well-rolled silage pit from a preservation point of view.
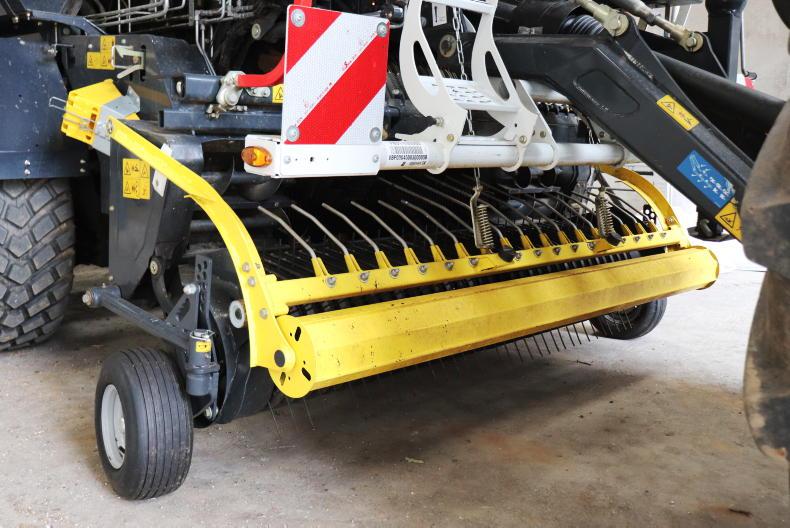
The Impress 125 FC Pro is fitted with a 2.3m wide pickup.
A baler-wrapper combination was the machine of choice based on machinery and labour resources. The two brands that appealed to James were Pöttinger and Kuhn, the Pöttinger in particular based on its 32-knife chopping unit. However, a Kuhn i-Bio and Pöttinger Impress 125 FC Pro were demonstrated.
Both balers performed well but what seriously impressed James was the performance of the chopping unit, in addition to the build and design of the baler. After striking a deal, the Moores’ baler arrived last April.
Pickup
The Impress 125 FC Pro is fitted with a 2.3m pickup reel comprising five rows of tines and fixed guide wheels which do not need to be removed for transport. Pöttinger suspends its pickups centrally, meaning it has the ability to pivot 120mm to the sides in a pendulum motion to adapt to ground contours.
The pickup can be set to automatically lift while film/net binding is taking place.
The intake rotor is closely positioned to the pickup reel, a feature James felt was important providing short leafy grass is what’s baled predominantly. The rotor measures 650mm in diameter and 1.15m in width. Supporting the pickup are twin augers on either side, ensuring material is fed through the rotor.
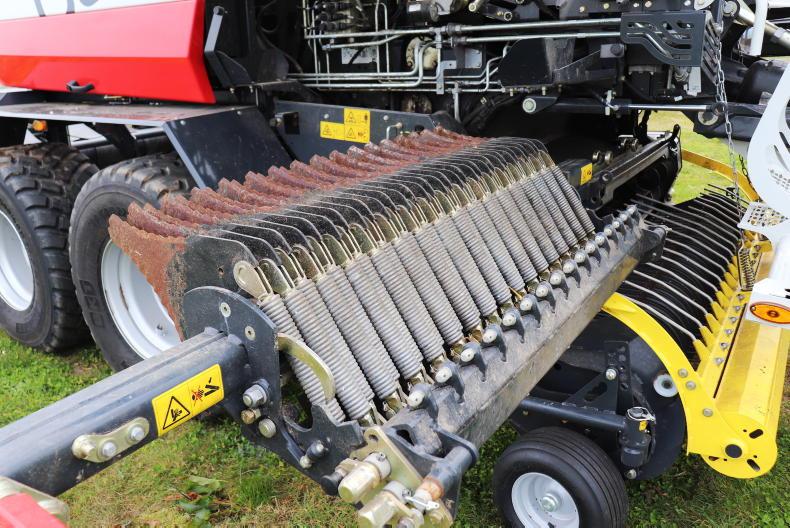
Each of the 32 knives are individually spring protected.
Unlike almost all other balers on the market, Pöttinger rotates its rotor upwards, feeding the crop over it and through the chopping unit before entering the chamber. The knock-on effect of this is the positioning of the knife bank above the rotor presenting itself for ease of access, a super feature, James pointed out. The drawbar on James’s baler is equipped with the hydraulic drawbar.
Chopping unit
The positioning of the chopping unit has two main benefits. Firstly, crop flows directly into the baler and doesn’t follow the traditional curved path. This, James feels, is key to its intake capabilities. The second benefit is a cleaner cut as the knives are positioned above the rotor and therefore slots cannot collect debris.
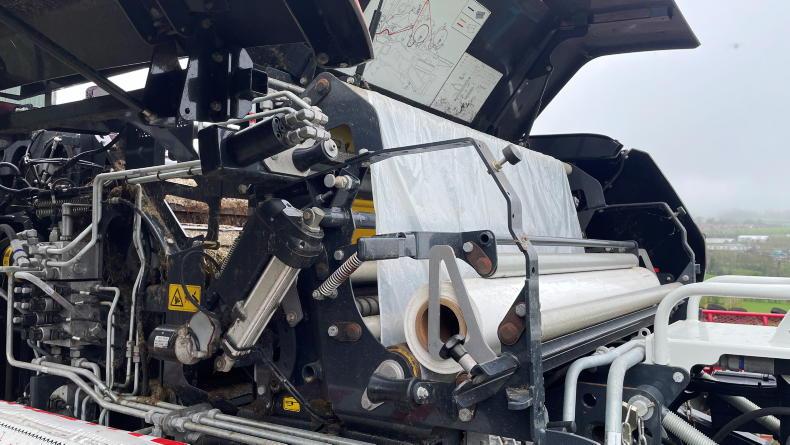
Both film and net binding is supported with the Impress.
The knife bank contains a maximum of 32 knives through two groups of 16. Every knife is individually spring-loaded for protection purposes. Knife groups can be set up in numerous configurations depending on the operator or customers requirements. While the knife bank can be moved in and out of working position through the terminal, switching between knife groups is done manually on James’s machine. He tends to run the full 32 knives for the shortest 36mm theoretical chop.
“Leaving chop length aside, the difference we noticed between running 16 and 32 knives is density. The 32-knife bales weighed up to 950kg, a full 100kg more than the bales chopped with 16 knives.”
Once the knife bank is disengaged and its rams removed, it pulls right out to the side like a drawer using the same principle as the brand’s forage wagons. “The knife bank slides on rollers, leaving it pretty much effortless. With the knives being reversible, I can have the bank pulled out and all knives rotated in a matter of minutes. If this was the case with all balers I think we’d see contractors sharpening knives more often.”

The Expert 75 Isobus terminal is clear and easily navigated through.
Chamber and binding
The bale chamber is fitted with 18 rollers and is capable of producing bales 1.20m in width and 1.25m in diameter. Roller wall thickness ranges from 3.5mm to 4.5mm, with the latter located to the front to withstand greater load.
James’s machine is capable of film binding in addition to traditional net binding. Switching between the two binding options is done manually according to James, although he tends to only use the film. “The film application process is fast. As well as binding the bale better, which is important with such a fine chop, the film helps the bale preserve better. Although there was a two-roll dispenser option, it wasn’t something we needed.”
Bale shape and density is another trait James likes about the Impress baler. Through the terminal, density can be adjusted depending on the crop. Sensors monitor the density within the chamber and display a fill percentage as well as arrows to indicate whether the operator needs to keep left or right on the swath to fill the respective side of the chamber and produce an even bale.
Bale transfer and wrapper
Once ejected from the chamber, bales are transferred via the linear transfer system and loaded on to the tilted wrapping table. Guide bars are fitted to prevent the bales from twisting. The wrapping arm is controlled from below in order to keep gravity low according to Pöttinger. At 36rpm, James described the wrapper as fast. Cameras allow the process to be monitored from the cab.
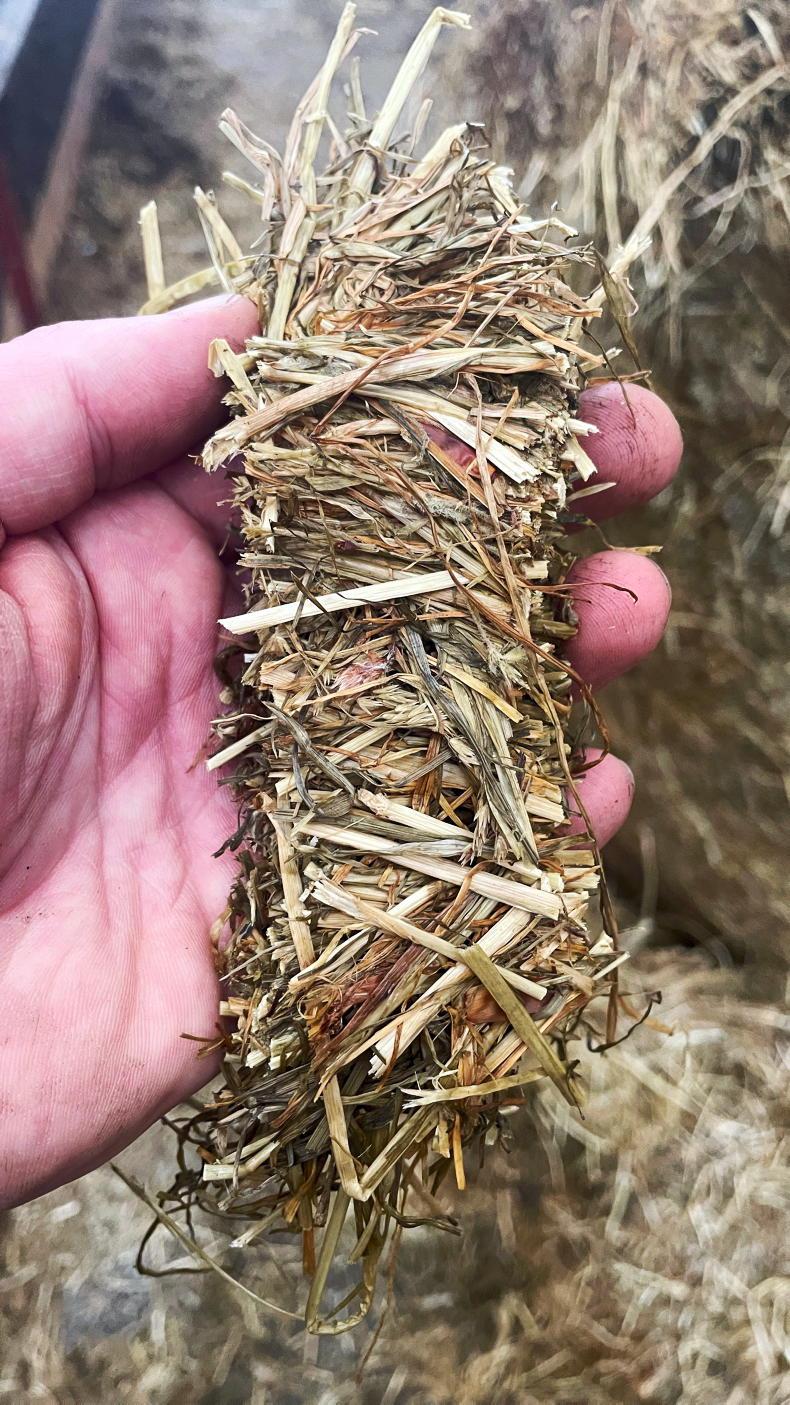
With the full 32 knives a 36mm chop length is possible.
In the event of wrap tearing, it is detected and bale rotation speed is automatically reduced so that the correct number of layers are applied with only the one roll. Rear-mounted controls are fitted as standard to operate all wrapper functions from ground level.
Under the side panels there is capacity to carry 12 additional rolls of wrap. These holders raise and lower hydraulically. Below this there is space for one roll of net or binding film.
Controls
Like almost all balers nowadays, the Impress is fully automatic, from binding right through to wrapping and drop-off. However, the option is there to work the baler and wrapper combination manually.
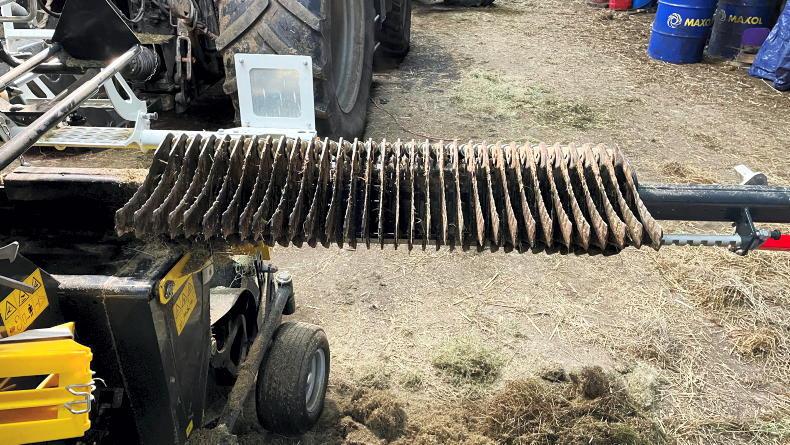
The drawer like knife bank pulls out to the side for access.
In addition to full Isobus control, Pöttinger offers three terminal options, Power Control, Expert 75 Isobus terminal or the CCI 1200 Isobus terminal. James opted for the Expert 75 display which he feels is easily used and navigated through. It is fitted with a 5.6in display which can be operated via touchscreen or using the keys and scroll wheel provided. All functions can be operated using the terminal via load sensing.
After one full season of use and over 2,000 bales made, the Moores are well impressed (pun intended) by the baler wrapper combination.
“We were pleased with how it performed all summer. The real proof was the quality of bale produced when it came to feeding. Once the wrap and film is removed the bale just disintegrates.
“In addition to the 1,500 bales we made for ourselves, we baled over 500 bales for neighbouring farmers. One of whom is a sheep farmer who makes haylage and loves the consistently short chop.
“It’s a well built and engineered machine which I am confident will last us for many years. The ongoing service provided by our local dealers Hunter Kane & Son was key in sticking with the brand,” James outlined.
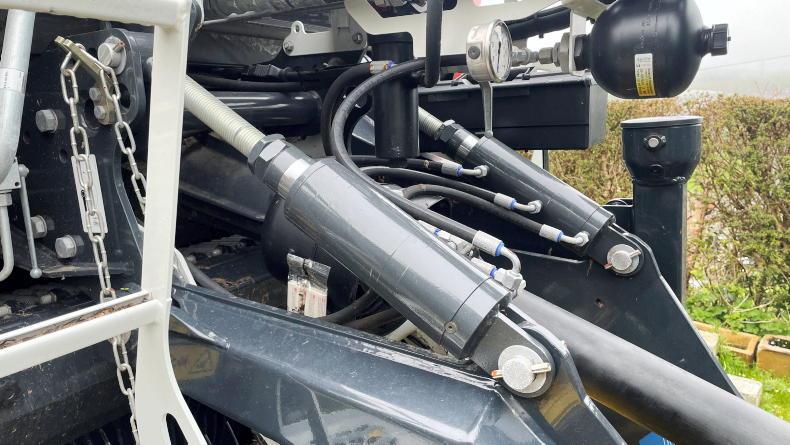
James opted for the optional hydraulic drawbar.
Weight: 7,600kg.
Tyres: 520/55 R22.5.
Knives: 32 knives, two banks of 16 knives.
Bale chamber: 18 rollers.
Terminal: Expert 75 Isobus 5.6in.
Pickup: 2.3m, five-tine bar.
Feed rotor diameter: 650mm x 1.15m.
Length: 7.24m (23.8ft).
Width: 2.89m (9.5ft).
SHARING OPTIONS: